Planning Your Build in Metal Steel Structures
No Pics.
A guide to pre-construction planning for a metal building project
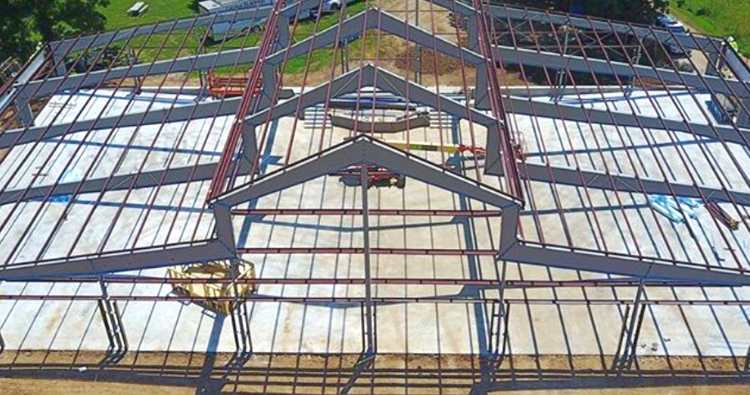
Index On This Page
Building Orientation
Site Selection
Building Size
Bay Spacing
Building Height
Framed Openings
Planning a Construction Project
This section will help you think about your chosen construction site and building options, such as floor plan, size, height, and openings (for doors and windows). You’ll need to consider not only what the building is for now but what you might also want to use it for in the future. If you can, seriously consider going bigger. The number one comment we hear from customers is.... “I wish I had chosen a slightly larger building.”
Pre-construction planning will ensure project efficiency and save you a lot of money trying to change things around mid-project with expensive change orders or once the building is in place.
Think about every detail, right down to the exact number, placement, and size of doors, windows, location of electrical outlets, etc. An experienced contractor can provide invaluable assistance with aspects of the project that you may easily overlook.
Building Orientation
Prevailing wind directions and sun exposure may be important, depending on your intended use. The building orientation can make a large difference to your building’s energy efficiency and to your ongoing heating and cooling costs. And natural light may be important, depending on the building’s purpose.
For example:
-
Do you want to have the sun shining in the windows in the morning, early afternoon, or early evening?
-
The low winter sun can help warm the building through south-facing windows, but you may need to shade the building from the higher summer sun with a roof overhang or taller shade trees. Deciduous trees can provide great shade in the warmer months while still allowing solar heat exposure in the colder months when their leaves have fallen.
-
Will you need insulation and air conditioning?
-
Might you want to eliminate windows and doors from one side that may get regularly buffeted by the rain and wind?
-
Is there a view that should be considered?
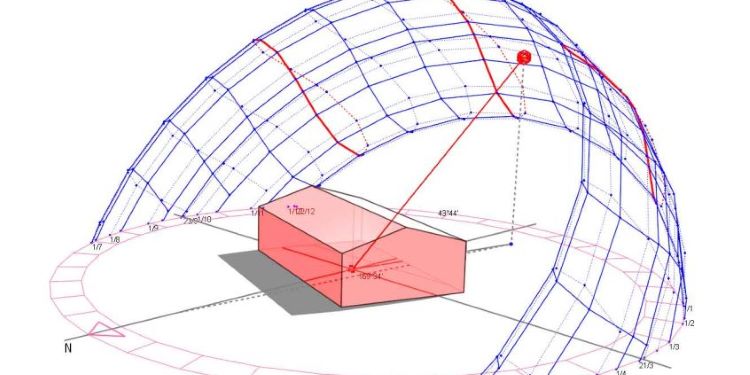
Building Orientation for Sun and Shade
Credit: ZHM Huawu Steel ©
Site Selection & Construction Site Planning
Steel buildings always require a foundation; the type of foundation will depend upon the intended end use of the building. Foundations often consist of custom-designed footings, but sites with poor soil might require deep foundations – drilled shafts or piles. Such deep foundations might exceed the cost of the building itself, so a preliminary site investigation is a must. Agricultural buildings with dirt or gravel floors often use concrete piers. For a detailed discussion, see our guide to metal building foundations.
At the building site planning stage, you’ll also need to consider:
-
Can the site be easily accessed? This applied both to the delivery of the building kit and for usage. (Remember that delivery and construction might require much higher clearance than the final use).
-
Is the ground firm and level? A sloping site introduces extra complexities to the design and construction. A building kit typically assumes that the site is level.
-
Does the site naturally drain well? Drainage issues need some investigation if you see multiple large puddles after it's rained.
-
Is access to utilities and services, such as electrical, gas, water, sewer, and the Internet, available?
-
Is the ground suitable for a septic field (if that applies)?
-
Is there room for possible future expansion?
Steel Building Size
(Note: Unlike standard home dimensions, steel frame building dimensions are measured between the outer surfaces of the exterior wall girts — essentially, these are OUTSIDE dimensions.)
Building Layout
One of the first steps will be to take an inventory of the proposed space-use requirements, e.g.,
-
For garages & shops: How many vehicles do you need to store? Will you need a dedicated workspace? Will you require office space or a bathroom?
-
For metal homes: What size of living space do you need? How many bedrooms? How many bathrooms? Do you need covered decks or porches? How much storage space do you need? Will you require an attached garage?
-
For shop houses: What square footage do you need for shop space? What height clearances do you need in the shop for access? For the house portion, how many bedrooms do you need? Do you have sufficient space to have the shop house on one level, or will you need a second level to reduce the overall footprint?
-
For warehouses: How many loading docks do you need? How high will inventory racks be? Will you require office space with bathrooms?
-
For horse barns: How many horse stalls do you need, and what size should these be – 10x10 or 12x12? Do you need a wash rack and tack storage area? Will you need storage for machinery and equipment?
-
For farm storage barns: What equipment will be stored in the barn, and what clearances will be required to allow easy access? Will it be more convenient to have large doors at each end for access? What type of doors will allow for the most convenient access? How wide should the barn be to allow for easy stacking of produce or feed?
Plan your layout by drawing it on graph paper, each square representing 5 feet. Place cutouts of the items you want to store in the building on paper to get an idea of what will work best for your particular setup.
While, in theory, a pre-engineered steel building could have an unlimited length and width, some specific considerations relate to various types of primary frames:
-
A single-span rigid frame's maximum unobstructed clear span could reach more than 60meters. Still, its most economical range is between 20m and 40meter. Above 120 feet, multispan rigid frames (with some interior supports) tend to become more economical.
-
The width of multispan rigid frames can reach 100m or even more, as limited by the selected roofing and siding options, the building location, the presence of heating and cooling systems, and other factors.
-
Major pre-engineered building manufacturers are rarely interested in buildings smaller than 9m by 12m. For buildings smaller than this, it might be more economical to choose conventional wood framing.
-
Steel buildings come in a vast range of sizes and shapes. Building dimensions are often provided in increments of 10 feet, e.g., 6m x 9m or 20 x 30m. Standard steel building sizes include: 30x40, 30x50, 40x60 and 50x100 .You might save money by choosing a standard size, but a steel building can be EXACTLY the size you need.
For larger buildings, you’ll need to consider the maximum clearspan (i.e., the span without intermediate supports), height, and the possibility of future expansion. A building with interior support columns (multispan) may cost less than a similar building with single-span rigid frames but be less versatile and convenient.
Points to consider when sizing your building:
-
How big is your proposed building site?
-
What is your budget?
-
Would you want to expand in the future?
-
Are there any zoning, HOA, or building-code restrictions related to building sizes?
-
For single-span rigid frames, the clear span (width) has a larger impact on the cost than the building length, so for such buildings, it might be more economical to reduce the width of your building and maximize its length.
See our list of common standard metal building sizes.
Steel building size and dimensions
Credit: ZHM Huawu Steel ©
Bay Spacing for Metal Buildings
Primary steel frames are the “skeleton” of pre-engineered buildings. The frames include columns and rafter beams bolted or welded together. The frames can also include bracing, web stiffeners, and base plates, as required by design. The frames support secondary framing: roof purlins and wall girts.
The spacing between two parallel frames is called a 'bay.' The bay spacing has an impact on price. The most common bay spacing in pre-engineered buildings is 25’ (20’ bay spacing is also available), which is often the most cost-effective and economical span for typical 8-inch roof purlins. The bay spacing could be smaller for heavier roof loading or larger for different purlin sizes. Sometimes, the bay spacing is smaller in the last bays of the building to reflect structural considerations.
Non-standard spacing of the primary frames might sometimes be needed to reflect any unusual usage requirements. For instance, if a huge side-entrance opening must be in a specified place, the adjacent frames are placed on each side. If you require this for your specific application, specify 'portal frame' construction when placing your order.
Again, this type of custom design will add to the final cost of the structure.
Bay Spacing for Metal Buildings
Credit: ZHM Huawu Steel ©
Building Height
Height needs to be considered carefully, so ensure you have sufficient clearance for your intended needs. Your specific requirements will determine your final building height. Here are some points to consider:
-
Will you have large and tall equipment?
-
Will you need access for oversize vehicles?
-
If your intended use is for an auto shop, will you use a car lift? If so, what clearance will you need?
-
Will you need a mezzanine for additional interior space?
-
Will you need a loading dock for deliveries, and if so, what size trucks do you need to offload?
-
For warehousing, what height are your storage racks, and what clearance do you need?
-
Are you planning to have overhead cranes in the building?
The applicable local building code will specify the maximum allowed height for various building types. Beyond that, the height will depend on architectural and engineering considerations.
Based on the type and style of the building and its proposed use, you can calculate the minimum required eave height. For example, airplane hangars must use clear-span framed openings and frames with high roof clearance. Churches may need high vaulted ceilings to give a feeling of loftiness. A standard eave height of 9-12 feet for residential buildings is usually sufficient.
The height for metal buildings is specified as the eave height (see diagram below). The eave is the point where the sidewall meets the roof. Typical building eave heights range from 3m to 10m, but they could be 12m and higher if needed by the building’s use (this will require special engineering).
The roof should be high enough to accommodate anything that might come into the building, such as construction equipment, farm machinery, an RV with an air conditioning unit on top, and so on. See more about the types of openings below.
Framed Openings
A “framed opening” is any opening in the building larger than a pipe penetration. There are framed openings around doors, windows, and louver vents. There are also larger openings through which vehicles, large equipment, and loading items pass. For example, a garage doorway would be considered a framed opening. Similarly, schools, retail stores, and manufacturing facilities often have a loading bay area, closed off by a large overhead or roll-up door, which trucks can back up to deliver and receive large inventory items.
There are various types of doors, such as:
-
Overhead, which moves on a track under the ceiling
-
Roll up, which rolls into a coil when opened
-
Sliding, similar to those in residences
-
Hangar doors with rollers, moving similar to sliding doors
See our metal building doors page for more on the most popular door options.
If practical, position doors away from prevailing winds for durability and to reduce heating and cooling costs.
Framing Components for Steel Buildings
Credit: MBMA
A Critical Decision BEFORE Ordering a Building
Primary frame columns can be ordered with tapered or straight profiles. Columns with a tapered profile are less expensive, while straight columns allow for a more straightforward application of interior wall finishes. Straight columns also maximize the interior space. Since many steel buildings DO NOT have interior wall finishes, most companies will supply the less expensive tapered columns unless you specifically order straight columns. Just something to keep in mind before you place your order.
Straight Vs tapered columns for steel buildings
Straight Vs tapered steel building columns
Credit:
Would you like to see more information and images of ZHM’s Metal Steel Structure Buildings ? Visit our Photo Gallery.
HOW CAN WE HELP YOU?
ZHM’s world-class team — together with our raw material suppliers and subcontractors — works to solve your most challenging design, engineering, farbrication or construction issues.
Contact ZHM by telephone at +86 135-8815-1981 (wechat and whatsapp) or send us your questions via email to info@zhmsteelworks.com