The Build Process An overview of planning, designing, and erecting a metal building
No Pics.
The Build Process
An overview of planning, designing, and erecting a metal building
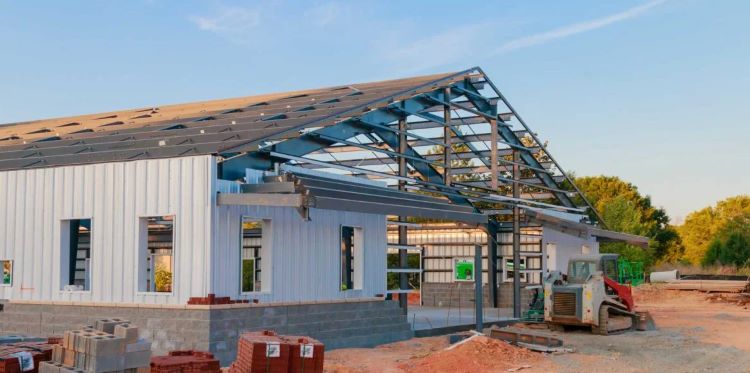
Erecting a metal building
1.Planning
2.Design
3.Ordering
4.Pre-Construction
5.Construction
6.Finishing
An overview of planning, designing, and erecting a metal building with links to guides for each stage of the process, from breaking ground to final inspection and walk-through.
Let's DIG in ...
Step-1: Planning
Planning a building project
As with any large project, careful planning is critical to ensure your build runs smoothly and that you get the most suitable building at the right price.
What will your building be used for? Start by carefully considering what you will use your structure for now and in the future. Although metal frame buildings are modular by design (allowing you to add approximate 6m sections to the length of the building), this needs to be factored in before ordering your building. Bed sure to specify 'expandable end walls' if this is the case.
What size building do you need? We recommend deciding on a size and adding 20% if your budget allows it. You will always fill the space, and one of the main things we hear from first-time buyers is..."I wish I'd ordered a size up." Buildings are available in widths from 30 to 300 feet in 10-foot increments. Lengths are available from 20 feet to as long as you need, in increments of either 20 or 25 feet, based on the standard widths of each bay (see bay spacing).
What height building do you need? The best way to decide on a building's height is to consider the tallest equipment you'll use. Then, add 600mm (as a safety measure) and another 600mm above the door opening to arrive at your eave height. For residential buildings, this will depend on whether you need a single-story (approx.3.4m) or two-story (approx.6.2m) home.
Where will your building be located? Site selection is a crucial step. You will need to verify that the ground will support the weight of the structure and the foundation. You will also need to consider exposure to wind and light along with access to the building.
Please read our guide to planning a metal building project for an in-depth look at the planning stage.
Will a building permit be required? In the majority of cases, the answer will be yes. See our page on permits and building codes for additional details.
Will you require financing? For details on construction loans HELOCs and more, see our guide to metal building financing.
Step-2: Design
Designing a red iron building
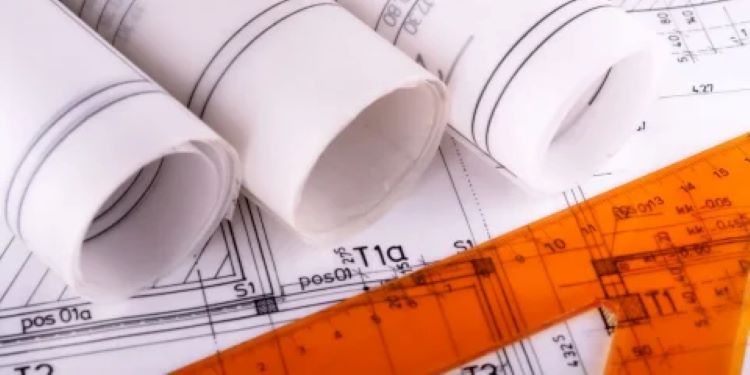
If you are constructing a residential building, you will need to purchase floor plans online or work with a designer to produce these for you. To get started, see our selection of steel building floor plans for a variety of end uses.
Exterior customization options include:
Roof options. Choose from a number of roof profiles, including gable, single-slope, gambrel, or monitor, along with the pitch. Also, choose from a number of different metal roofing material options. Read more on our building roof styles and profiles page.
Color options. Mix and match colors for roof panels, wall panels, and wainscots to compliment your existing structures or match a corporate style. Experiment with our color visualizer and view popular color combinations and color schemes.
Door options. As all buildings are custom-made, you will need to specify the styles, types, and sizes of doors required for your application. For more, see our door options page.
Siding options. All building kits come standard with metal siding panels, but you can replace these with a large selection of other options. See our siding options page for further details.
Structural options. Any number of exterior structural design features can also be added, including roof canopies, wall canopies, and lean-to extensions. Also, consider adding a mezzanine level for additional indoor storage space. See our structural options page for more.
Step-3: Ordering
Ordering a building kit package
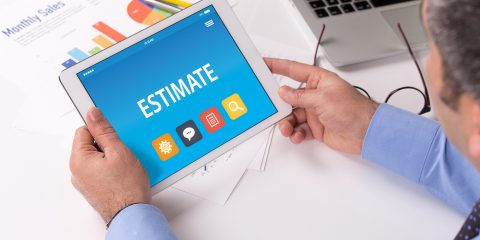
Place deposit. You will be required to place a deposit (normally 10-30%) at this stage. Once the deposit has been placed, your supplier will then finalize the designs with you and supply you with the engineering drawings. The supplier, at this stage, will then forward the drawings to the engineering department for manufacturing.
Contracting. If you are not erecting the building yourself, now is the time to engage local sub-trades, a steel building erection crew, or a general contractor.
Apply for building permits. Now that you have the final drawings for the building, you can begin the permitting process. This can either be done by your GC or yourself. Read our article on building permits and codes.
Step-4: Pre-Construction
Site prep and foundations
Typically, your building will be ready to ship within 2-4 months after placing your order. This allows you plenty of time to arrange permits and prep the site ready for construction.
Site preparation. The site will need to be cleared and graded at this stage. See our article on construction site prep for more details.
Run services to the job site. Before pouring the foundation, you must run power, water, and cable to the site.
Pour the foundation. Based on the structural engineers' foundation plan, you can now have the foundation installed by a local concrete company. Please read our article on metal building foundations for a detailed look at the various options.
Step-5: Construction
PEMB construction project
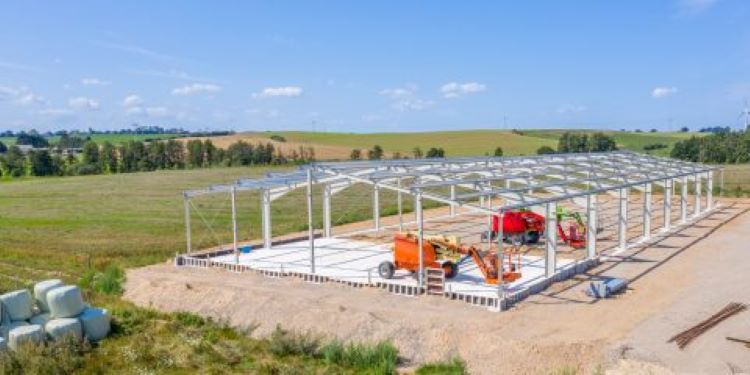
Construction. Read our guide to metal building construction for details on construction options and an overview of the construction process.
Step-6: Finishing
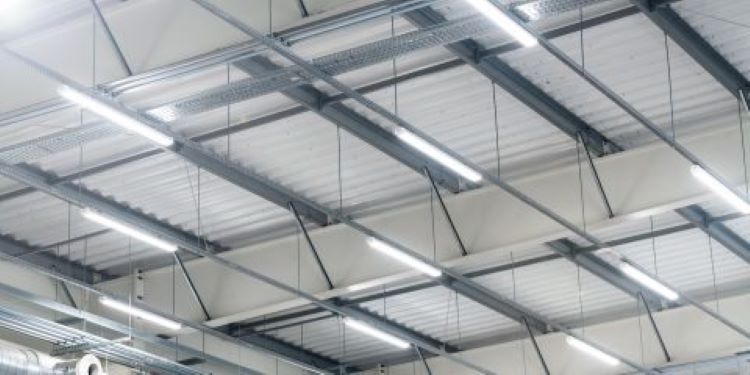
Interior finishing of a steel structure
Install insulation. At this point, you or your contractor must decide which type of insulation to install: fiberglass insulation or spray foam insulation. Insulation is an optional upgrade that can help improve your building's energy efficiency. You can purchase insulation from your building supplier, online, or locally. Read our guide to insulating a metal building for further details.
Interior framing (if required). If you are adding partitions, bathrooms, or a second level to your building, your contractors can now begin this stage of the build process. Read our article on finishing the interior of a steel building for details on the various framing options.
Hookup services. Your contractors will now be able to hook up the utilities.
Walkthrough and final inspection. Inspections are carried out throughout construction, with some being more frequent at critical stages. A punch list is developed during these inspections, which documents issues that still need to be resolved. After an issue is taken care of, it is removed from the list. A final inspection verifies that all the punch-list items have been satisfactorily addressed and that your building has been constructed in accordance with the engineering drawings and any special directives issued during construction. The building inspector will conduct a final inspection to verify that the building has been assembled correctly and meets all local codes. A successful final inspection will allow the department to issue a Certificate of Occupancy.
Would you like to see more information and images of ZHM’s Build Process An overview of planning, designing, and erecting a metal building ? Visit our Photo Gallery.
HOW CAN WE HELP YOU?
ZHM’s world-class team — together with our raw material suppliers and subcontractors — works to solve your most challenging design, engineering, farbrication or construction issues.
Contact ZHM by telephone at +86 135-8815-1981 (wechat and whatsapp) or send us your questions via email to info@zhmsteelworks.com