Environmentally Friendly Structural Steel Buildings Eco Friendly Low Carbon
2024-4-12 17:14:08
No Pics.
Introduction
Environmentally Friendly Structural Steel Buildings Eco-Friendly Low Carbon
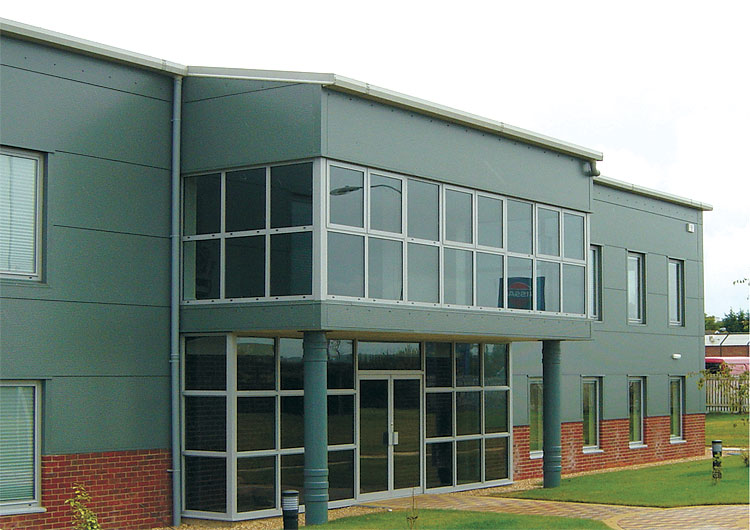
environmentally friendly steel buildings Steel buildings are intrinsically ‘green’ environmentally friendly buildings as they can be taken down almost entirely and their materials recycled.
Other aspects which can be added to our steel buildings include:
Wind turbines fitted along the ridge
Solar panels fitted onto the whole huge roofs
Our buildings can also be designed to incorporate the growing of green lawns or gardens on their large roofs, up to the size of football pitches, if wanted.
Low Carbon Buildings – Target Zero Carbon Construction
Thermal Mass in Buildings
Sustainability of steel
Frequently asked questions
Constructional Steelwork Association members are frequently asked questions about the sustainability of steel as a construction product, its recycled content and carbon footprint together with wider environmental questions on their business activities.
Below are a series of commonly asked questions together with answers that have been created with the intention of being used by members to support pre-qualification questions on the use of steel in sustainable construction.
Read PDF which includes explanation from Constructional Steelwork Association regarding steel sector commitment to helping construction industry assess the environmental performance of materials.
Is steel construction sustainable?
Steel is arguably the most sustainable of the major structural materials. It has numerous sustainability benefits, which are guaranteed to be realised whenever steel is used. They include: low waste, flexibility, offsite manufacture, speed, resource efficiency, adaptability, demountability, long lasting appeal, safety, reusability and recyclability.
These inherent characteristics result in many social, environmental and economic benefits to satisfy sustainability’s ‘triple bottom line’.
What are the sustainability benefits of steel during construction?
Steel is a fast, safe construction material. Reduced time on site means lower costs, quicker returns and less disruption to the local community. Steel is manufactured offsite in a safe, factory environment and arrives on site when needed, making it predictable with no unpleasant surprises.
There is no site waste and any waste that is generated earlier in the process is easily returned to the steel supply chain. Steel treads lightly on the ground. It has high strength to weight ratio and is resource efficient. Fewer deliveries mean reduced emissions.
What are the sustainability benefits of steel in operation?
People like a steel built environment, which is light, open, airy and adaptable. Steel structures mature with age, rather than deteriorate and decay. Steel’s long clear spans mean that interiors can be changed with ease. Steel frames can readily be adapted and reconfigured to give old buildings a new lease of life. The longevity of a building is fundamental to its overall sustainability
What are the sustainability benefits of steel at end of life? Steel structures are inherently reusable in full or part. Whole buildings can be taken down and rebuilt elsewhere or individual elements can be reused. An increasing number of buildings are being designed with this in mind, but reuse is an option for steel structures without any special provision. Any steel which is not reused is captured and recycled for further use in construction or elsewhere.
Most construction materials can be recycled, why is steel any different? Most other materials are recycled once to a lesser use. This is referred to as downcycling. Steel can be recycled indefinitely without loss of property or performance. This is referred to as multicycling. It means steel always has a value, which guarantees that virtually none is ever disposed of to landfill. The multicycling of steel is a self-sustaining system that predates modern appreciation of environmental issues and would continue in the unlikely event that they should ever lessen in importance.
How much steel is recycled?
Over 500 million tonnes of steel are multicycled worldwide each year – equivalent to 180 Eiffel Towers every day. The recovery rates are high. Research shows that 99% of structural steel arising from demolition sites in the UK is recycled or re-used.
There is a conservative estimate that over 80% of all steel scrap that becomes available each year is captured and recycled. This figure increases in poorer economies where the relative value of steel is higher.
Should steel be specified by recycled content?
Recycled content is a driver to encourage recycling of materials which would otherwise be disposed of. However, it is not a suitable driver for metals that are already recovered and recycled close to their maximum. Specifying recycled content for steel does not have any beneficial environmental effect, but can distort the market and result in unnecessary transport costs and emissions. All steel is recyclable and will be multicycled many times without any artificial stimulus.
What figure should be used as the recycled content of structural steel?
Recycled content varies by process route. Most large scale modern steelmaking processes produce steel with a significant recycled content, as scrap steel is a standard input.
When a figure is needed to calculate overall recycled content of a building, the Waste Resource Action Programme (WRAP) recommends applying a value of 60% recycled content for structural steel sourced.
What are the economic sustainable benefits of steel?
It is accepted that, to be sustainable, a solution needs a sound economic basis. Steel is fast, efficient, predictable and safe. Production is highly automated and site operations are not labour intensive. Steel is the cost effective solution and delivers long term value through flexibility, adaptability and lasting appeal.
What are the social sustainable benefits of steel?
Steel construction is fast, clean and relatively quiet, so disruption of the community is kept to a minimum. Steel construction is carried out by small teams of skilled workers in a consistent manner which is predictable and safe. Steel is manufactured and fabricated offsite, so workers are stably employed in good conditions.
All steel works and major fabrication premises are integrated into their local communities and in the case of the bigger sites are the reason that the community exists. The steel built environment is light, airy, pleasant and popular with people.
What is the steel construction industry doing to encourage and support sustainable development?
Constructional Steelwork Association have recently embarked on a major new initiative to help make zero carbon buildings a reality. The ‘Target Zero’ project will provide the construction industry with the guidance it needs to meet the emissions reduction targets towards the aspiration of zero carbon by 2019.
The Target Zero project will look at five major building types (school, warehouse, office, supermarket and mixed-use development) and will generate fully-costed solutions demonstrating how to achieve the three highest ratings and meet the changes to Part L of the Building Regulations.
How is Constructional Steelwork Association tackling climate change?
Constructional Steelwork Association and our customers are addressing climate change on a local scale by continually making our processes more and more efficient. Since 2000, there has been an 11% reduction in the energy required to produce steel which has contributed to an overall reduction of 50% over the last 40 years.
Through optimising the use of process gases arising at our plants, Constructional Steelwork Association has achieved very high levels of on-site generation of electricity. In 2007, on-site generation produced almost 1,600 GWh of electrical energy. The effect of these efforts is a reduction of approximately 700,000 tonnes of CO2 emissions from the electricity generation sector.
As a partner in the Ultra-low CO2 Steelmaking (ULCOS) programme, an initiative to achieve a step change reduction in emissions.
Can the benefit of thermal mass be realised with a steel framed building?
The thermal mass of a building can be used to reduce the requirement for active heating and cooling. People instinctively associate the cool inside churches with their mass, but it has far more to do with the lack of windows and low solar gain along with an absence of heat generating electrical equipment and lighting.
Optimum thermal mass is mobilised from the first 100mm thickness of concrete floor slab, which is available in standard steel-framed construction. The extra mass associated with heavier weight structures is a waste, which is compounded by the larger foundations required.
What is the carbon footprint of structural steel?
The CO2 emitted during the production of one tonne of structural sections is 0.76 tonnes. This value is higher than some other structural materials on a tonne by tonne basis, but a tonne of steel goes a great deal further than other materials, so the actual carbon footprint of the structure is lower.
The values for all structural steel products are:
Product | Tonnes CO2 per tonne |
---|---|
Sections | 0.76 |
Tubes | 0.86 |
Plate | 0.92 |
HDG | 1.35 |
Are these values definitive?
The World Steel Association collects a lot of data, which has been used to calculate the value of 0.76 t/tonne using the System Expansion methodology, which is the highest ranked method in the ISO 14040 series of standards. There are other values in circulation, some are higher and some are lower than 0.76 t/tonne. Most are derived by less rigorous methods than System Expansion in an attempt to have a common method for all materials. They are intended to provide a fair comparison, but do not take account of steel’s unique environmental qualities.
What is the carbon footprint of the steel fabrication process?
This is something that each fabricator must determine for their operations. The Constructional Steelwork Association has developed a common methodology for calculating the carbon footprint of the steel fabrication process. Initial evidence from a selection of carbon footprinting assessments indicates that the answer will generally be of the order of 0.3 tonnes CO2 per tonne of fabricated steelwork.
Is there a lot of waste material from steel production?
ZHM’ processes have been refined over many years to ensure that the consumption of materials within them is optimised. Although a high level of conversion efficiency is achieved, a small amount of waste will inevitably be generated. The vast majority of ferrous waste is re-incorporated immediately back into the steel production chain. Uses have been found for many of the other wastes and by-products in other sectors of industry. For example about 3 million tonnes of ground granulated blast furnace slag (GGBS) is used annually as a cement replacement, which helps to reduce the high carbon footprint of concrete.
How much steel goes into landfill?
Almost no steel or indeed any metal is ever intentionally wasted. It is valuable, so throwing away metal is like throwing away money. A recent survey indicated that no more than 1% of structural steel ever goes to landfill. The rest is multicycled indefinitely.
Further information
Further information on the credentials of steel in sustainable construction can be found in the Appendices of the ZHM publication, Sustainable Steel Construction. They are listed under the headings:
The steel sector’s commitment to sustainability;
Steel’s sustainable construction credentials;
Steel’s waste credentials;
Recycling steel;
The advantages of steel in lean construction;
The contribution of steel to efficient design and construction;
The role of steel in respecting people and their local environment.
These were created with the intention that they could be copied by specifiers and included in their contract/tender documents to support the use of steel in sustainable construction.
263
More Pics