Zurich North America Headquarters | Steel High-rise Office Buildings | ZHM,China Manufacturer Factory Supplier
Steel High-rise Office Buildings | Zurich North America Headquarters,Chicago, USA
PROJECT NAME: Zurich North America Headquarters | ADDRESS: Chicago, USA |
OWNER: ZURICH INSURANCE GROUP |
STRUCTURE TYPE: Frame Structure |
EPC: Clayco |
BUILDING CATEGORY: High-rise structural steel |
FLOORS: 12 |
Developer: ZURICH INSURANCE GROUP |
General Contractor: Clayco |
Steel consumption: 4822.84ton(ZHM scope) / 5042 t (Total) |
Building area: 70,555 ㎡; |
|
Number of floors:
11 above ground and 1 underground; 1-6 floors of H-shaped steel column, 7-11 floors of H-shaped truss column and truss beam; Maximum beam span is 13.85m. main steel structure materials use Q390 grade materials (Fy=390Mpa).
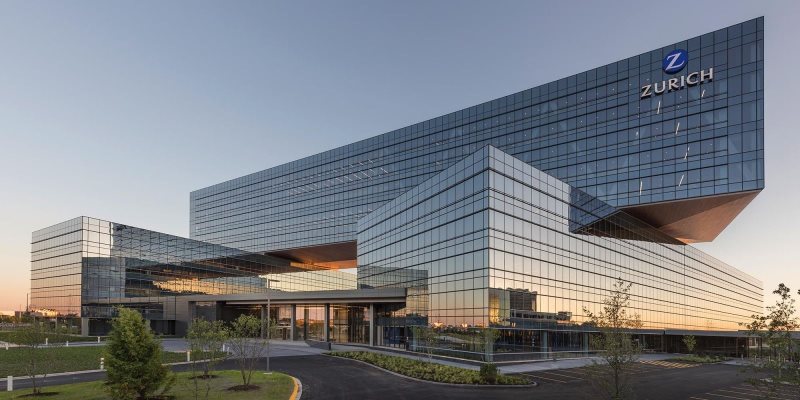
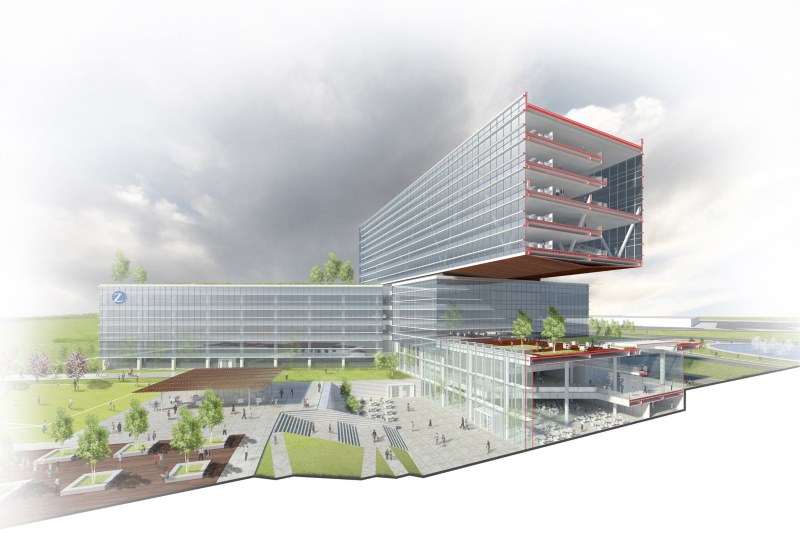
Introduction:
As a Top 10 insurance company in the world, Zurich Insurance has more than 60,000 employees. Located in Chicago, US, this office building serves as Zurich’s headquarter in North America with architectural features emphasizing reliability and success as an insurance company.Zurich North America's stunning 783,800-square-foot headquarters in Schaumburg bucks the trend of corporations abandoning suburban campuses for city centers. The massive glass, steel and wood structure is a throwback to an era when architecture was highly valued as a way for a company to make a statement about itself.
The 783,800-square-foot Zurich North America Headquarters is the largest build-to-suit office project completed in the Chicago area in the last 15 years, but this striking addition to the I-90 corridor in Schaumburg is not just notable for its size. The unique building form is comprised of the three long rectangular bars shown The east and west lower bars rise six stories from the ground, while the five-story upper bar sits on top of – and spans between – the two lower bars.
The dramatic 180-foot main span and the two 60-foot cantilever spans on each end are made possible by two steel trusses at the exterior faces of the upper bar and a third truss centrally located in the interior. Usually, a requirement to transfer five levels of office loading over such long spans would be an arduous task associated with a significant cost premium. In this case, however, loads from the upper bar are not carried by a one-story or two-story transfer truss. Instead, the main structure of the entire upper bar is a truss. By replacing vertical columns with truss diagonals throughout the entire five-story upper bar office space, the full 68-foot height of the space becomes structural depth for the truss, allowing chord axial forces to be minimized.
Additional efficiency is achieved by making the truss continuous over its supports, and ideally proportioning the cantilever spans to balance forces and deflections in the main span. These effects further reduce chord axial forces and result in deflections which are approximately equal at the main span and the cantilevers.
Although the depth and continuity of the trusses make them inherently stiff, and therefore not prone to large deflections, the trusses were fabricated and erected with slight cambers to mitigate concerns about floor levelness. By super-elevating initial panel point elevations by up to one inch, the initial truss deflection due to dead load was effectively eliminated. Meanwhile, live load deflections are less than ¾-inch at both the main span and the cantilevers.
The design of the truss chords was governed by the axial truss forces acting in combination with significant bending moments, since the chords also act as 60-foot continuous W36 steel girders supporting the conventional 45-foot composite steel framing. A series of large truss chord penetrations (40 inches wide x 22 inches high) were carefully coordinated to allow mechanical services to fit within the standard 13-foot-six-inch floor-to-floor heights without compromising the ceiling height.
While coordination of the deep truss chords with mechanical services was a challenge, coordination of the truss diagonals with the interior office space was less so. As the centerpiece to the most iconic component of the project, the trusses are featured and celebrated by the architecture rather than hidden behind partition walls.
Early in the design phase, the design team worked closely with the contractor’s connection engineer to develop economical splices and compact connections at the truss nodes. The typical truss diagonal-to-chord node (Figure 4) was shop-welded at ZHM Huawu and delivered to the site in one piece with the chord, with bolted diagonal splices accommodated on both sides of the node. Where possible, bolt quantities were reduced by taking advantage of bearing, such as in compression diagonals which were not subject to load reversals.
With a roof height of 152 feet, the building will not be confused with the tallest high-rise office buildings found in downtown Chicago. Still, the 480-foot wide wind sail of the upper bar, in combination with the Exposure C wind loads blowing off the expressway from the south, creates substantial overturning forces that required creativity in the layout of the two braced frame cores which stabilize each end of the upper bar.
The typical elevation of the primary north-south braced frames is shown . It was critical to take advantage of the large gravity loads present in the columns supporting the main trusses to minimize foundation tensions. However, the trusses are laid out on a 45-foot module, while the extent of the braced frames was limited to the 29-foot-8-inch width of the elevator core. Outrigger braces were provided directly beneath the upper bar at the Level 6 mechanical level at each of the four brace lines to engage the truss support columns and their beneficial gravity loads. In addition to reducing the uplift forces, the extra depth of the structural system, combined with the high axial stiffness of the large truss support columns, ensured that lateral drifts could be controlled with a minimal steel weight premium beyond what was required for strength.
Four large atrium spaces give the interior a dramatic feel befitting the project, and a series of feature staircases connect the various levels served by the atriums. The longest, shown in Figure 6, spans 40 feet between Level 9 and a 17-foot cantilever landing at Level 10, and another 50 feet between the Level 10 landing and Level 11.
Given the susceptibility of long-span staircases to vibration, a series of dynamic analyses were undertaken to predict the vertical accelerations at mid-span of the stair under the worst case of a rapidly descending individual. Since the dynamic response of a long-span stair is a highly nonlinear problem, it is possible for a moderate increase in stiffness to result in dramatically improved behavior. In this case, the initial stair design based on strength and deflection was stiffened by optimizing the steel stringer profile, with a 3-inch increase in depth and a modest increase in steel weight. This reduced the estimated stair accelerations under the controlling case by more than a factor of 3 compared to the initial design.
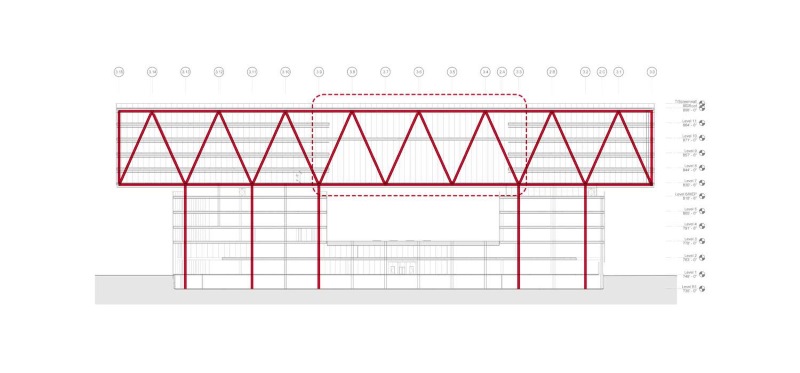
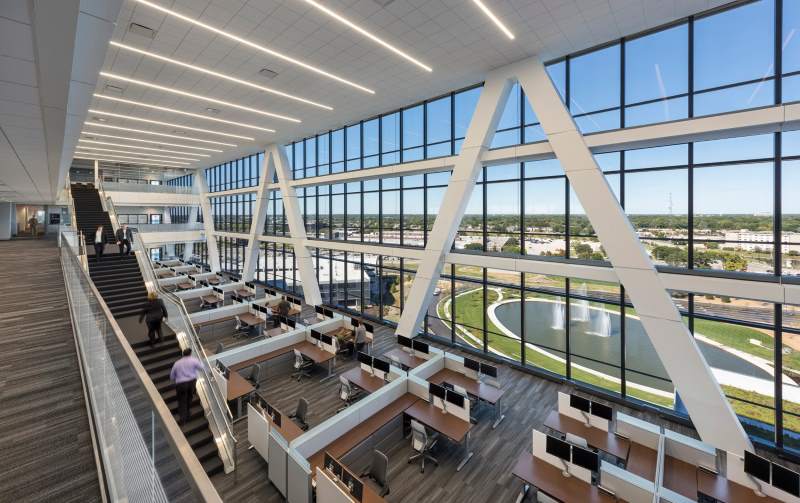
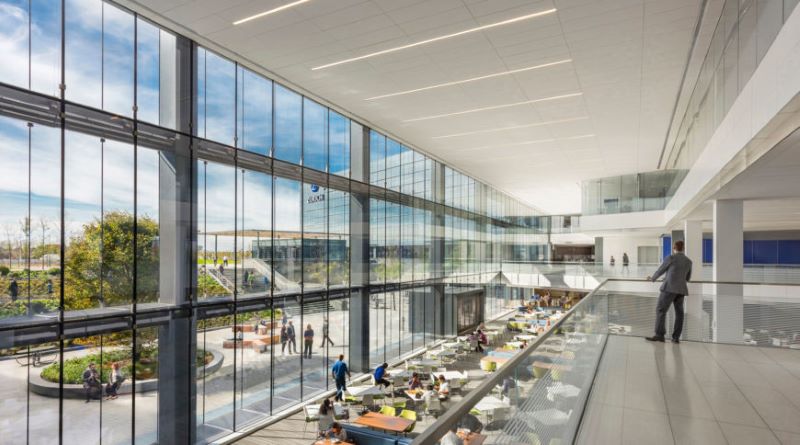
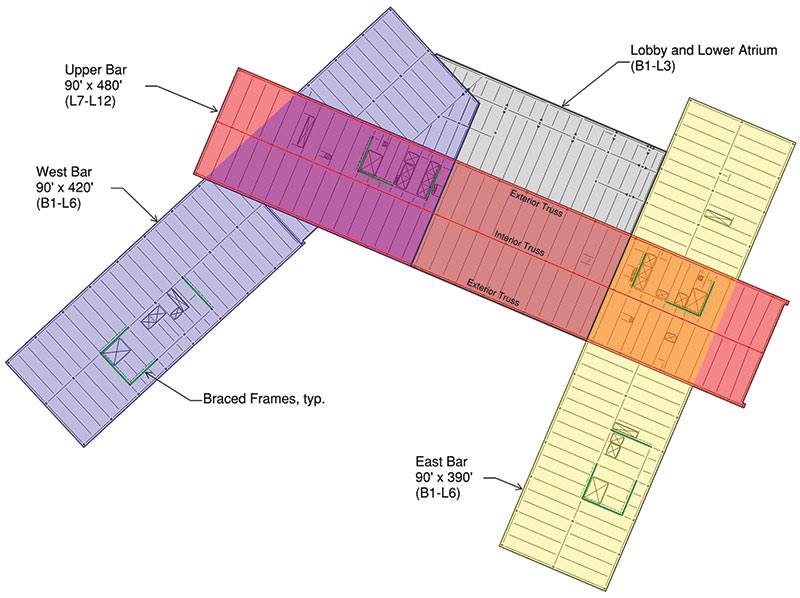
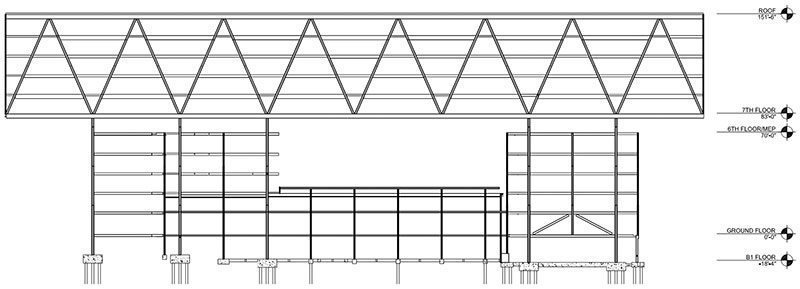
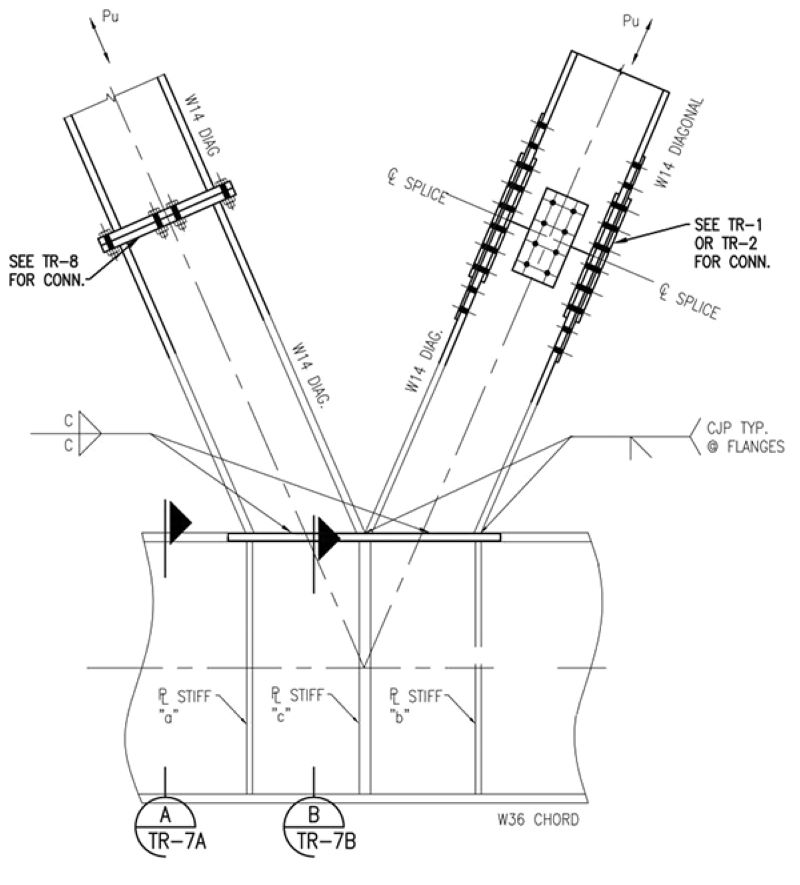
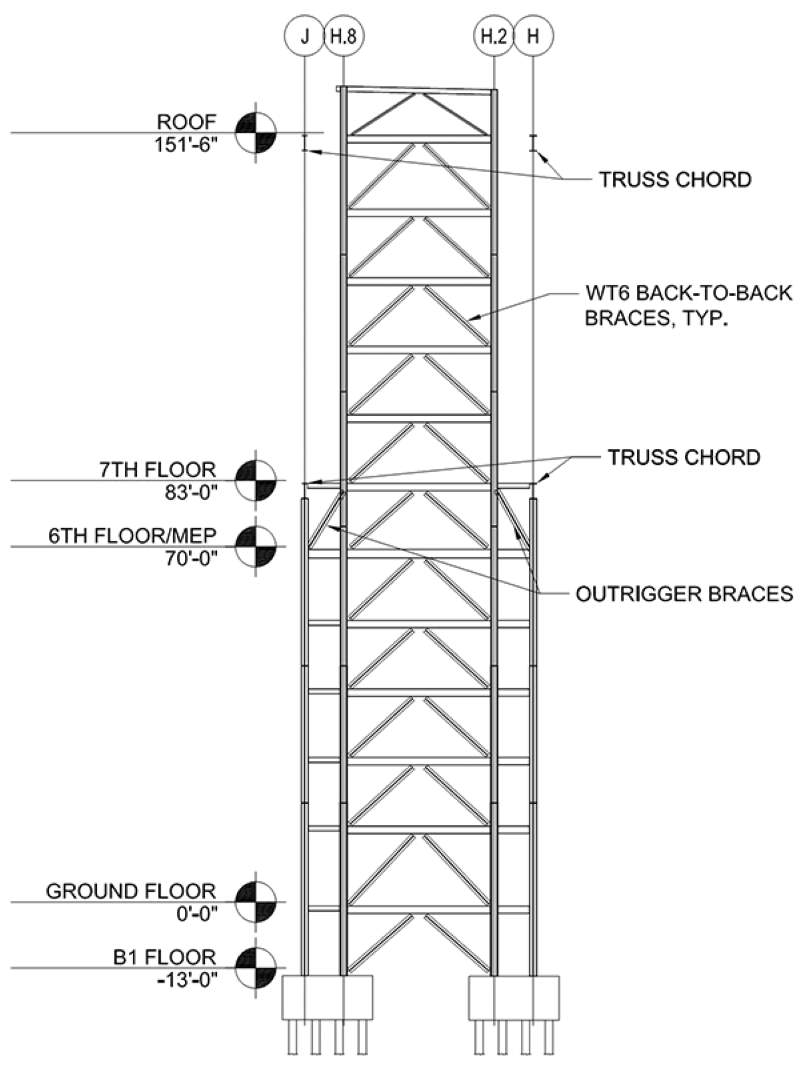
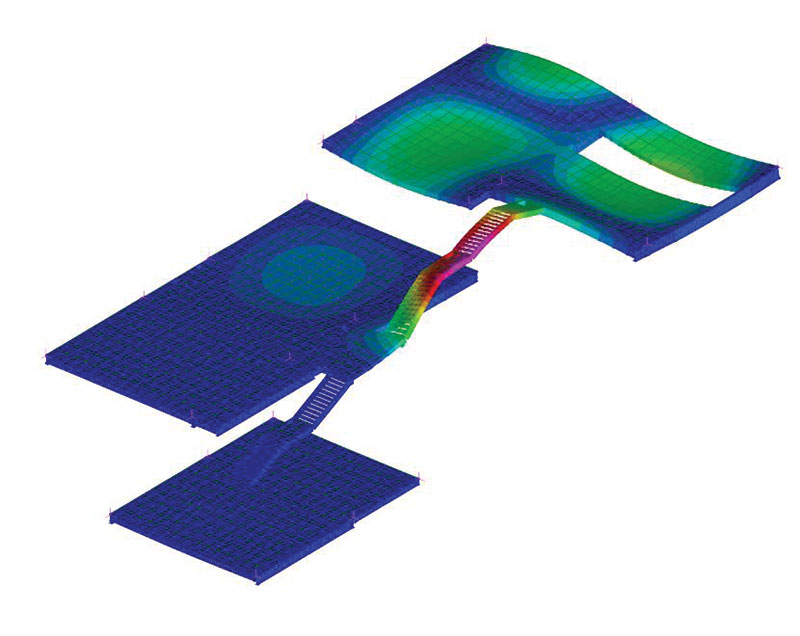
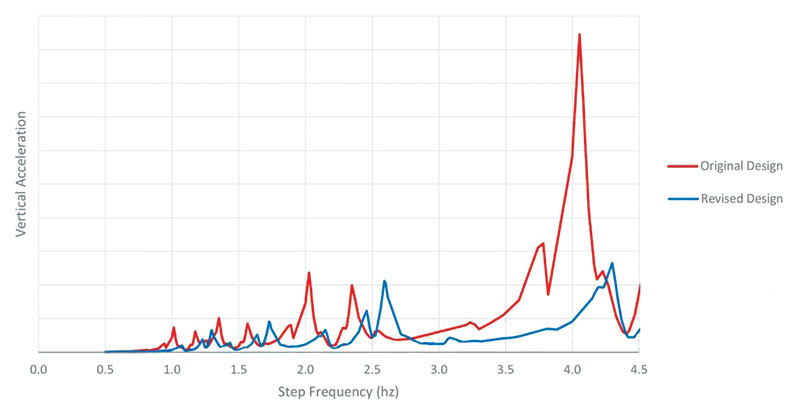
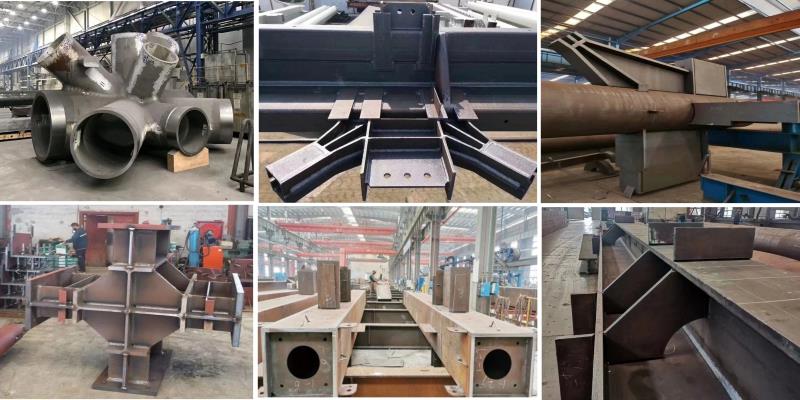
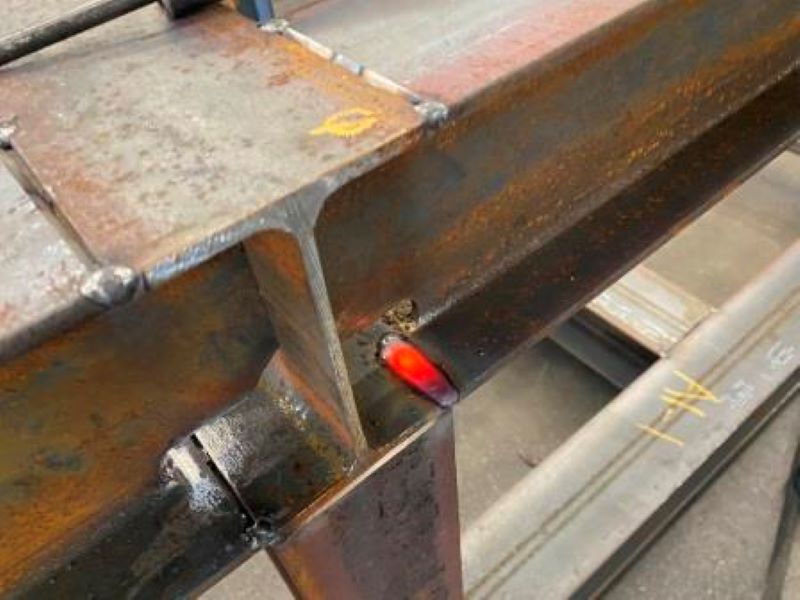
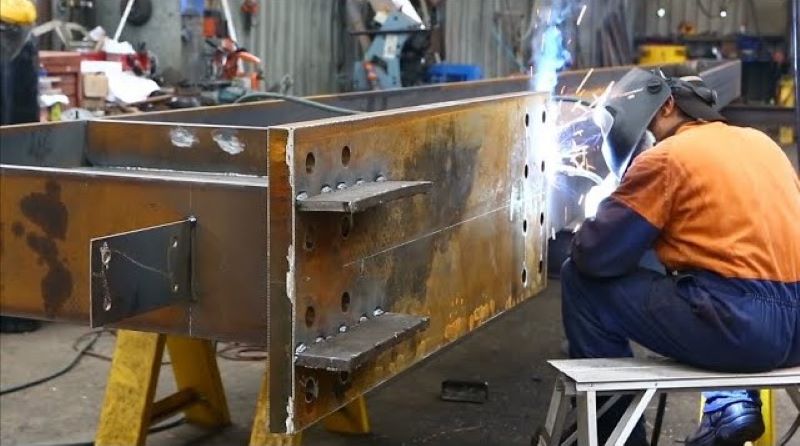
Glass
The most advanced facade assembly occurs along the glazed south-facing wall of a three-story cafeteria where a ventilated double-wall facade was specified. Here, to verify performance and optimize the façade for reduced energy consumption, Thornton Tomasetti provided computational fluid dynamics (CFD) modeling. The 4.5-foot-wide double wall with integrated shades is designed to reduce solar gains in summer, while increasing the gains in the winter, as well as to improve daylighting, resulting in an estimated 33 percent energy savings in the adjacent space.
IGU make-up; 25.5mm Low Iron SGP Toughened Heat soaked Laminate; 12mm Black Spacer; 10mm Low Iron Low E Tempered Heat Soaked; Argon Gas Filled
Largest Unit- 1504mm X 4931mm (59” X 194”)
Details
The curtain wall facade wraps outboard of three super scale trusses that are set 60 feet on center, achieving an 180-foot span over the middle of the campus, and a 30-foot cantilever at the perimeter. The three primary “bars” stacked and arranged to maximize views of the surrounding landscape and optimize solar orientation.
The architectural character of the 783,800-square-foot, design-build complex reinforces an image of reliability and success through its bold simplicity in form, a timeless material palette, and its commitment to sustainability. Composed of three primary “bars” that are offset and stacked, the arrangement creates unique spaces for collaboration, open views of the surrounding landscape, optimizes solar orientation for amenities, and provides programmatic flexibility not found in typical office buildings. The top “bar” of the complex soars 11 stories and cantilevers toward downtown Chicago, providing visual identity along the interstate while projecting the strength and future focus of the company.
Zurich currently employs approximately 2,500 people in Schaumburg and also has an office in downtown Chicago. The new campus aligns with Zurich’s commitment to building sustainable communities with a focus on energy and operational efficiencies, wellness and includes input from employees to create the best workspace for the future.
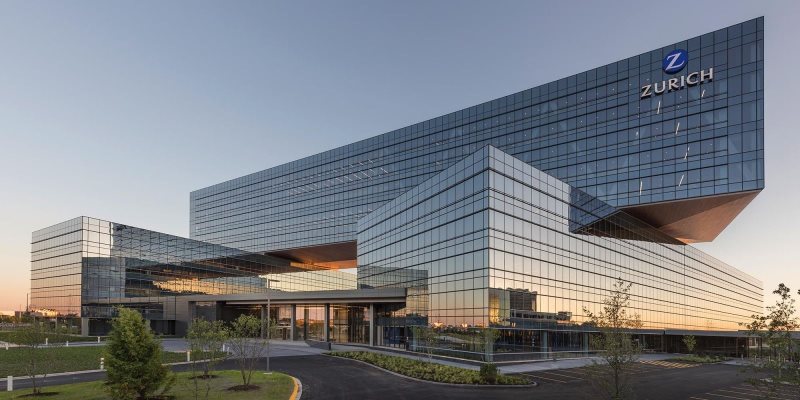
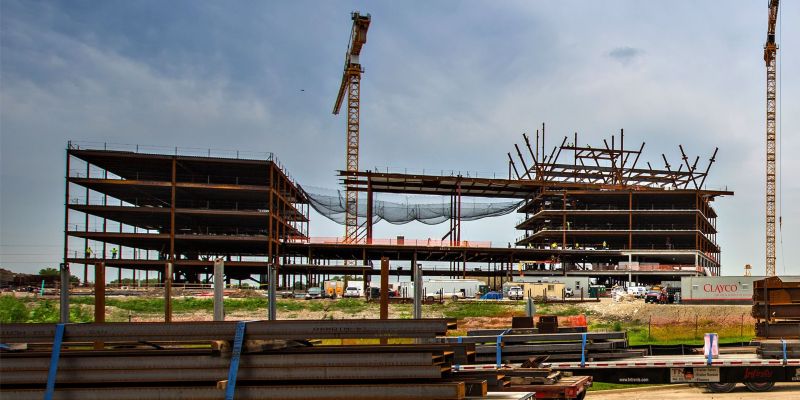
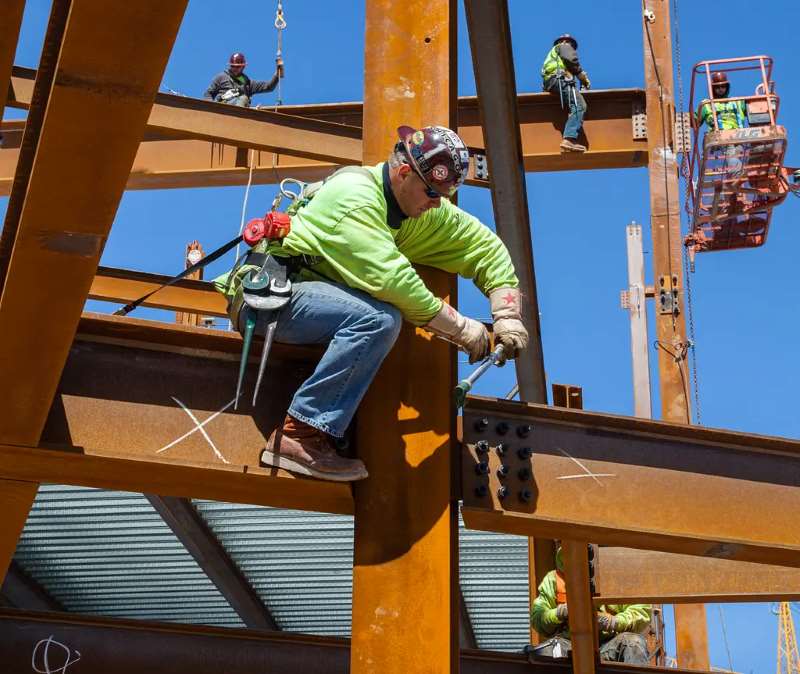
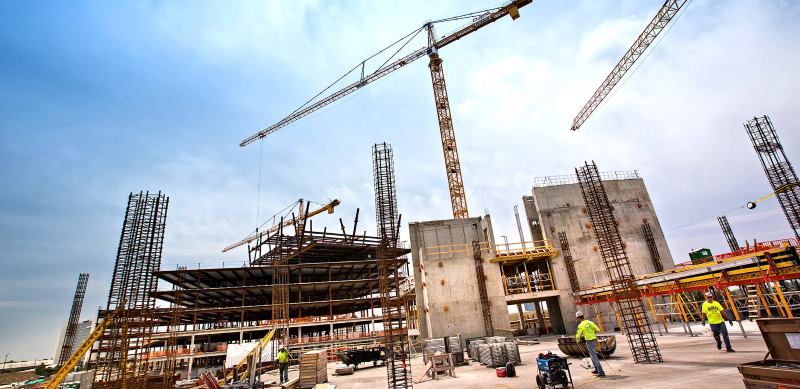
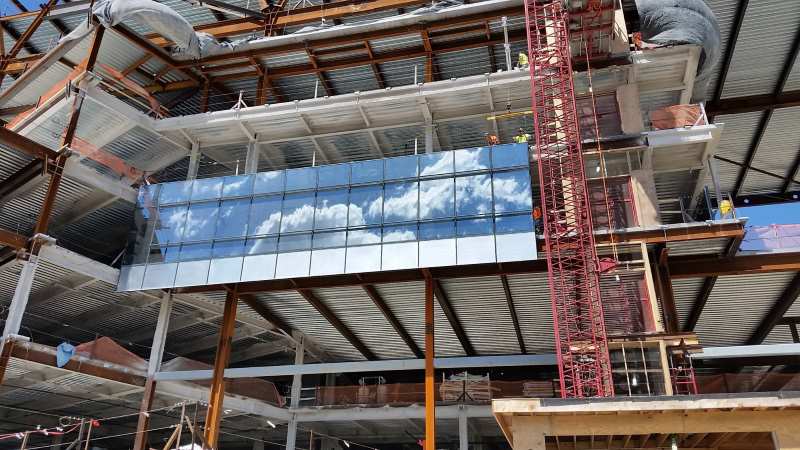
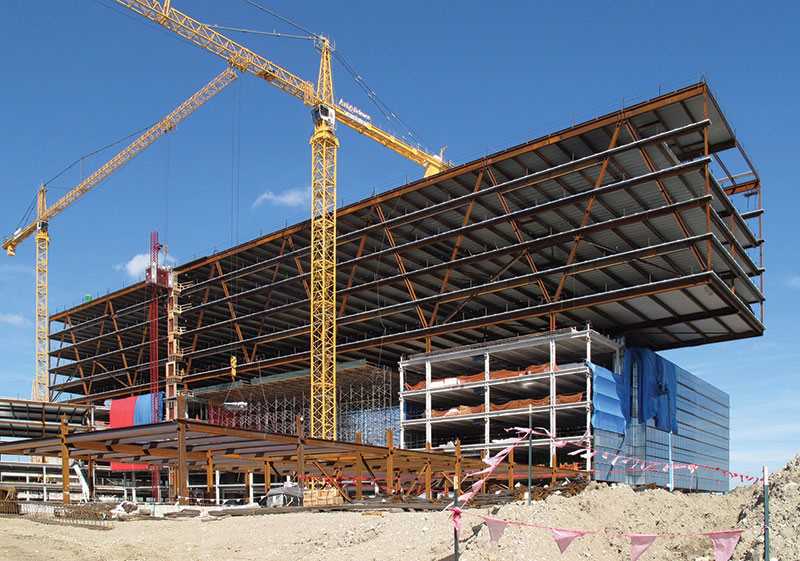
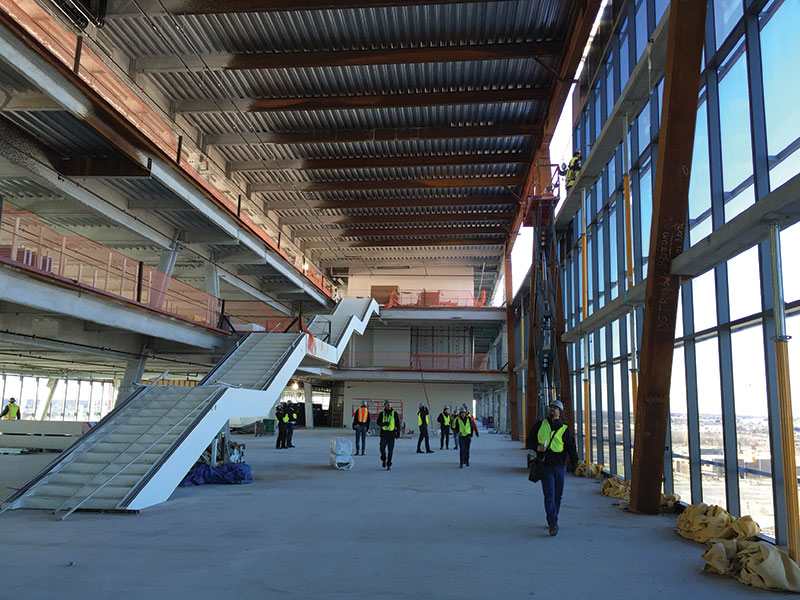
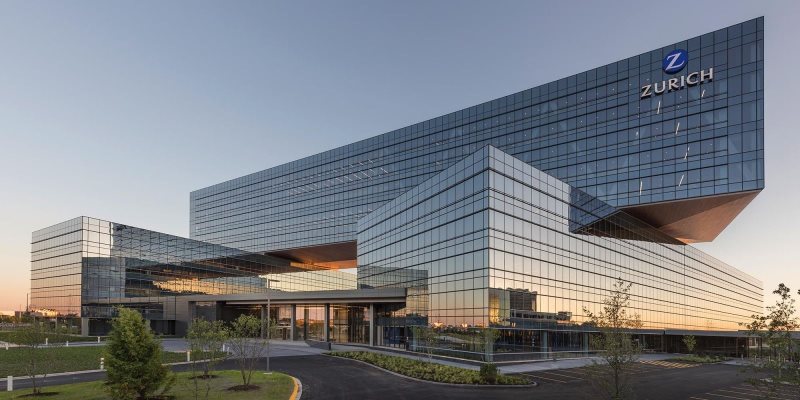
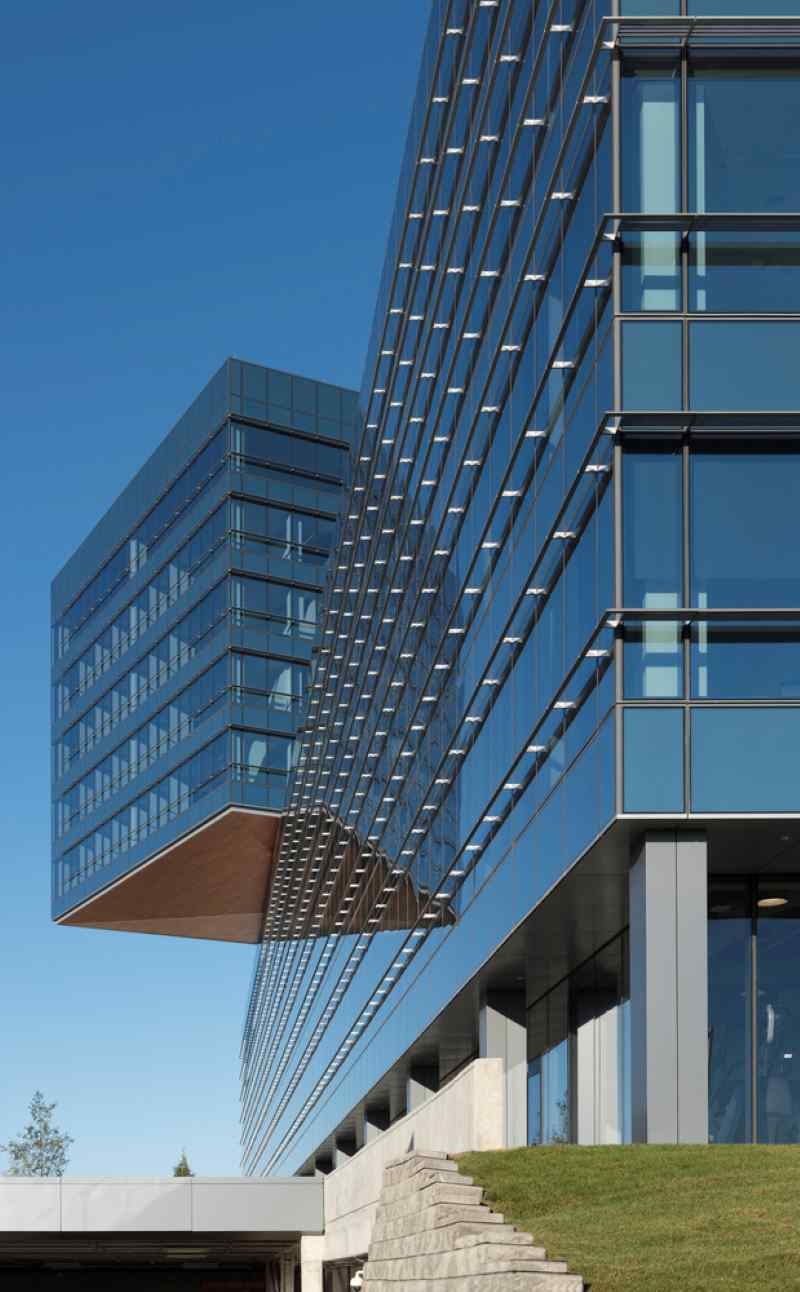
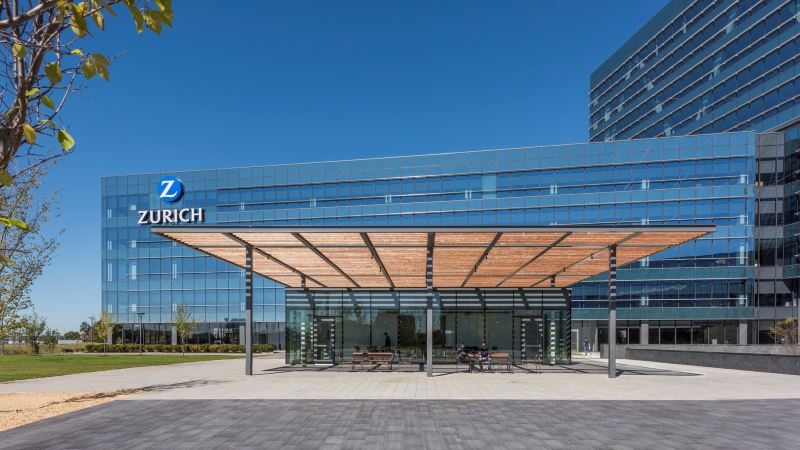
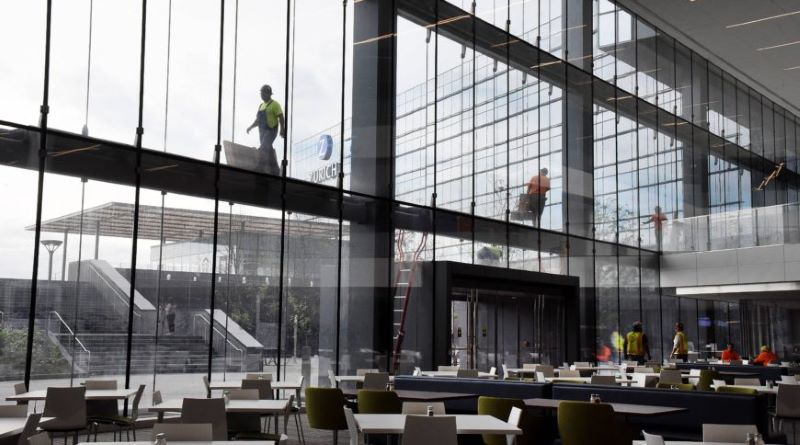
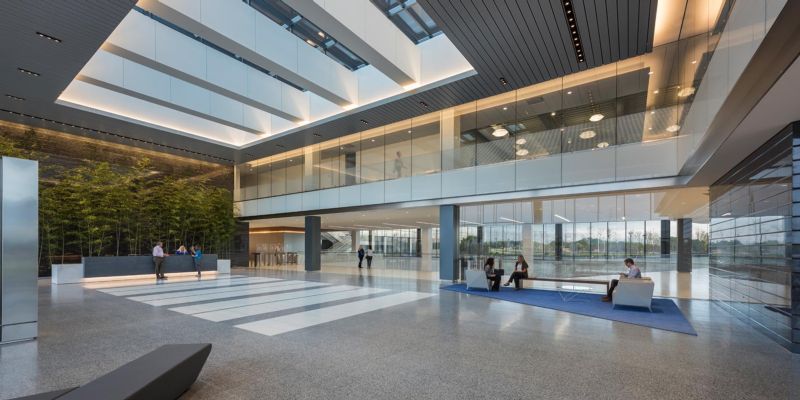
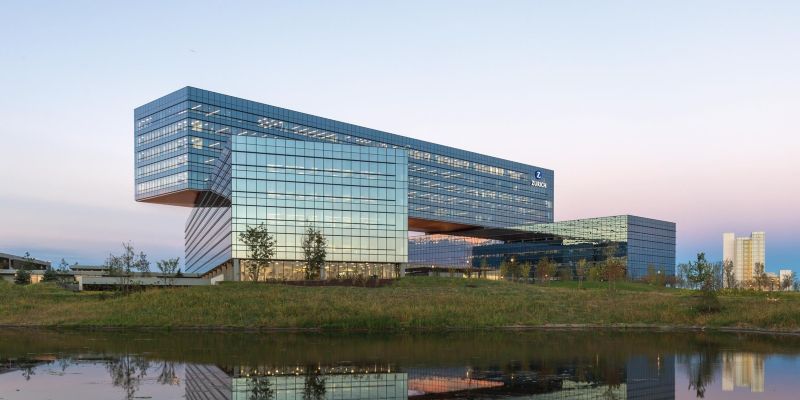
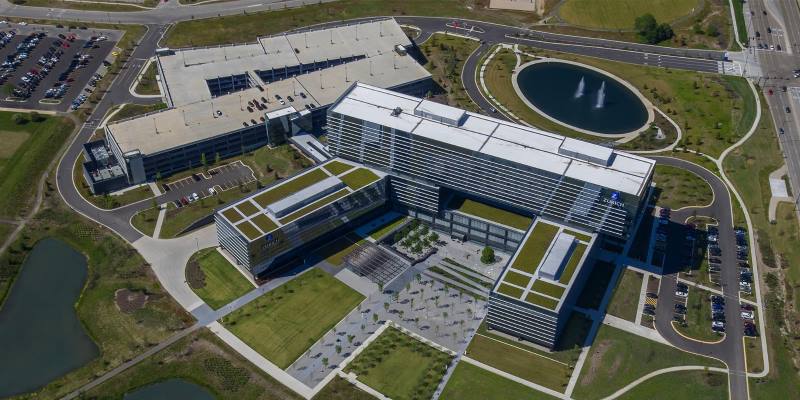
Why ZHM Huawu Metal Steel High-rise Office Buildings for your group company Headquarters ?
![]()
|
![]()
|
![]()
|
![]()
|
Reliable and Customized Designs | Cutting Edge Designing Process | Free Online Price System | Easy Bolt-by-number Assembly |
![]()
|
![]()
|
![]()
|
![]()
|
Over Two Decades of Experience | Value For Money | Unmatched in Quality and Craftmanship | Excellent Customer Service |
Would you like to see more information and images of ZHM Huawu Steel's Metal Steel High-rise Office Buildings for your group company Headquarters ? Visit our Photo Gallery.
HOW CAN WE HELP YOU?
ZHM’s world-class team — together with our raw material suppliers and subcontractors — works to solve your most challenging design, engineering, farbrication or construction issues.
Contact ZHM by telephone at +86 135-8815-1981 (wechat and whatsapp) or send us your questions via email to info@zhmsteelworks.com