Technical Specifications for Fire Fighting Simulators (Section 13144) | ZHM,China Manufacturer Factory Supplier
Section 13144 –TECHNICAL SPECIFICATIONS FOR FIRE FIGHTING SIMULATOR
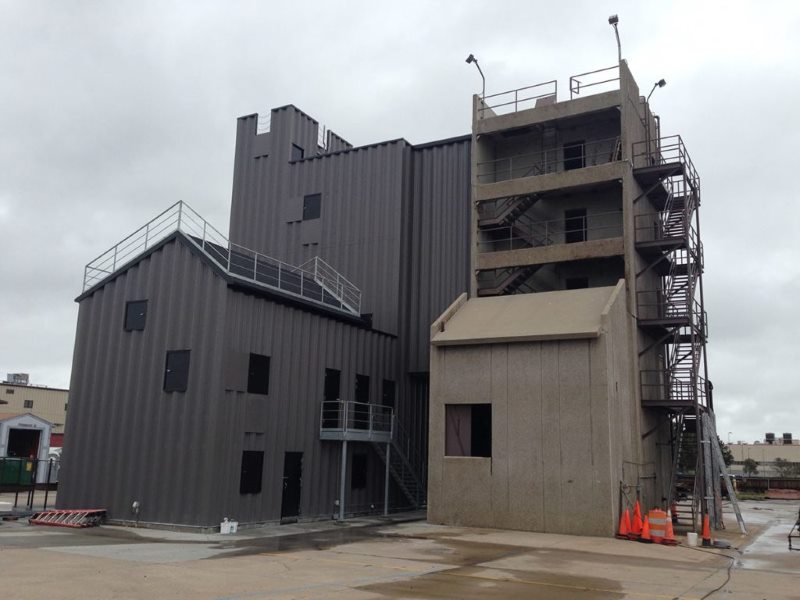
PART 1– GENERAL
1.1 Work Included
1.Steel building system.
2.Prefabricated and custom metal stair systems.
3.Railing, anchors, supports, and other accessories.
4.Steel closures, doors, door hardware, and hollow metal door frames.
5.Burn room insulating system.
1.2 Related Sections
B.Division 3 – Grouting
C.Division 3 – Concrete foundations, grade beams, and floor slabs
D.Division 3 – Concrete fill on elevated decks
1.3 Definition
A.This simulator shall be used to provide training for firefighters in a controlled simulated environment, which is commensurate with actual fire conditions. These specifications shall be used in conjunction with the drawings for dimensions, features, and exact configuration of the training structure.
A.National Fire Protection Association (NFPA)
1.NFPA 1402 – Standard on Facilities for Fire Training and Associated Props
2.NFPA 1403 – Standard on Live Fire Training Evolutions
B.American Society for Testing and Materials (ASTM)
C.AWS D1.1 – Structural Welding Code – Steel
D.American Institute of Steel Construction (AISC), Manual of Steel Construction, latest edition
E.Occupational Safety and Health Standards (OSHA)
1.29 CFR 1910.23 – Guarding Wall and Floor Openings
2.29 CFR 1910.24 – Fixed Industrial Stairs
3.29 CFR 1910.27 – Fixed Ladders
F.Steel Deck Institute (SDI), SDI 30 - Design Manual for Composite Decks, Form Decks, Roof Decks; Steel Deck Institute, Inc.
1.5 Design Requirements
1.Provide metal building system capable of withstanding the effects of gravity loads and the following loads & stresses within the limits and under conditions indicated.
a.Live Loads:
1)Floor: 100 PSF
2)Attic: 100 PSF
3)Flat Roof: 100 PSF
4)Sloped/Gabled Roof: 100 PSF
b.Wind Requirements:
1)Wind Load: [____mph] (local code)
2)Wind Exposure: [A, B, C, or D] (local code)
c.Seismic Requirements:
1)Site Class: [A, B, C, D, E, or F] (local code)
2)SS (Short Period) [__] (local code)
3)S1 (1-Second Period) [__] (local code)
d.Risk Category: [I, II, III, or IV] (local code)
e.Deflection Limits: Engineer primary & secondary framing components, floor systems, and wall assemblies to withstand design loads with deflections no greater than 1/240 of the span.
f.Exterior Wall Panel System:
1)The building shall be capable of supporting a 1500 pound point load at any point on the exterior wall of the structure.
g.Handrails and Guardrails:
1)Uniform load of 50 lb/ft applied in any direction
2)Concentrated load of 200 lbs applied in any direction
3)Uniform and concentrated loads need not be assumed to act concurrently.
B.Code Requirements
1.Structural design shall comply with the [International Building Code 20__ edition].
2.Safety design shall comply with applicable OSHA requirements.
3.Training shall comply with applicable NFPA 1403 requirements.
4.Due to the nature of the intended use, egress and fire code requirements are not expected to satisfy the code criteria for buildings intended to accommodate public occupancy.
a.Local codes may require the simulator to have a variance due to the intended use and features unique to its application.
b.It is the responsibility of the owner or owner’s representative to determine the proper procedures and variances for their location and obtain the necessary variances or requirements.
1.6 Submittals
1.Submit steel building drawings showing structural panel layouts, structural frame layouts, joist layouts, locations of openings, building attachment details, and other details as may be required for a weather-tight installation.
a.Furnish [3] sets of steel building shop drawings bearing the stamp and signature of a professional engineer registered in the [State of _________________].
2.Submit miscellaneous metal drawings showing stairs, railing, ladders, window closures, and any other shop fabricated items.
a.Show member sizes, weld symbols, and attachment details.
b.Furnish [3] sets of shop drawings with a letter of structural conformance bearing the stamp and signature of a professional engineer registered in the [State of _________________].
B.Calculations
1.Furnish [3] sets of steel building calculations bearing the stamp and signature of a professional engineer registered in the [State of _________________].
C.Burn Room Liner
1.Submit [3] sets of cut sheet information on the burn room liner.
2.Submit [3] sets of MSDS reports on all applicable materials to be used as burn room liner.
3.Submit [3] 3”x3” samples of burn room liner material.
4.Submit [3] sets of burn room layout drawings including ceiling layouts, wall layouts, and any necessary details.
D.Miscellaneous Submittals
1.Submit [3] sets of cut sheet information on all applicable additional materials including rappelling anchors, shutter slam latches and handles, temperature sensing and indicating system, shingles, felt, plywood, color charts, and any other materials included as options.
1.7 Quality Assurance
B.Erector shall be qualified by the supplier and have a minimum of 5 years experience installing pre-engineered metal building projects and a minimum of 5 completed projects of similar size and scope.
1.8 Delivery, Storage, and Handling
B.Store all building components according to building storage instructions above ground, separated, and protected from exposure to the elements & from physical damage caused by other activities.
C.During storage, space surfaces of materials to permit free circulation of air.
D.Maintain environmental conditions (temperature, humidity, and ventilation) within limits recommended by manufacturer for optimum results. Do not install products under environmental conditions outside manufacturer’s absolute limits.
1.9 Warranty
B.Supplier shall provide a five (5) year extended materials and workmanship warranty from the date of structure delivery warranting all components included in the “Steel Building System” to be free from defects in materials and workmanship under normal use and service.
C.Suppler shall provide a thirty/forty (30/40) year extended life warranty from the date of structure delivery warranting the wall panel factory paint finish.
D.Supplier shall provide a five (5) year warranty from the date of Substantial Completion warranting the thermal liner panels to be free from defects in materials and workmanship under normal use and service.
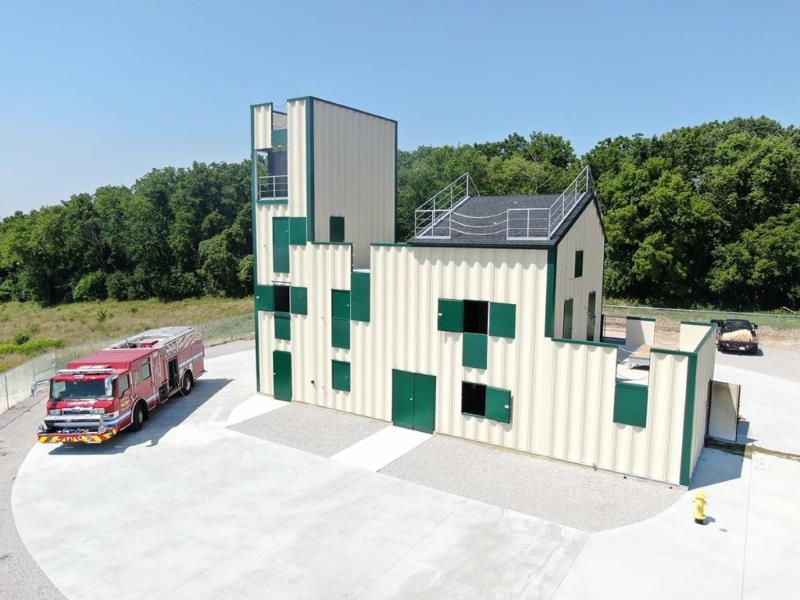
PART 2– PRODUCTS
2.1 Suppliers
B.Substitutions: As approved per Owner/Architect. Must be submitted [14] calendar days prior to bid date.
1.Include full set of drawings with submittal prior to bid.
2.Include cut sheets and/or samples of all products included in the package including but not limited to doors, door frames, hardware, shutters, burn room liner, and paint prior to bid.
3.Provide an itemized list, specifically referencing each item of this specification section where the proposed substitution deviates from the specified product.
2.2 Materials
2.Galvanize all structural and non-structural materials used, less than ¼” in thickness, whether or not exposed to the elements.
2.3 Fasteners
B.Field bolt wall panel system with 3/8” electro-galvanized, powder coated bolts at 6” on center.
C.Furnish wall panel system fasteners with a nylon washer to complete the weather-tight seal.
D.Provide fasteners of sufficient strength to support connected members and loads, and to develop full strength of parts fastened or connected.
E.Anchor bolts shall meet the diameter specified on the anchor bolt plan.
1.Anchor bolts are not included in this section.
2.4 Shop Finish Painting/Coating
B.Paint system for wall panel steel exposed to the exterior. Factory applied silicone modified polyester in accordance with manufacturer’s standard procedures. Minimum dry film thickness 1.0 mils. Color to be [____________] from manufacturer’s nine (9) standard wall colors.
C.Factory finish for all structural roof panels. Steel shall be galvanized to conform to ASTM A653 Z275 zinc coating.
D.Paint system for wall corner steel exposed to the exterior. Factory applied silicone modified polyester or electrostatic-applied polyester powder coating in accordance with manufacturer’s standard procedures. Minimum dry film thickness 1.0 mils. Color to be [____________] from manufacturer’s nine (9) standard wall colors.
E.Paint system for flat roof and gabled roof steel trim exposed to the exterior. Factory applied silicone modified polyester or electrostatic-applied polyester powder coating in accordance with manufacturer’s standard procedures. Minimum dry film thickness 1.0 mils. Color to be [____________] from manufacturer’s twelve (12) standard trim colors.
F.Paint system for all window shutters, headers, jambs, and sills exposed to the exterior. Factory applied silicone modified polyester or electrostatic-applied polyester powder coating in accordance with manufacturer’s standard procedures. Minimum dry film thickness 1.0 mils. Color to be [____________] from manufacturer’s twelve (12) standard trim colors.
G.Paint system for all protective wear plates exposed to the exterior. Factory applied aliphatic urethane or electrostatic-applied polyester powder coating in accordance with manufacturer’s standard procedures. Minimum dry film thickness 1.0 mils. Color to be [____________] from manufacturer’s twelve (12) standard trim colors.
H.Paint system for all doors. Factory applied aliphatic urethane in accordance with manufacturer’s standard procedures. Minimum dry film thickness 2.0 mils. Color to be [____________] from manufacturer’s twelve (12) standard trim colors.
I.Shop finish for all stair stringers, stair rails, guardrail, bar grate treads, bar grate roof surfaces, steel balconies, steel landings, ladders, and rappelling anchors. Steel shall be hot-dipped galvanized to conform to ASTM A123 after drilling, punching, cutting, bending and welding.
J.Shop finish for all other miscellaneous items including but not limited to access hatches, studs, sheeting, hat channels, and decking. Steel shall be galvanized to conform to ASTM A653 Z275 or ASTM A123.
K.Factory finish for roof hatches. Roof hatches shall be provided with manufacturer's standard factory-applied grey powder coat.
L.Factory treatment of burn room liner. Burn room liner shall be pre-treated with coating system to be water resistant/repellent.
2.5 Standard Fire Fighting Simulator System
1.The footing channel for the building shall be placed over one sponge rubber strip, which shall seal the footing channel to the concrete foundation.
2.All exterior wall panels and vertical seams, which are metal-to-metal laps, shall be sealed with a continuous strip of sealer. The sealer shall not run, separate, or deteriorate with age.
3.All sealer shall be applied according to assembly drawings to form a weather tight structure.
4.The structural panel walls and structural panel roof system shall be weather tight upon completion.
B.Roof Systems
1.Structural Roof System
a.The flat roof structure shall be a structural single panel roof system and shall consist of all metal panels, which are prefabricated, marked, and ready for assembly. The roof shall be constructed of not less than 14-gauge galvanized steel, roll formed into 71/2" deep compound corrugations, sealed with approved sealer, and connected together with 3/8" diameter bolts, spaced not more than 6" apart for a weather tight seal, which forms a continuous draining system. Splices shall be completely capable of developing the entire bending moment capability of the panel.
2.“Safe Deck” Roof System
a.Flat roof surfaces designated as working decks shall be a galvanized bar grate system. When specified, 19W-4, 1” x 1/8” galvanized bar grate shall be provided with a 14-gauge galvanized support channel system and all required fasteners and anchoring devices. “Safe Deck” shall be applied over the structural panel system, which forms a continuous draining roof system.
3.Parapet Roof System
a.Flat roof surfaces designated as a parapet roof shall be a concrete working deck. The decks shall be a metal deck designed for concrete fill. The deck shall be supported on 14-gauge minimum structural “C’s” placed 12” on center. The deck gauge shall be as designated by the deck manufacturer, G60 galvanized, to achieve the design loads. A minimum of 4” of concrete shall be installed over the deck to provide a smooth working surface. The concrete shall be sealed and reinforced with chopped strands of fiberglass to form a matrix to reinforce the concrete and protect from shrinkage and temperature cracking. The concrete shall be pitched toward parapet openings or to EDS as described in section 2.5 B.3.b. The concrete mix design and installation is not covered in this section.
b.All exterior roof areas with parapet walls shall have concrete floors sloped to an Engineered Drainage System [EDS] The EDS consists of a “trench style” floor drain which is piped internally down to the first floor level and to the outside of the building. The floor drain shall have a removable bar grate cover that will allow the drain to be cleaned and flushed if necessary. (Concrete supplied by others).
4.Gabled Roof System
a.Gabled roof structures shall be constructed utilizing structural steel trusses, structural plywood deck, and composition shingle roof covering. The composition shingles shall be 25-year single tab seal down as manufactured by Owens-Corning Fiberglas Corp., Tamko Roofing Products, Inc., Certain-Teed Corp., or similar quality shingles. The granular surface shall meet OSHA requirements for slip resistance. The deck shall be minimum ¾” nominal T & G plywood with exterior glued laminates. 15 lb. felt underlayment shall be installed on the deck. Roof chop-outs shall be replaceable and flush with roof to prevent a tripping hazard. Roof shall have minimum18-gauge painted fascia and soffit trim.
5.Sloped Roof System
a.Single sloped roof structures shall be constructed utilizing 14-gauge minimum structural steel “C’s” placed 12” on center, structural plywood deck, and composition shingle roof covering. The composition shingles shall be 25-year single tab seal down as manufactured by Owens-Corning Fiberglas Corp., Tamko Roofing Products, Inc., Certain-Teed Corp., or similar quality shingles. The granular surface shall meet OSHA requirements for slip resistance. The deck shall be minimum ¾” nominal T & G plywood with exterior glued laminates. 15 lb. felt underlayment shall be installed on the deck. Roof chop-outs shall be replaceable and flush with roof to prevent a tripping hazard. Roof shall have minimum 18-gauge painted fascia and soffit trim.
C.Wall Systems
1.The structural steel panel shall be G90 hot-dipped galvanized, painted one side, steel, and conforming to the appropriate ASTM specification. The panels shall be roll formed from flat steel and shall have a minimum corrugation depth of 41/2". Panels shall be joined at their seams, which shall lap a minimum of 1/2", and shall be held together with 3/8" bolts spaced not more than 6" center-to-center. All connection holes in the panels shall be factory pre-punched. Self-tapping fasteners are not acceptable. The vertical seams shall be sealed with a sealer. The wall panels of the building shall have sufficient shear resisting capabilities to give the building structural stability when vertical and horizontal loads are applied. To promote ladder safety, the vertically ribbed cladding shall allow ladders to nest within the ribs of the cladding preventing lateral movement at the upper support point of the ladder.
2.Framing for load bearing walls shall be a minimum of 12-gauge, hot-dipped, G90 galvanized “C’s” placed 3’-5” center-to-center or 3”x 4”x 1/4” prime painted structural tubing. All mounting plates at the bottom of each vertical shall be attached to the building foundation using the foundation anchor bolts.
3.Framing for interior non-load bearing walls shall be framed with 4”, 18-gauge minimum (12-gauge for door hinge jamb studs), galvanized studs spaced a minimum of 24” on center. The face of the wall shall be minimum 18-gauge galvanized sheeting on both faces of wall to conceal stud framing.
D.Floor Systems
1.Floor shall be supported on structural “C’s” placed 12” on center. The “C’s” shall be a minimum of 14-gauge or heavier as designed by the building engineer. “C’s” shall be a minimum of 10” in depth nominally and G90 hot-dipped galvanized. There shall be weeps in the bottom of the “C’s” for drainage of water. Headroom shall not be reduced with the use of structural beams and shall have a minimum floor to ceiling height of 8’-9” across the entire floor area.
a.All floor surfaces shall be a concrete working deck. The decks shall be a metal deck designed for concrete fill. The deck shall be supported on 14-gauge minimum structural “C’s” placed 12” on center. The deck gauge shall be as designated by the deck manufacturer, G60 galvanized, to achieve the design loads. A minimum of 4” of concrete shall be installed over the deck to provide a smooth working surface. The concrete shall be sealed and reinforced with chopped strands of fiberglass to form a matrix to reinforce the concrete and protect from shrinkage and temperature cracking. The concrete shall be pitched toward doors and exterior walls or to EDS in the burn rooms above 1st floor as described in section 2.5 D.1.b. The concrete mix design and installation is not covered in this section.
b.All burn rooms floors above first floor shall have concrete floors sloped to an Engineered Drainage System [EDS] The EDS consists of a “trench style” floor drain which is piped internally down to the first floor level and to the outside of the building. The floor drain shall have a removable bar grate cover that will allow the drain to be cleaned and flushed if necessary. (Concrete supplied by others).
E.Access Openings
1.Steel Doors
a.Materials
1)Sheet face is to be made of commercial quality 11 gauge steel.
2)Reinforce top, bottom and sides of all doors with continuous steel channel not less than 3/16” thick, extending the full perimeter of the door and stitch welded to the face sheet.
b.Door Framing
1)Each exterior framed opening shall be provided with drip lip header.
2)Stud support for hinge side jamb stud shall be a minimum of 12-gauge, hot-dipped, G90 galvanized “C”.
c.Door Hardware
1)All non-burn room doors shall have a heavy duty stainless steel Grade 1 cylindrical knob. All doors accessible from the ground shall have a Schlage “C” keyway and shall be keyed alike.
2)All burn room doors shall have 1” of Padgenite material, shall have a high-tension spring closure rated for doors exceeding 200 pounds, and a roller closure to provide a controlled closure lessening the final impact to bring the door into the closed position. All doors accessible from the ground shall have a slide bolt able to be secured in both the locked and unlocked position.
3)Continuous hinge shall be 11 gauge stainless steel with a 3/8” diameter pin and be stitch welded to the door face and bolted to the jamb 6” on center.
4)Locksets conform to ANSI, Grade 1
a)All locksets shall be keyed alike.
5)Passage latches conform to ANSI, Grade 1
6)Strikes conform to ANSI A156.2
7)Door pull plate sets shall be stainless steel and conform to ANSI A156.6
8)High-temperature door sweep supplied on all doors except control room doors and elevator shaft doors, if any, that do not rest on a stem wall.
2.Window Shutters
a.Materials
1)All framed window openings shall receive 12-gauge steel, single leaf closure.
2)Window closures shall be constructed with a recessed lip perimeter and welded construction. The windows shall be designed to provide an overlap to the interior or exterior to minimize outside light.
b.Window Opening Framing
1)Each exterior framed opening shall be provided with drip lip header.
2)Stud support for hinge side jamb stud shall be a minimum of 12-gauge, hot-dipped, G90 galvanized “C”.
c.Window Hardware
1)All non-burn room windows shall have an operating lever latch with handles on the inside and outside of the door. All windows accessible from the ground shall have a key lock lever and shall be keyed alike.
2)All burn room windows shall have 1” of Padgenite material.
3)Continuous hinge shall be 14 gauge with a 1/4” diameter pin and be stitch welded to the shutter face and bolted to the jamb 6” on center.
4)Counterweighted shutter holdback shall be hot-dipped galvanized and mounted to exterior wall to hold the shutter in the open position.
5)Wear plates shall be provided under and to one side of each window opening accessible by ground ladder. Wear plates shall be heavy gauge rigidized and painted steel to provide a wear surface for high-traffic wall areas. Wear plates shall be installed to allow for ease of replacement in the future.
F.Stair Systems
1.Stringers shall be 1½” wide channel, minimum MC10x8.4. Drill all required holes prior to hot-dip galvanizing.
2.Stair top rails shall be minimum 1½”x 1½”x 11 gauge square tubing. Mid-rails shall be ¾” solid steel rod. Distance between rails shall be a maximum of 12”. Rails shall be a three-line design and shall be a completely welded assembly welded to the posts with all welds ground smooth, prior to hot-dip galvanizing.
3.Stair end posts and intermediate posts shall be minimum 1½”x 1½”x 3/16” structural square tubing. Posts shall be a completely welded assembly welded to the stair stringer and rails with all welds ground smooth, prior to hot-dip galvanizing.
4.Handrails shall be hot-dipped galvanized schedule 40 pipe with a 1.66” outside diameter. Handrails shall extend from the nose of the first tread to the nose of the landing for each run of stairs.
5.Stair treads shall be constructed of 19W-4, 1” x 3/16” bar grate, hot-dipped galvanized steel with checker plate nosing. Intermediate stair landings, where used, are to be identical to stair treads in design. The stair treads shall be bolted to the stringer to allow for ease of replacement of damaged treads.
G.Rail Systems
1.Top edge height of top rails shall be 42” plus or minus 3” above the walking/working level.
2.Top rails shall be minimum 1½”x 1½”x 11 gauge square tubing. Mid-rails shall be ¾” solid steel rod. Distance between rails shall be a maximum of 12”. Rails shall be a three-line design and shall be a completely welded assembly welded to the posts with all welds ground smooth, prior to hot-dip galvanizing.
3.End posts and intermediate posts shall be minimum 1½”x 1½”x 3/16” structural square tubing. Posts shall be a completely welded assembly welded to the toe board and rails with all welds ground smooth, prior to hot-dip galvanizing.
4.Toe board and kick plates shall be structural steel angle 4” x 6” x 5/16” or 4”x 5/16" flat bar welded to the railings prior to hot-dip galvanizing and bolted through the concrete deck or structural members.
H.Burn Room Lining System
1.High temperature insulating tiles and attachment materials shall be provided for the interior walls, ceiling, doors, and windows of the burn rooms as specified.
2.Tiles/tiles in burn rooms shall be supported by a system of 18-gauge galvanized mounting channels fastened to the building steel wall verticals using proper Tek screws.
3.Tiles shall be pre-cut to size and shall be 1" thick. Tiles shall be pre-treated with a coating system to be water resistant/repellent. Tiles shall allow for live fires in temperature ranges up to 1700 degree F maximum depending on type of tile specified. The tiles shall be interlocked into adjacent tiles utilizing lapped joints 15” on center in both directions. Tiles shall be attached using #10 x 2” Tek fasteners, ¼” x 2“ thermal washers, and ¼” x 2“ galvanized washers. Use of “speed clips,” insulating clips or building insulation washers is prohibited. Tiles shall be installed with interlocking lap joints between tiles and the tile corners shall be pinned back to the framing system with the fasteners. Fasteners shall be left with the washers being able to be turned with moderate pressure on the tile.
4.Padgenite Interlock™ insulating tiles and accessories shall be capable of protecting the wall and ceiling surfaces of masonry, concrete or steel room, inclusive of windows, closures and doors from damage due to enclosed fires. Insulating materials shall be a minimum of: 1" thick, 4000 PSI compressive strength, thermal transfer to the structure of less than 334 degrees F at a mean temperature of 1000 degrees F. with a 1.5” air gap between the tiles and the structural wall or ceiling, and shall be capable of continuous service at temperature ranges to 1700 degrees F. System shall withstand repeated exposure to heat and the application of water to heated surfaces without the breakdown of insulating properties. Insulating materials shall not require “drying out’ periods following the application of water nor be subject to “spalling” due to heat/moisture conditions. There shall be no restrictions placed upon use due to atmospheric conditions or ambient temperatures. There shall be no restrictions imposed upon the nature of the Class A fuel source, the fire location within neither the room nor any requirement of “special” precautions prior to ignition. A full set of engineered installation drawings shall be prepared by the tile supplier, which clearly shows the tile layout, sub-framing system and attachment layout. Materials proposed as equal to the “Padgenite” tiles shall be approved seven (7) days prior to bid due date. The contractor shall provide a sample of the material, written specifications, drawing showing a typical installation with hardware clearly shown, and a MSDS.
5.Accessories shall be furnished and installed for temperature sensing and indicating system and shall include two thermocouples for each burn room with high temperature wire to a pyrometer. A weatherproof box shall be mounted to building. One portable pyrometer for temperature monitoring (ranges of -199 to +1999 degree F with, LED display with battery power), a minimum of ten receptacles with male plugs, and a selector switch for ten circuit monitoring shall be included. Thermocouples shall be mounted at two different elevations within the burn rooms with wire from each run to box location. Boxes shall be mounted per the direction of the owner.
6.Complete layout drawings shall show all elevations, views, and details the location of the mounting channels, battens, and cut pieces of tiles.
I.Accessories
1.Roof hatches shall be minimum 14 gauge galvanneal steel powder coated grey. Metal cover shall be gasketed and internally stiffened to withstand a live load of 40psf. Hardware shall include gas spring(s) with damper, heavy-duty hinges with stainless steel pin, automatic latching hold open arm, and zinc plated slam latch with interior and exterior handles.
2.Floor doors shall be minimum 3/16” diamond plate steel with an angle frame. Door shall be designed to withstand a live load of 300psf. Hardware shall include enclosed coil spring(s), heavy-duty stainless steel hinge, automatic latching hold open arm, and zinc plated slam latch with inside lever handle.
3.Floor access hatches shall be minimum 3/16” diamond plate steel with a stainless steel ¼” pin continuous hinge.
4.Rappelling anchor(s) shall be a forged swivel-style anchor with 360° swivel angle and 180° pivot angle and provided with a hot-dipped galvanized finish. The rated load for each unit shall be 10,000 lbs. as designated in NFPA 1402. Each anchor shall be 200% proof tested and include a unique certificate of conformance referencing the specific unit serial number.
5.Overhead rappelling anchor(s) shall include a standard rappelling anchor and an overhead mounting bracket designed to mount to the structural wall system.
6.Rappelling rail(s) shall be hot-dipped galvanized and fully welded assemblies. The rail shall be 48” in height and 45” in width with two cross-bars; one 25” above the roof and one 46” above the roof. Rappelling rails are to be used in conjunction with rappelling anchors to elevate the roof off of the working surface and are not intended as a tie-off point.
7.Standpipe shall be a dry standpipe with 4” diameter schedule 10 pipe and grooved couplings. A 4x2½x2½ F.D.C. shall be provided at the exterior of ground level and 2½” rough brass fire department valves with caps and chains shall be provided at each interior level.
8.Sprinkler run shall be tapped off of the dry standpipe utilizing 1” diameter schedule 40 pipe. Near the tap point, the sprinkler pipe shall include a manual ¼ turn valve to operate the sprinkler head(s). Sprinkler head(s) shall be ½” 5.6k 165° pendent(s).
9.Exhaust fan shall be a wall mounted direct drive fan with shutter. The fan shall have a 36” diameter up to 8,225 CFM. The fan shall be 115VAC, 60 Hz, single phase, with 6.4 full load amps. Power supply by others.
10.Smoke distribution system shall be a self-contained operation unit with an integrated smoke machine and 8 individually controlled fans to distribute smoke to up to 8 locations throughout the training structure. The system shall include a 1300-watt smoke machine designed to produce up to 30,000 CFM. Each distribution fan shall be designed for up to 120 CFM.
2.6 Building Description
1.Section A will be a five-story tower with a six-story elevator shaft and a six-story enclosed stair tower approximately 40’-8” W x 11’-8” L with varying roof heights. The tower will be 20'-9" W x 11’-8" L x 54'-0" H with a 4’-10” W x 11’-8” L x 64’-0” H elevator shaft and a 15’-1” W x 11’-8” L x 64’-0” H stair tower.
a.Four (4) interior floors (2nd, 3rd, 4th, 5th) tower
b.Three (3) flat roofs with concrete working surface and 48” H parapet walls. The concrete mix design and installation is not covered in this section
c.Seven (7) 3’-0” chain gates, one (1) on the elevator shaft roof, one (1) on the tower roof and five (5) on the stair tower roof
d.Eight (8) rappelling anchors on the stair tower roof
e.One (1) 2'-6" x 3'-0" Bilco roof hatch in the roof of the elevator shaft
f.Two (2) vertical ladders, one (1) from the tower roof up to the elevator shaft roof and one (1) from the tower roof up to the stair tower roof
g.One (1) six-story interior stair with welded stair railing
h.Seven (7) 3' x 7’ exterior plate steel door and hardware
i.Eleven (11) 3' x 7’ interior plate steel door and hardware
j.Three (3) 3' x 7’ interior burn room plate steel door and hardware
k.One (1) 3’ x 4’ window opening with latching shutter
l.One (1) 3’ x 4’ access hatch to residential attic
m.One (1) 11’ x 12’ burn room protected with a Padgenite liner system on 4th floor
2.Section B will be a two-story residential/industrial section approximately 21'-11" W x 35'-0" L x 24’-0” H.
a.One (1) gable roof, 5/12 and 9/12 un-equal pitch with perimeter welded guardrail
b.Two (2) 8’-0” chain gates, one (1) on each 35’-0” face of the residential/industrial gabled roof
c.One (1) attic space provided between the gabled roof and the second floor
d.One (1) 3' x 3' framed window openings with latching shutter at exterior gabled end of the attic
e.Nine (9) 3' x 4' framed window openings with latching shutters
f.One (1) 6' x 4' double window with latching shutters
g.One (1) 6' x 7' exterior plate steel door and hardware
h.One (1) 3' x 7' exterior plate steel door and hardware
i.One (1) 3' x 7' exterior burn room plate steel door and hardware
j.Two (2) 3' x 7' interior burn room plate steel door and hardware
k.One (1) two-story interior stair with welded stair railing
l.One (1) 12’ x 12’ burn room protected with a Padgenite liner system
3.Section C will be a one-story annex approximately 21'-11" W x 14'-6" L x 10'-0" H.
a.Two (2) 3' x 4' framed window openings with latching shutters
b.One (1) 3' x 7' exterior burn room plate steel door and hardware
c.Entire room shall be protected with a Padgenite liner system
2.7 Additional Items
A.
2.8 Items to be Included as Options
A.
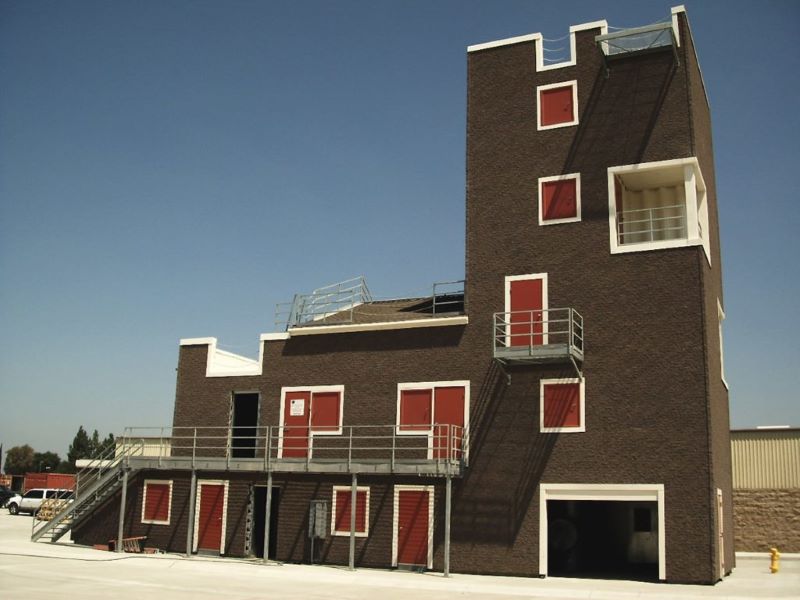
PART 3 – EXECUTION
3.1 Examination
1.Concrete stem wall elevation must be within tolerance of +/- ¼”.
2.Anchor bolts placement must be within tolerance of +/- 1/8”.
3.2 Installation
B.Comply with respective manufacturer’s instructions and approved shop drawings.
3.3 Adjusting and Cleaning
B.Contractor shall properly maintain the site, collect all waste material, place all debris and waste in containers and remove from the site.
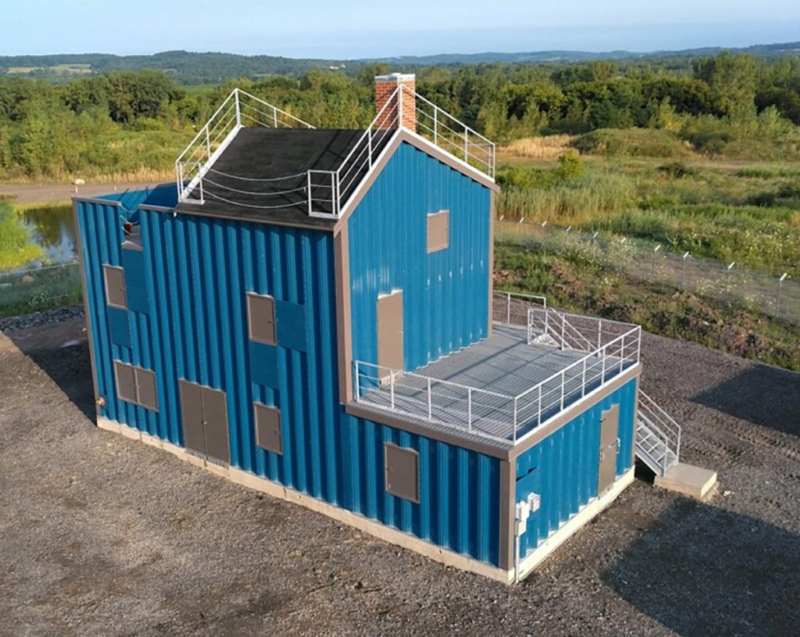
- Pre:None
- Next:Steel Structure Use Spiral Wel 2024/7/28