Steel Reefer Rack Detailing Design Factors for Exporting to Europe
Steel Reefer Rack Detailing Design Factors for Exporting to Europe

Content Index:
Part 1: Safety
Part 2: Handrails
Part 3: Access Gates and Access Control
Part 4: Stairs
Part 5: Flooring
Part 6: Roofing
Part 7: Nameplates and Signs
Part 8: Electrical Fittings
Part 9: Earthing
Part 1: Safety
1.1.Safety details (e.g. handrails, kicker plates, staircases) shall comply with EN 13586 and ISO 14122 requirements - particularly sections on marine terminals, walking/working surfaces and means of egress.
1.2.The safety of the reefer rack engineer is a main concern in the design of the reefer rack. Same safety design philosophy as per existing terminal shall be included in the design.
1.3.The ARMG carrying a container will always travel in the same path, crossing the reefer racks over the centre. This centre construction will be a separate construction connected with shear bolts to both side sections. In the event of a collision, this centre section will collapse, while both side structures with the stairs will remain standing. When a container passes over the rack a visual and audible alarm will alert the reefer rack engineer. During this period the engineer should not be in the centre area.
1.4. A roof will be constructed over the entire reefer rack, partly for protecting the reefer rack engineer from the rain, partly for protection from falling rocks or smaller items which cloud fall from the container or crane.
1.5.Since both stairs will be used as escape routes, their location will be as far as possible from the container travel path. To give the engineer the possibility to choose for a safe position in the reefer rack, the container travel path will be marked within the reefer rack.
1.6.On all floor levels fixtures for clipping on safety harnesses will be included in the construction. This will ensure the safety of the reefer rack engineer when having to reach over the handrail when connecting/disconnecting reefer racks.
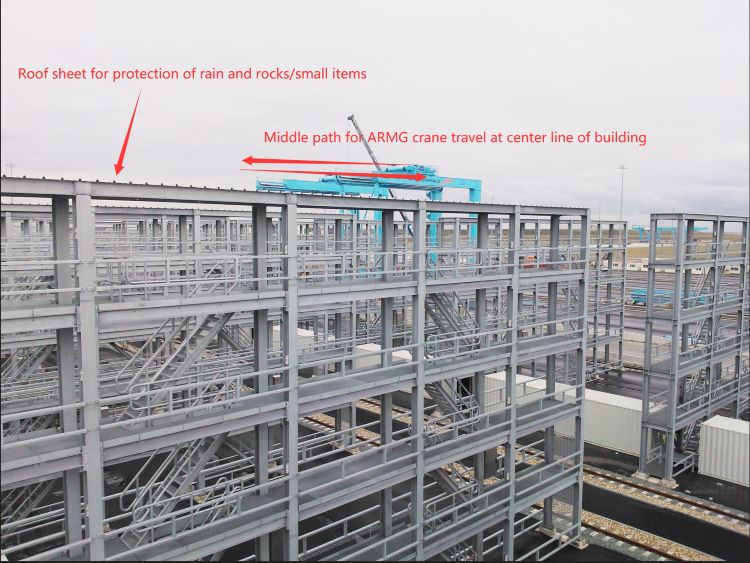
2.1.Handrails shall be provided at the following locations: Inspection Point
(a) Around the perimeter of each elevated level and at ground level
(b) Around the stair opening at each level
(c) On both sides of each stairs
2.2.Handrails shall be 1,100mm high, shall have a top bar, mid-height bar and a base kick plate. Inspection Point
2.3.The perimeter of the reefer rack (including at ground level) shall be closed with fullheight mesh or chainlink fencing (in addition to handrails), except for the side(s) where access to the reefer containers is required, which shall be closed with only handrails as above. Inspection Point
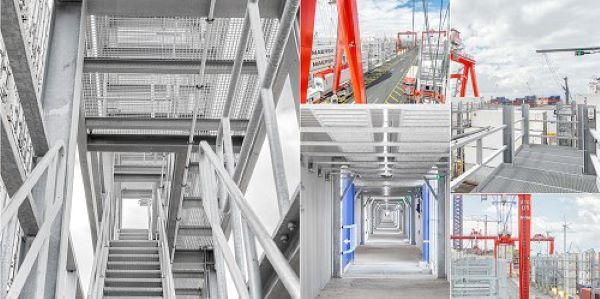
3.1.Each reefer passage shall have an access gate located at the ground level, at the narrow end towards the car parking place. Location indicated on the Definition Drawing. The access gate shall be inward opening, self-latching, and self-closing by heavy duty, low maintenance gravity/spring action. Inspection Point
3.2.The entire length of pedestrian access corridors, all joints between sections of reefer passage (if relevant), and the perimeter of all reefer racks shall be contained by handrails and/or fencing. The boundary of the access corridors which face onto stacking areas, crane rails or other automated equipment tracks/corridors shall be contained by mesh or chain-link fencing as indicated on the Definition Drawings. Inspection Point
3.3.The access point(s) for technicians to enter the automated area / reefer passage / access corridor system shall be defined by the Employer, and each point shall be closed with an access gate. Inspection Point
3.4.Where the access corridor connects with or crosses each reefer rack, the corridor shall be continuous without interruption through the reefer rack at ground floor level. Fixed handrailing with an access gate shall be mounted across the width of the reefer rack to physically segregate the access corridor from the operational area of each reefer rack.. Inspection Point
3.5. All access gates shall be inward opening, self-latching, and self-closing by heavy duty, low maintenance gravity/spring action. The height and structural form of the gate shall match the handrail or fence into which it is set. Inspection Point
3.6.Access control points with IT connections shall be provided at: Hold Point
3.7.Swipe cards shall be used to allow access through each access control point listed above, except for the emergency exits, to indicate when technicians are working in a particular rack and/or passing through the passage/access corridor. The system shall be linked to the ECS (Teams) and/or Safety system ARMG (ABB), and/or Access control system (securitas)to control the safe movement of automated equipment, including whenever an emergency exit has been opened. Hold Point.
3.8.Emergency exits shall be provided at maximum 60m centres from each row of reefer passages and dedicated access corridors. All accessible areas shall have at least 2 access/egress points. Emergency exits shall open outward toward the road / maintenance aisle via a gate with a quick-opening facility (e.g. fire exit type push bar). They shall be a minimum of 900 mm wide and freely accessible (e.g. no fixtures or electrical panels impeding access) and clearly signposted. Inspection Point The gate shall be linked to the crane operations via the access control system, so that if the gate is opened the crane is immediately immobilised. Hold Point
3.9.The details of the access control system, including gate locations, shall be as per Contractor’s design, based on the principles of the existing terminal.
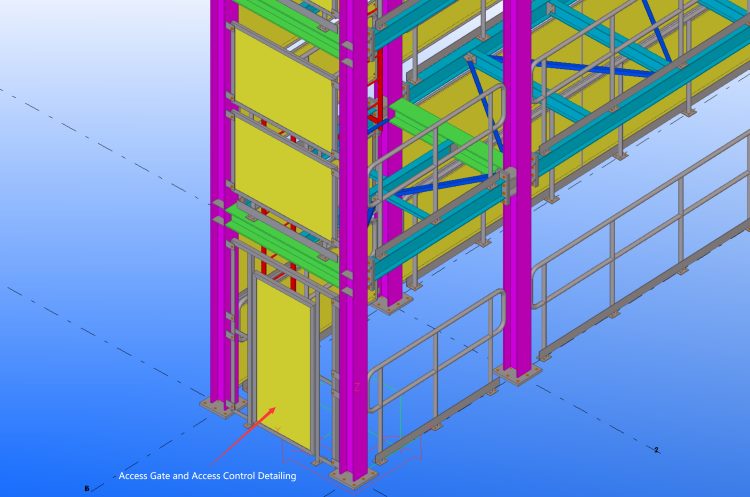
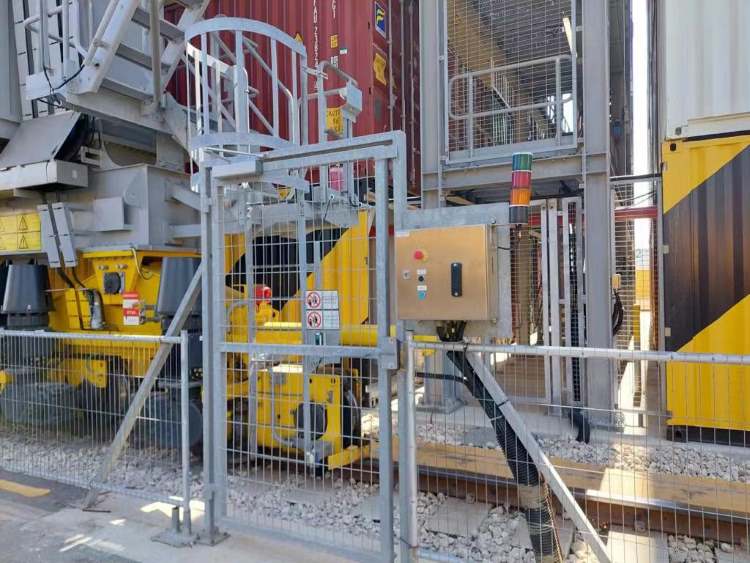
4.1.Stairs shall be designed so that they are comfortable and safe to use in accordance with EN 13586 and ISO 14122. The minimum width of the stairs (clearance between the handrails) is to be 700mm as indicated by BS EN ISO 14122 Part 3 section 5.7. The angle of the stairs shall not be more than 45°.Inspection Point
4.2.The riser height and tread width shall satisfy the requirements of local building codes.
4.3.The steps of the stairs can be grating of the same type as the flooring on each level. The edges of the steps shall be serrated to further reduce the chances of slipping.Inspection Point
4.4.To minimise the staircase opening on each level, the opening shall commence at a vertical distance of 2050mm from the stairs.
4.5.Longitudinally, the stairs location will nominally align with the 2nd row of containers. On the ground level, the stairs shall not terminate less than 2.5m from the end of the reefer frame.
4.6.The stairs shall be orientated to facilitate rapid exit of personnel in the case of emergency. Inspection Point
4.7.Transversely, for single-sided reefer racks the stairs shall be located on the opposite side from the reefer plugs (to leave maximum space for a corridor). For double-sided reefer racks the stairs shall be located centrally.
4.8.Where reefer passages are required, stairs on the ground level shall be positioned to ensure there is no obstruction of access to the passage or the stairs, including allowance for any gates or other access control. Inspection Point.
4.9.Particular attention shall be paid to detailing at the top and bottom of all flights of stairs to avoid trip hazards. Inspection Point
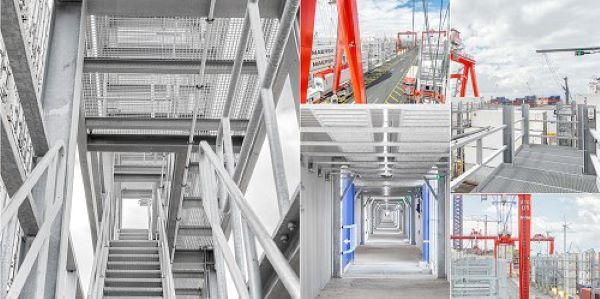
5.1.The flooring on each level (except the ground level) shall be steel galvanised grating which affords the reefer technician a view of the levels below. The grating shall be formed of serrated bars or other non-slip finish. The nominal grating size will be no greater than 30mm x 30mm. Inspection Point
5.2.The method of clamping or bolting the grating to the structural frame shall not cause a trip hazard. Inspection Point
5.3.The finished surface of the flooring shall flush and continuous across each level, with no steps, ramps or trip hazards. Inspection Point
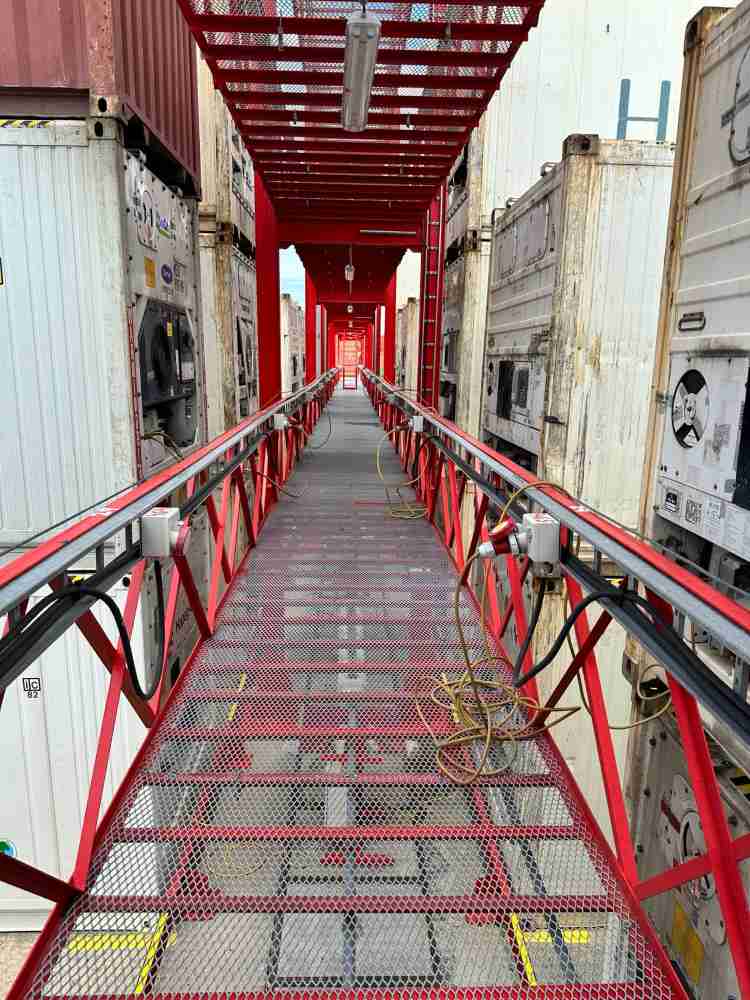
6.1.The roof shall be made of galvanised sheet steel with a minimum 5% cross-fall from the apex for run-off of rainwater. The sheet steel shall be minimum 4mm thick for durability. Inspection Point
Part 7: Nameplates and Signs
7.1.Reefer rack numbering and safety signs will be painted on the reefer racks as per the specific requirements of the Terminal, which will be provided by the Terminal:Inspection Point
Part 8: Electrical Fittings
8.1.The structure shall be designed to accommodate the following electrical fittings, for which the detailed requirements are specified in Part I “Reefer Racks”:
a.Plug sockets positioned approximately in line with one side of each container. Sockets may be mounted on bespoke brackets bolted to the steel frame adjacent to a container slot. Sockets shall be fixed between 1.0m and 1.4m above floor level, and shall be oriented so that cables trail parallel to the handrail (not across the walkway). Inspection Point
b.A main reefer rack power panel to supply all electrical equipment installed on the reefer rack. Inspection Point
c. Cable trays running longitudinally along each level, and vertically to connect the cable trays on each level. Inspection Point
d. Lighting and emergency lighting fixtures for all levels. Inspection Point
e.Automated lights on the exterior of the reefer rack to indicate to the container equipment operators when reefer technicians are working in a particular rack.
The indicator lights shall be located on the end face of the reefer racks (i.e. narrow end, away from the containers) and shall not extend more than 200mm
from the face of the rack. Inspection Point
8.2.Cable trays, conduits, cabling, electrical panels and other fixtures shall not project beyond the outside perimeter of the steel frame. Where vertical cable trays or conduits pass between levels, openings shall be provided in the floor grid. Inspection Point
8.3.All supports, brackets, cable trays, etc. must be integrated into to the structural design and completed before painting. Inspection Point
8.4.Lighting fixtures shall typically be mounted to the underside of the roof / flooring on each level and not on the columns. On the top level, if no roof is provided, then fixtures may be mounted on the posts for handrails and/or plug sockets. Inspection Point
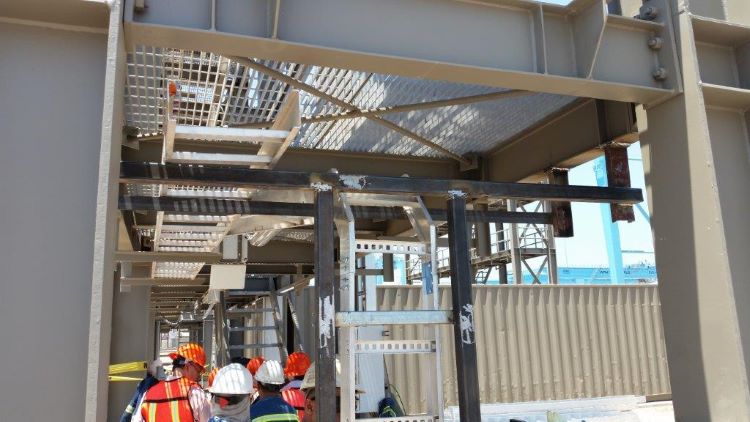
9.1.The metallic structure shall be earthed in accordance with Part G “Earthing”.
Would you like to see more information and images of ZHM’s steel sructure reefer rack Support Buildings ? Visit our Photo Gallery.
HOW CAN WE HELP YOU?
ZHM’s world-class team — together with our raw material suppliers and subcontractors — works to solve your most challenging design, engineering, farbrication or construction issues.
Contact ZHM by telephone at +86 135-8815-1981 or send us your questions via email to info@zhmsteelworks.com
- Pre:None
- Next:Steel Reefer Rack Detailing De 2024/5/17