Morton Salt Mines,USA | Mine A-Frame Headframe Steel Works With Hoist Houses | ZHM,China Manufacturer Factory Supplier
Mine A-Frame Headframe Steel Works With Hoist Houses
for Morton Salt Mines,USA
ZHM Huawu Steel was recently awarded the fabrication and installation of not one, but two, headframes for Morton Salt Mines,USA
Our first award is a design-build headframe where we are working with Hatch as our partner. This headframe is in Ohio, USA and is scheduled to be erected the spring of 2021.
Our second headframe is a fast-track project. Our projects department, engineering department and fabrication facilities will meet the challenge head-on, with erection to start this fall. It is exciting to note that we are heading all the way down to the Gulf of Mexico in Louisiana, USA to erect the second headframe.
A history of ZHM Mining Headframes
ZHM Huawu Steel has a long history of fabricating and erecting mining headframes. And they kept getting bigger and bigger!
In 2006, ZHM Huawu Steel provided connection design, detailing, fabrication, and delivery of the world’s largest mining headframe at the Mosaic Potash mine in Esterhazy. This mine shaft head frame stands 93m above grade and includes girder fabrications weighing 95 tons, 38m in length. It was not to be the largest for long…
In 2009, The Potash Corporation of Saskatchewan (PCS) Allan Mine undertook an ambitious expansion, designing a specialized headframe that could be built over top of the existing headframe with concurrent operations. At the time of construction, this headframe was the tallest in the world, later to be surpassed by the BHP Jansen Mine Service Shaft headframe…
In 2012, ZHM Huawu Steel executed the fabrication and supply of the structural steel for the service shaft A-Frame and support buildings at the BHP Jansen Potash Mine in Saskatchewan. This headframe increased the mine to an ultimate capacity of eight-million tonnes a year, making it the world’s largest potash mine.
ZHM Huawu Steel Role
ZHM Huawu Steel handled supplying, fabricating and applying a meticulous 3-coat paint system on the structural steel. Additionally, we were entrusted with the installation supervision of the new headframe. Our commitment to quality and precision was paramount throughout this multifaceted undertaking.
Overcoming Challenges
In the demanding 5-week shutdown period, aligning all components for completion was challenging. However, through meticulous planning, efficient coordination, and unwavering dedication, we successfully overcame these challenges, ensuring the timely completion of the headframe installation.
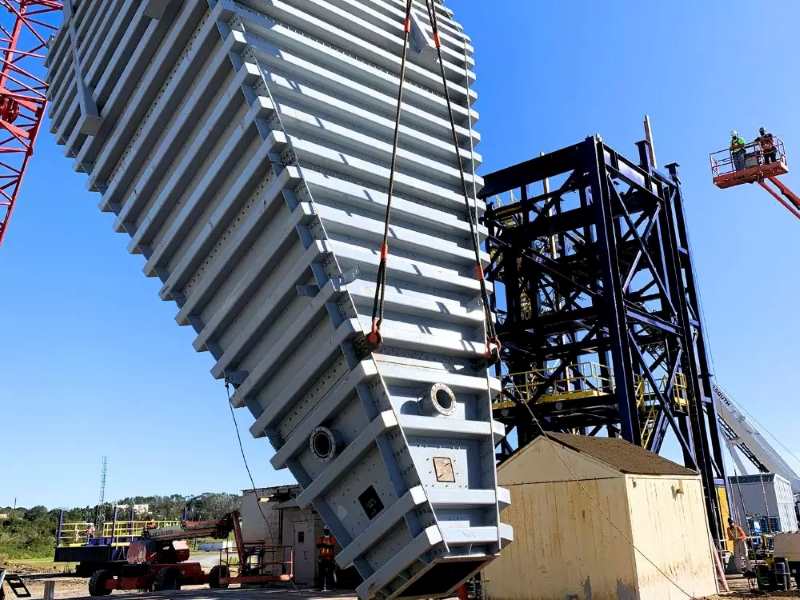
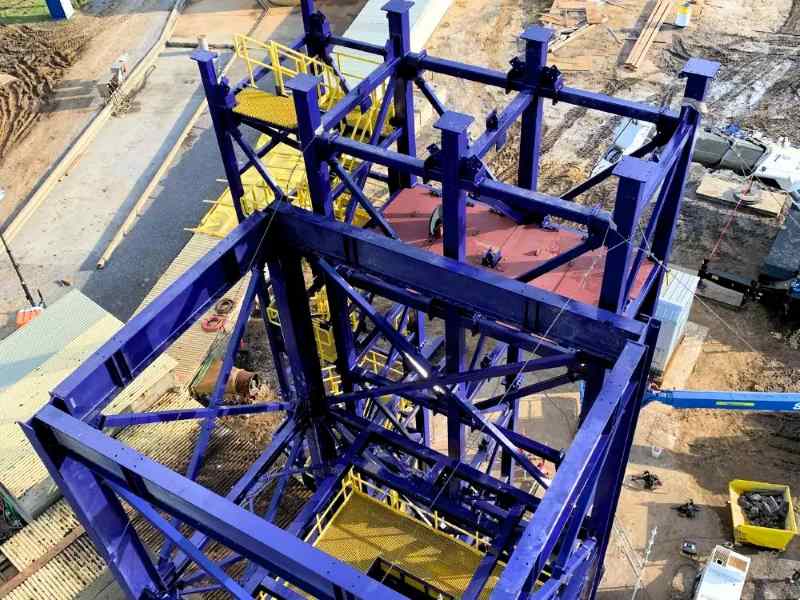
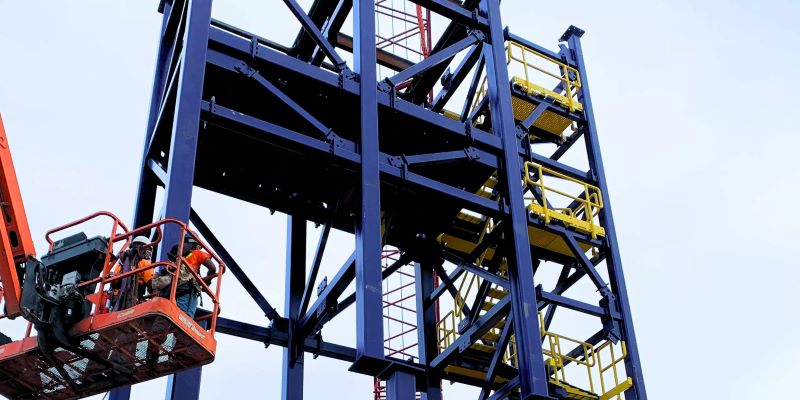
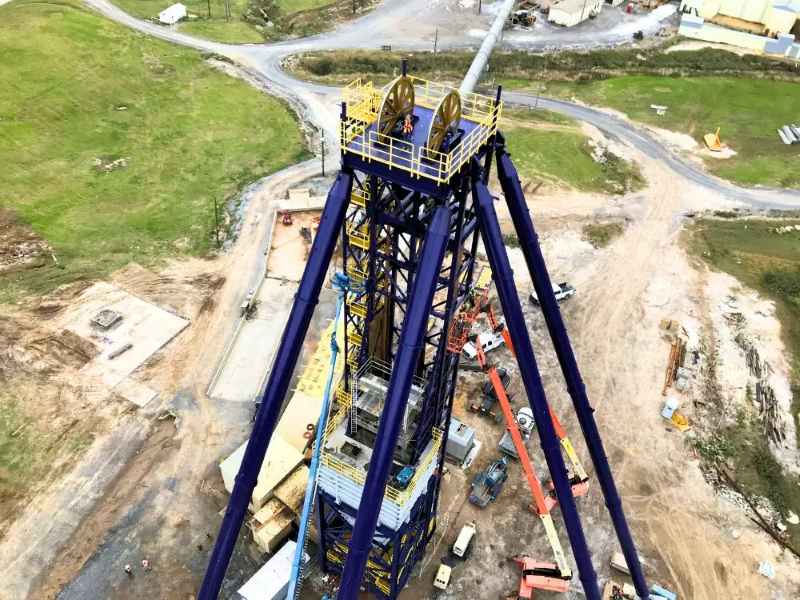
So What's a headframe?
A headframe (gallows frame, winding tower, hoist frame, pit frame, shafthead frame, headgear, headstock, poppethead) is the structure above an underground mine shaft, built for hoisting machines, people, and materials.
A steel headframe is less expensive than a concrete headframe; the tallest steel headframe measures 87 m.Steel headframes are more adaptable to modifications (making any construction errors easier to remedy), and are considerably lighter, requiring less substantial foundations. As steel headframes are easier to design, they have the potential to utilize "off the shelf" design tools. Construction of a steel headframe can be easily interrupted and restarted if necessary for statutory holidays or bad weather, where slip forming concrete is not. Upon mine closure and mine reclamation a steel headframe is easier to demolish and may have value as scrap metal.
A mine hoist winder is a critical piece of equipment used in underground mining to transport personnel, equipment, and materials up and down the mine shaft. The mine hoist winder typically consists of a drum or sheave around which the hoisting rope is wound, a motor or engine to provide the necessary power, and various safety devices and controls to ensure safe operation. Here is a general overview of how a mine hoist winder works:
Power Source: The mine hoist winder is powered by an electric motor, a diesel engine, or sometimes a hydraulic system. The power source provides the energy needed to lift and lower the hoist cage or skip.
Drum or Sheave: The hoisting rope is wound around a drum or sheave. As the drum turns, the rope is either wound up or let out, raising or lowering the hoist cage or skip in the mine shaft.
Hoist Cage or Skip: The hoist cage is a platform that carries personnel and materials in the vertical shaft. A skip is a container used to transport bulk materials. The hoist cage or skip is attached to the hoisting rope and moves up and down the shaft as the drum rotates.
Safety Devices: Mine hoist winders are equipped with various safety devices to ensure safe operation. These may include overspeed protection systems, emergency brakes, slack rope detectors, and other safety features to prevent accidents.
Controls: The operator controls the mine hoist winder using a control panel located either near the hoist or in a control room. The controls allow the operator to start, stop, and control the speed and direction of the hoist.
Monitoring: The operator monitors various parameters such as load weight, speed, rope tension, and other critical factors to ensure safe and efficient operation of the mine hoist winder.
Maintenance: Regular maintenance of the mine hoist winder is essential to ensure its safe and reliable operation. This includes inspections, lubrication, and replacement of worn components.
Overall, the mine hoist winder plays a crucial role in underground mining operations by providing a safe and efficient means of transporting personnel, equipment, and materials in and out of the mine shaft. It is essential for miners to follow proper procedures and safety protocols when using a mine hoist winder to prevent accidents and ensure the well-being of everyone involved.
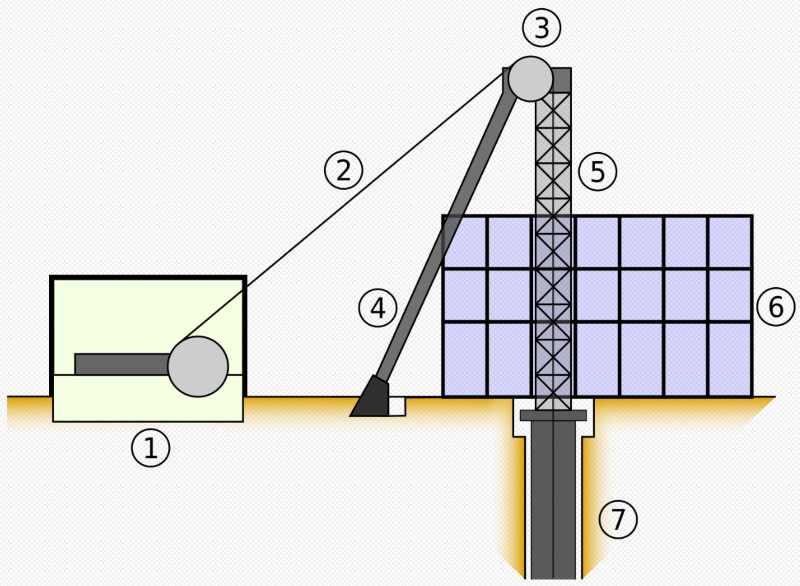
Schematic of headframe
- hoist
- cable
- wheel
- sheer
- false edge
- hoistroom
- mineshaft
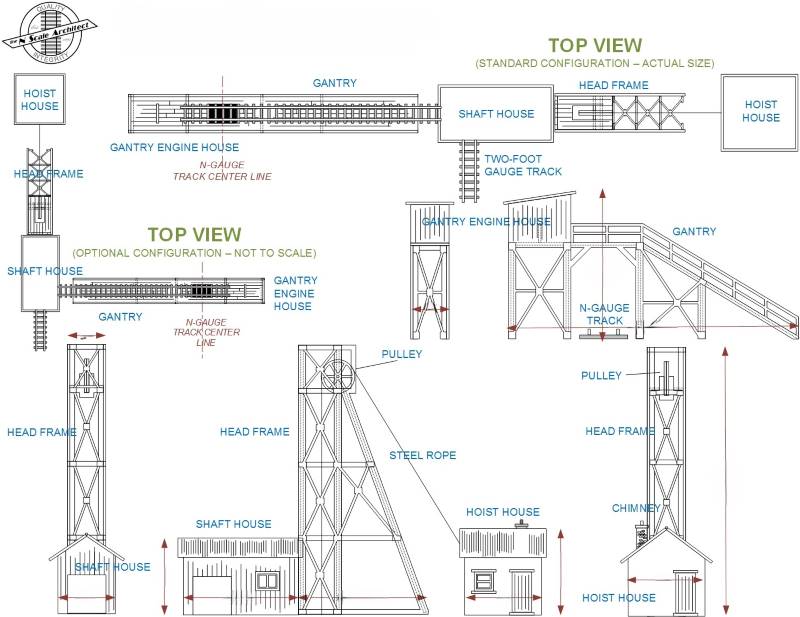
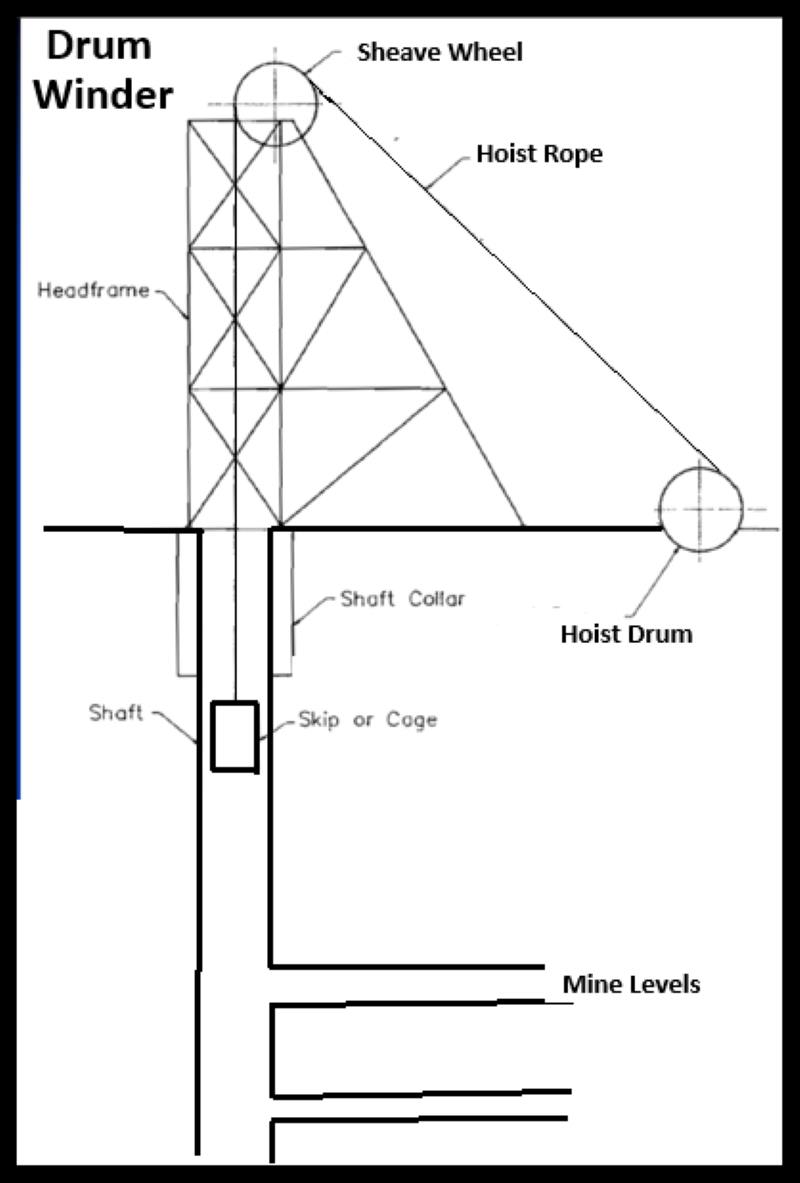
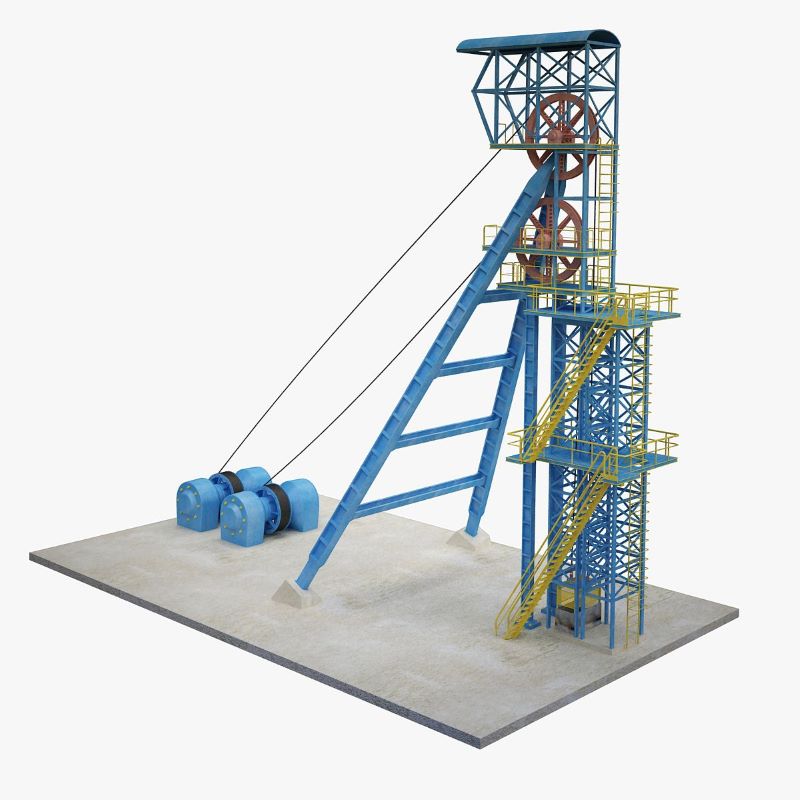
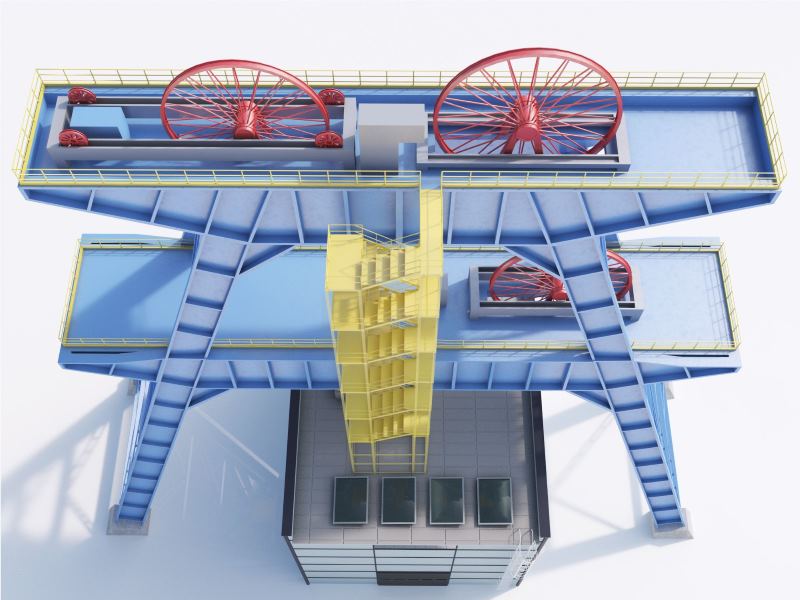
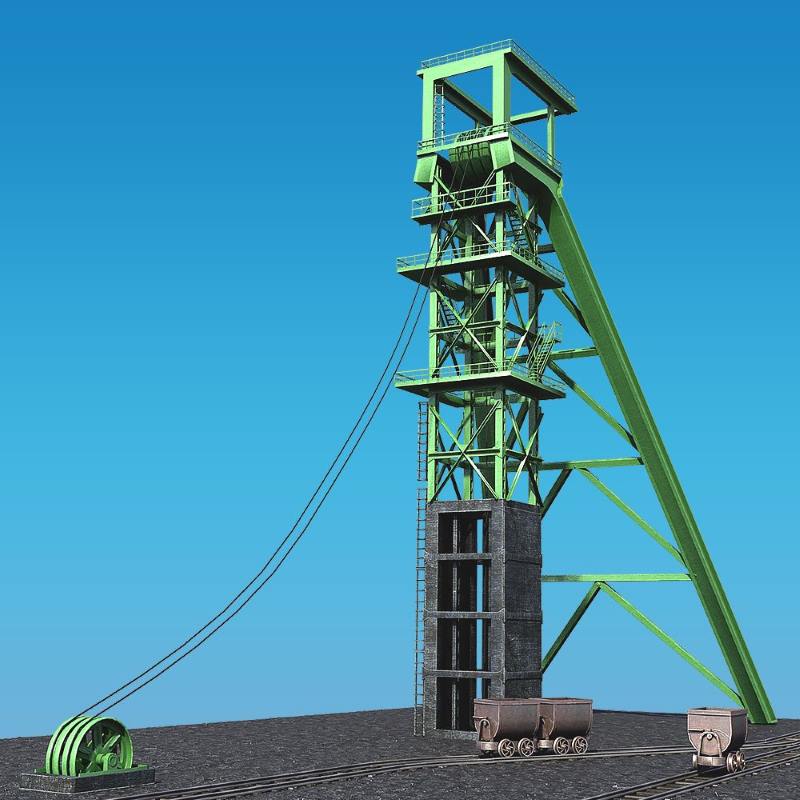
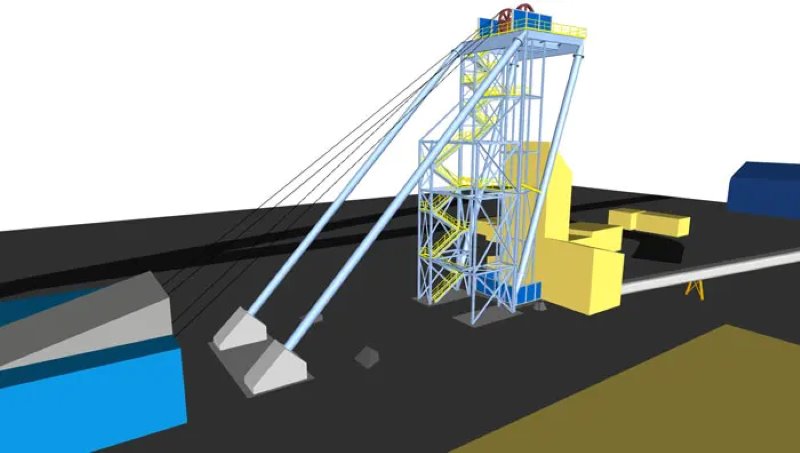
Why ZHM Huawu Metal Mine A-Frame Headframe Steel Works With Hoist Houses ?
![]()
|
![]()
|
![]()
|
![]()
|
Reliable and Customized Designs | Cutting Edge Designing Process | Free Online Price System | Easy Bolt-by-number Assembly |
![]()
|
![]()
|
![]()
|
![]()
|
Over Two Decades of Experience | Value For Money | Unmatched in Quality and Craftmanship | Excellent Customer Service |
Would you like to see more information and images of ZHM Huawu Steel's Metal Mine A-Frame Headframe Steel Works With Hoist Houses ? Visit our Photo Gallery.
HOW CAN WE HELP YOU?
ZHM’s world-class team — together with our raw material suppliers and subcontractors — works to solve your most challenging design, engineering, farbrication or construction issues.
Contact ZHM by telephone at +86 135-8815-1981 (wechat and whatsapp) or send us your questions via email to info@zhmsteelworks.com