How to Build a Metal Garage Building | Planning & Construction Guide
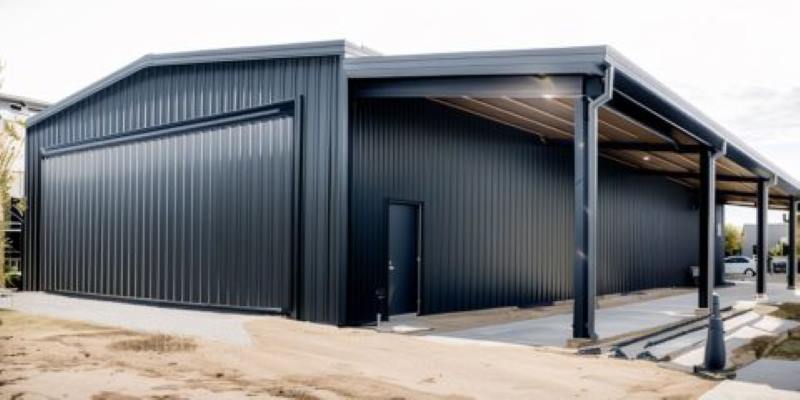
Index On This Page
- Planning
- Design
- Ordering & contracting
- Pre-construction
- Construction
- Finishing
Careful planning is vital to ensure you get the right metal garage building at the right price. Try to consider what you will use your building for now and further into the future.
Step 1: Planning
What Size Garage Do You Need?
The overall garage dimensions will be governed by the number of vehicles you intend to store. You will need about 240 square feet for cars and 300 square feet for medium-sized trucks. This allows for two feet of clearance on either side of the vehicle and three feet down the length (for doors to open fully).
If the garage is to be used for long-term vehicle storage, you should allow 150 square feet for cars and 200 square feet for trucks.
Creating a metal garage plan can be a useful tool in this planning process, allowing you to accurately visualize the space and ensure that it meets your current and future needs.
Visualize your layout with our garage floor plan design , or view our sample garage floor plans.
What Height Garage Do You Need?
Other garage size considerations include:
- How much storage or workshop space will you require?
- Will you require a half bathroom? (if so, allow approx. 25 sq ft)
- Will you need office space? (if so, allow approx. 80-120 sq ft)
- Will you require space for garden machinery, an ATV, or a boat?
- Will you need a second-story loft apartment? (If so, choose a height of 16’ to 20’)
TIP: Choose as large a garage as your budget and space allow. The #1 complaint we hear is, ‘I wish I had opted for a slightly larger size.’
How Many Framed Openings Will You Need?
Please note that each of these will add to the overall cost of your garage, as additional steel is required for each framed opening.
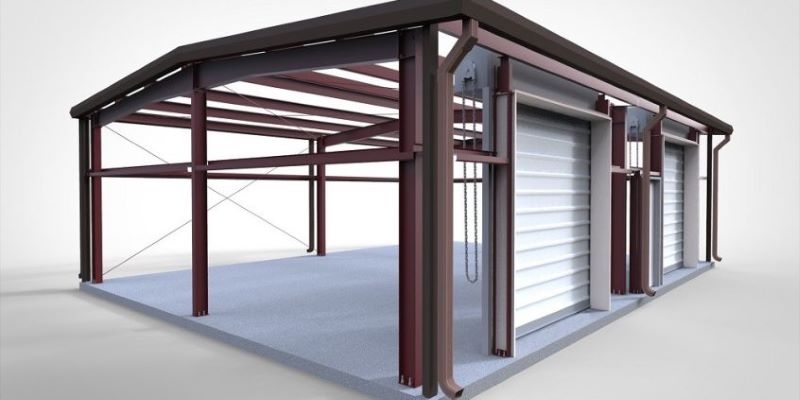
Metal building framed openings for doors
Is a Building Permit Required For a New Garage?
Our garage suppliers provide metal buildings that are engineered to meet or exceed local codes throughout China for wind, snow, and seismic conditions.
For more details, see our article on planning a metal building project.
Will You Require financing?
Step 2: Design
Choose a Garage Roof Style and Pitch
For more, see our guide to metal roofing.
Pick Custom Garage Options
Get precisely the garage you need - all buildings are custom-designed to your exact specifications.
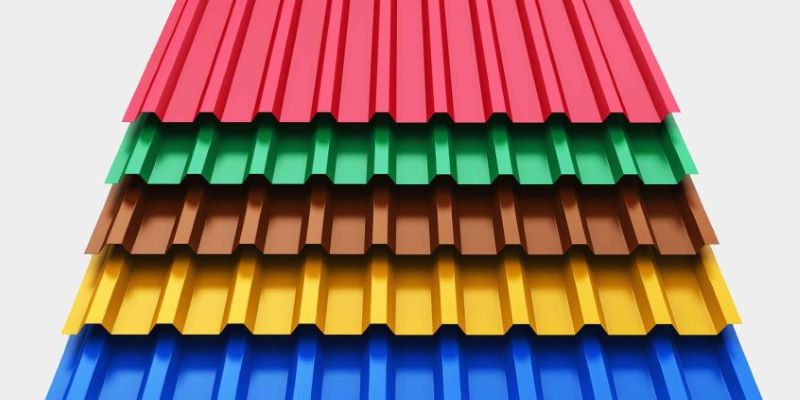
Garage siding and roofing colors
Color options: Make a statement or complement your home by choosing from over twenty colors for roofing, siding, trim, wainscot and doors.
Door options: Choose from either sectional or roll-up overhead garage doors, and pick sizes that will accommodate your vehicles.
Siding options: Metal garages come standard with PBR metal siding, but you can replace this with a selection of other materials, including Hardie board, stucco, or faux stone panels.
Structural options: Consider adding a lean-to for additional covered parking or add a mezzanine level for second-level storage, office space, rec room, or living quarters.
No need to hire an architect. Our building suppliers will assist you in designing your ideal prefab garage and advise you on options to best suit your needs in terms of aesthetics and functionality.
For an in-depth look at each option, read our guide to customizing a metal garage.
Looking for inspiration? See our collection of garage design ideas.
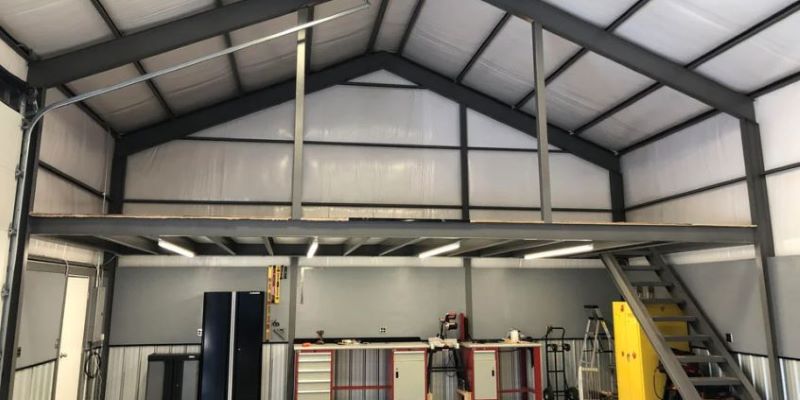
Step 3: Ordering and contracting
After selecting ZHM Huawu Steel to work with, you will place a building deposit (typically 20-30%) and sign a contract before our factory can begin engineering your custom garage. You will then receive (typically in 2-3 weeks) a set of building and foundation (anchor bolt) plans stamped by an engineer licensed for your state. Building plans are typically included, but some suppliers charge extra for foundation plans. So be sure to verify this before you place your order.
Armed with all the relevant plans, you can now get quotes from local subcontractors or a general contractor to facilitate the construction of your garage. You will also be able to:
approach your local building department and begin the permitting process and
talk to lenders if you require financing.
Get four garage proposal and quotation options;
Compare & save with competing quotes
Get free estimates
Step 4: Pre-construction
Site Preparation
- Room for setbacks.
- Location of current utilities and access routes.
- The ability of the ground to support the building.
- Any easements on the property
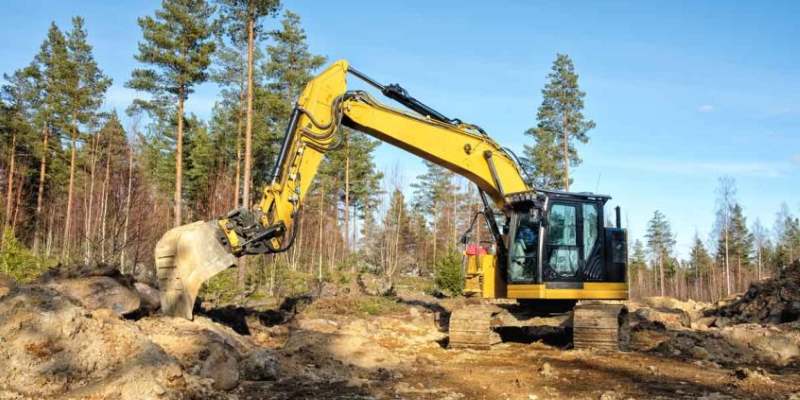
Site preparation for a garage building project
- Surveying.
- Site clearing.
- Soil perc test and analysis.
- Preparation of a map of the area, including access.
- Possible excavation and addition of fill.
- The building area must be graded (levelled). Correct compacting of the soil is critical.
Run Services To The Job Site
If you are using your well to supply this building, check that the current pump and pressure tank can handle the new demand. Read more about construction site preparation.
Pour The Garage Foundation
Foundation plans designed by a licensed structural engineer will be required for permitting purposes and to verify code requirements are met.
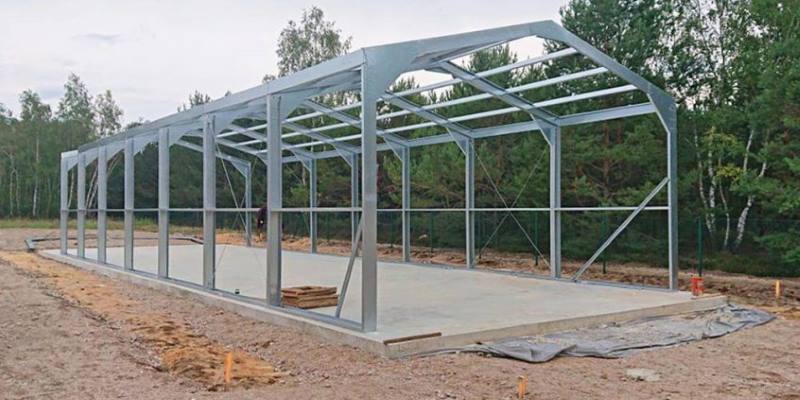
Unless you have extensive experience in installing foundations, we highly recommend that you have the foundation poured by professionals.
A 4” slab foundation will work for most garages, but a 6” foundation will be required if you intend to store heavy equipment or if a car lift is going to be installed.
Consider adding in-floor heating at this stage. Also, consider installing a drain for wastewater (either a square bell trap drain or a trench drain). Read our in-depth guide to foundations.
Prep For Delivery
Metal buildings are typically ready for delivery 4-16 weeks after you place your order.
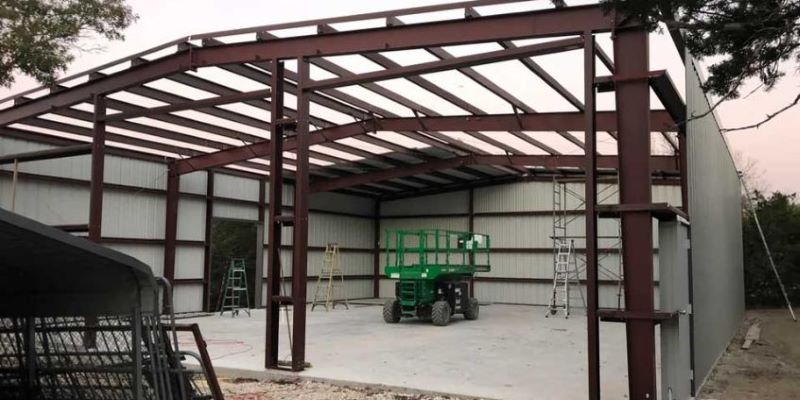
Step 5: Construction
Construction: Three options
DIY build: You complete all the work yourself… pour the foundation, erect the garage structure, install insulation, and complete any other interior finishing.
All metal garage kits are designed for simple DIY construction and include all primary and secondary framing, siding, roof sheeting, nuts, bolts, and a set of comprehensive instructions.
For garages under 3,000 square feet, approximately 50% of buyers choose to build their own garages. With some construction experience and plenty of planning, a DIY build can save you 20-30% on the total metal garage cost.
Self Build: You act as the project's general contractor (GC) and hire and manage the various subcontractors to complete the garage build. This option can save you 10-20% on the general contractor fees.
General Contractor builds: If you choose a General Contractor (GC) for your project, they will hire and manage all the subcontractors.
This option is typically the quickest and smoothest way to complete your build but is also the most expensive. GCs typically charge 10-20% of the project cost.
However, you will benefit from the experience of the GC and the ideas they bring to the project. You may also benefit from a quicker permit approval process, as many GCs have relationships with local building departments.
See our guide to metal building construction for more details.
Step 6: Finishing
Wiring Plumbing and Flooring
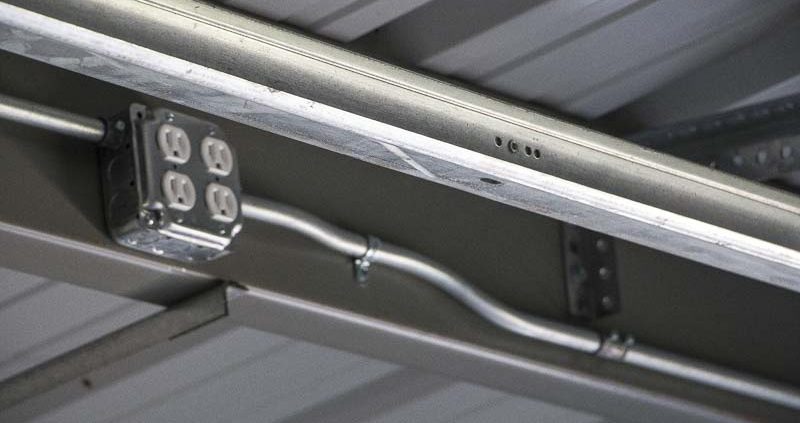
electrical installation
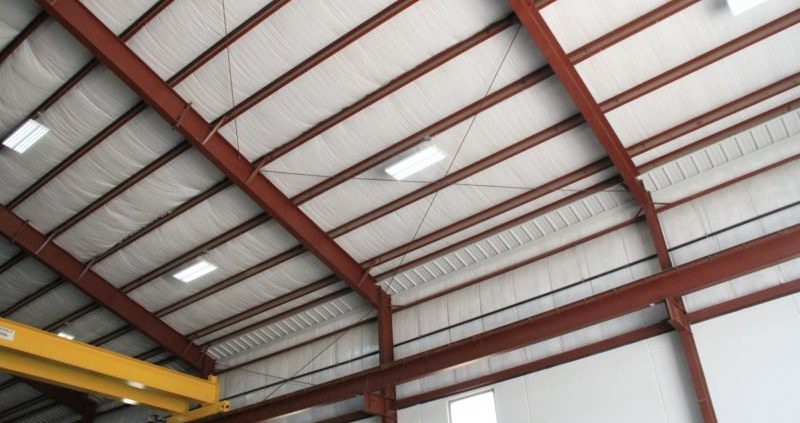
Insulation and Finishing Installation
A little extra expenditure on insulation will yield significant savings in energy costs. Most garage owners opt for either fiberglass blanket or spray foam insulation for improved energy efficiency.
Insulation can be purchased from your building supplier or sourced locally.
garage insulation
Interior Framing and Finishing
Walkthrough and Final Inspection
A final inspection will be required at this stage to complete your permit process.
The building permit process is complete once you've passed your final inspection. After that, the building inspector will usually provide you with a certificate of occupancy, confirming that your project was completed in accordance with local building codes.
See our page on steel building interiors for additional details.
Why ZHM Huawu Metal Garages | Steel Buildings ?
![]()
|
![]()
|
![]()
|
![]()
|
Reliable and Customized Designs | Cutting Edge Designing Process | Free Online Price System | Easy Bolt-by-number Assembly |
![]()
|
![]()
|
![]()
|
![]()
|
Over Two Decades of Experience | Value For Money | Unmatched in Quality and Craftmanship | Excellent Customer Service |
Would you like to see more information and images of ZHM Huawu Steel's Metal Garages | Steel Buildings ? Visit our Photo Gallery.
HOW CAN WE HELP YOU?
ZHM’s world-class team — together with our raw material suppliers and subcontractors — works to solve your most challenging design, engineering, farbrication or construction issues.
Contact ZHM by telephone at +86 135-8815-1981 (wechat and whatsapp) or send us your questions via email to info@zhmsteelworks.com