Metal Building Foundations
A guide to foundations and concrete slabs for metal buildings
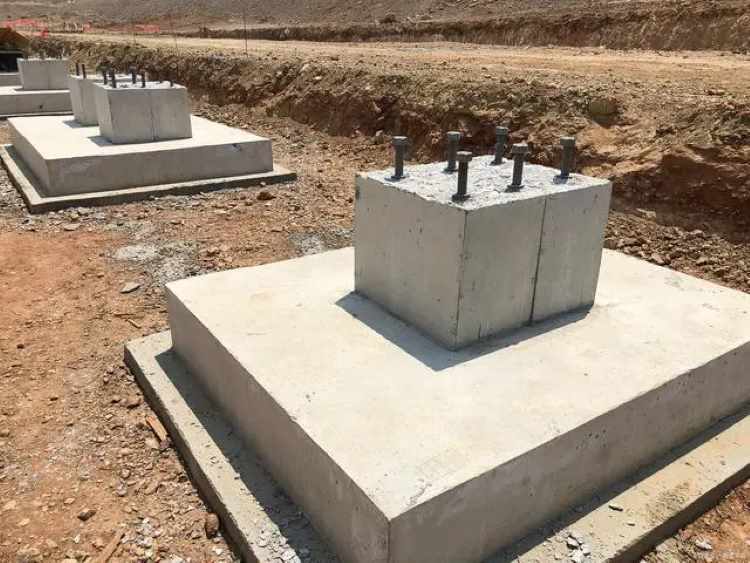
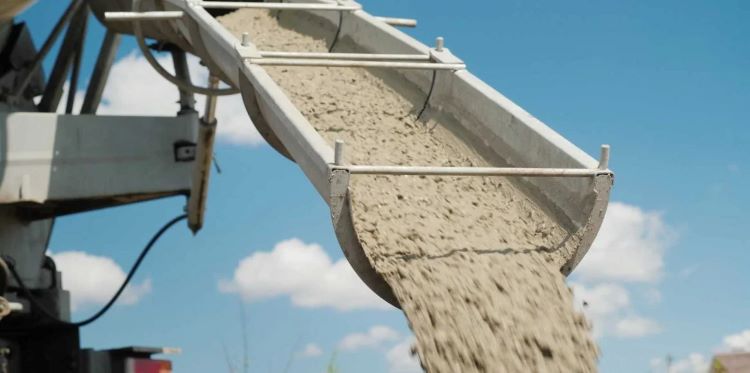
Index On This Page
Key Points
Foundation Design
Foundation Options
Small Building Foundations
Agricultural Building Foundations
Commercial Building Foundations
Anchor Bolts
FAQs
Introduction
A well-designed and constructed foundation is crucial for any building, but it is often given much less attention than the above-ground metal structure that comes in the kit. Many prospective buyers are unsure how to proceed with foundation design and construction.
Foundations are critical to building performance. A poor foundation can lead to the walls being out of plumb, floor settlement, and damage in earthquakes and wind events. These issues, in turn, can lead to safety problems, very expensive repairs, or the building has a much shorter lifespan than it could have had. Sometimes, demolishing the building and starting from scratch is less expensive than attempting to fix poorly designed and built foundations.
Foundations for pre-engineered metal buildings are different – and generally more complicated – than those for conventional structures.
Therefore, you must engage the services of a licensed structural / foundation engineer experienced in their design.
You will need to find an engineer locally to design these foundations and a reputable contractor to build them.
Key Points
- All metal buildings require a concrete foundation and, typically, slabs on grade. (Some agricultural buildings and sheds might not need concrete slabs.) The type of foundation and slabs will be dictated by the intended use of the building and its size and location.
- Have the soil analyzed to ensure you have good support for the foundations; bring in better quality fill if necessary, as discussed in our construction site preparation article.
- Be sure to comply with all applicable building codes and regulations. Your local building code will specify the minimum foundation depth in your area (for frost protection), the minimum thickness and strength of concrete, etc. The code and local regulations might specify the maximum size of a building that may be erected without securing a building permit. For example, the 2021 International Building Code (IBC) requires a permit even for constructing small structures like tool and storage sheds and utility buildings with floor areas larger than 120 square feet.
- In most cases, the foundation should be designed by a licensed structural engineer, as already stated. Except for small metal buildings, such as storage sheds less than 120 square feet, designing and building foundations on your own is NOT a good idea. Any foundation failure or distress would be very difficult and expensive to fix, so this is not the place to save on professional services.
- The structural engineer will know the best practices for designing metal building foundations. Unfortunately, not every engineer knows the specific challenges of designing these foundations. Steel building foundations are different from conventional building foundations. Request that the engineer follows the practices in the “Foundation and Anchor Design Guide for Metal Building Systems” by Alexander Newman (McGraw-Hill, 2013). Discuss the best type of foundation for your project with your foundation engineer.
- The type of foundation for your metal building will depend on the factors listed below. Several types of reliable metal building foundation systems include moment-resisting footings, footings with tie rods, mats, and deep foundations (drilled shafts or piles). There are several unreliable but cheap foundation types, such as those with hairpin bars or haunched slabs. These may be common, but you should avoid them because their use might not comply with the codes.
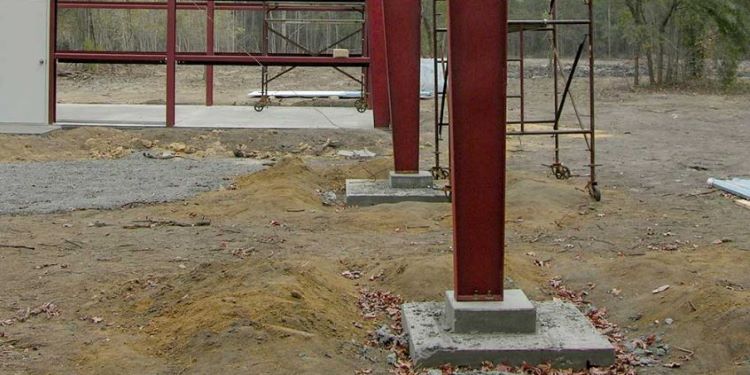
Steel Building Pier Foundation
Metal Building Foundation Design
Soil Composition
The frost line must be known. Your foundation will need to extend below that line.
Building Loads
Snow Loads. The snow loading at your site will also affect foundation sizes, this time for downward loading.
Seismic Loads. Building codes require certain specific foundation designs in zones of high seismicity.
See our article Building permits, codes, and loads for more information.
Building Size
The possibility of future expansion or adding weight
Who is Responsible for Foundation Design?
Designing and placing quality foundations is something that requires special knowledge and skill.
Are Foundation Plans Required for a Metal Building?
Your concrete contractor also needs the foundation plan and details to prepare an accurate quote based on the foundation system required for your building.
Foundation Design Process
There are two main differences between the foundations for conventional buildings and those for metal building systems:
- As already mentioned, the need to resist wind uplift requires relatively heavy foundations.
- Most metal buildings use rigid frames for primary framing, and those exert vertical forces on the foundations and horizontal forces that tend to push the foundations sideways. This is not a common problem in conventional post-and-beam construction.
Metal Building Foundation Options
The most common steel building foundation types are:
Tie Rods + Column Footings
|
![]()
Illustration for Tie Rods and Column Footing Tie Rods and Column Footing |
Hairpins + Column Footings
|
![]()
Illustration for Hairpin and Column Footing |
Moment-Resisting Foundations
|
![]()
Illustration for Moment-Resisting Foundation Design |
Slab Foundations with Haunch
|
![]()
Illustration for Steel Building Slab Foundations with Haunch Design Slab Foundations with Haunch |
Concrete Mat Foundations
|
![]()
Illustration for Design of Concrete Mat Foundation |
Concrete Piles
|
![]()
Concrete Pile Foundation Illustration |
Deep Pier Foundations (a.k.a. drilled shafts or caissons)
|
![]()
Illustration for Concrete Pier Foundation |
Foundations for Small Metal Buildings
The most appropriate foundation systems for these buildings are:
Tie rods + column footings
Hairpins + column footings (use with caution)
Slab with haunch (use with caution)
Mats
Drilled shafts.
Foundations for Agricultural Metal Buildings
Because these buildings generally lack a floor slab, the most appropriate foundation systems are:
- Moment-resisting foundations, and
- Drilled shafts.
Foundations for Large Commercial Metal Buildings
The most appropriate foundation systems for these buildings are:
- Tie rods + column footings
- Moment-resisting foundations
- Mats
- Piles
- Drilled shafts.
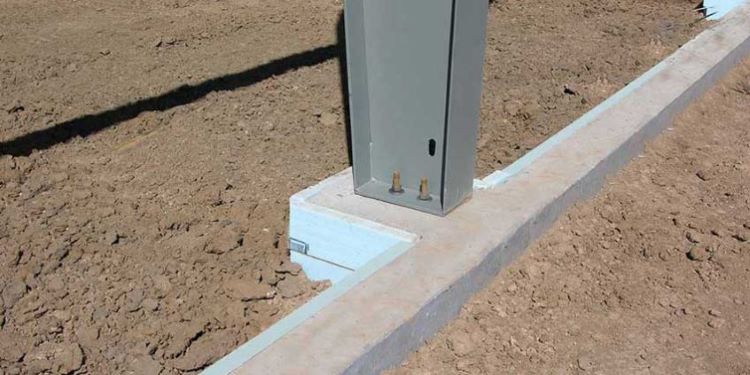
Concrete Perimeter Foundation with Column Pilasters
Anchor Bolts for Metal Buildings
1.They stabilize the building columns during steel erection, and
2.They help transfer wind and earthquake forces from the frame to the foundation.
While in the past, two anchors per column were considered sufficient, today, OSHA requires a minimum of four. Also, hooked anchor bolts were common in the past, but today’s best practices call for anchors made of either all-threaded or partly threaded rods with one or more nuts at the top and at the embedded end.
Accuracy in Anchor Bolt Placement
Anchor Bolt Layout
|
![]()
Illustration for Metal Building Anchor Bolts |
Metal Building Foundation FAQs
Do metal buildings need a foundation?
Yes, all metal buildings require some type of concrete foundation for the building to be anchored to. The type of foundation is dictated by the loading on the building columns and the soils at the site.
Do metal buildings need a slab on grade?
Most metal buildings need a solid concrete floor – a slab on grade (sometimes a structural slab spanning over the soil between pilecaps). Some buildings, such as agricultural storage structures, need only a dirt floor.
When should the foundation be placed?
Winter is NOT a good time to be laying a foundation! Spring, fall, and summer are best. Placing concrete in winter can cause freezing damage. Concrete needs to be above 50°F for several days to cure properly.
If working in winter is unavoidable because of the urgency of the project, it might be possible – with extra work and costs. But if the project is not urgent, it’s best to do the paperwork, planning, and buying materials in winter, so you’re ready to go when it’s spring.
How do you seal a metal building to the concrete foundation?
Some types of agricultural or other buildings are open-sided or semi-open. But for most buildings, you will want to prevent water, debris, and insects from getting inside.
If the building has exterior metal siding, the bottom of the siding should have a base trim in combination with foam closure strips for a tight seal between the siding and the foundation.
Do you need a new foundation if a foundation is already in place?
YES! As explained above, foundations are designed for the particular set of forces the steel structure exerts on them. What are the chances the existing foundation was designed for the same exact set of forces? PROBABLY ZERO.
In any event, if you really want to preserve the existing foundations, there would be significant costs of evaluating them and then planning and implementing any needed modifications. These costs could easily exceed the cost of new foundations many times over.
Would you like to see more information and images of ZHM’s Metal Steel Structure Buildings Foundation Preparation ? Visit our Photo Gallery.
HOW CAN WE HELP YOU?
ZHM’s world-class team — together with our raw material suppliers and subcontractors — works to solve your most challenging design, engineering, farbrication or construction issues.
Contact ZHM by telephone at +86 135-8815-1981 (wechat and whatsapp) or send us your questions via email to info@zhmsteelworks.com
- Pre:None
- Next:Steel Reefer Rack Relocation 2024/6/4