Refrigerated Container Racks Reefer Racks
refrigerated container racks reefer racks
Electric Refrigerated Container Racks: Technical Analysis
Introduction
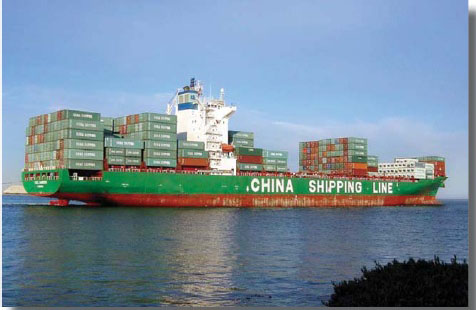
Background
Many container terminals at any given time have hundreds or thousands of reefers awaiting a ship,truck or train for export or import out of or into the area. Typically these reefers will wait for 24–72 hours with their engines running in order to maintain cold temperatures for the goods inside. Depending on how they are transported, reefers are powered by diesel engines or electricity.
Diesel Reefers
Diesel-powered reefers, or diesel reefers, have been the standard for perishable food truck transport in the world. With 2-liter engines ranging in size from 30 to 40 horsepower, these diesel engines are run anywhere from 1,000 hours to 7,200 hours per year depending on type of operation. For this study’s purposes, we will assume an average use of 3,000 hours per year. When powered by diesel generators, reefer containers can be major fuel consumers. At an average usage rate of 3,000 hours per year, annual diesel consumption would be 2,205 gallons per reefer peryear (at an average rate of 0.735 gal/hr). At a diesel price of $1.87 per gallon, a total of $4,123 is spent on fuel to run that reefer every year.
Every gallon of diesel consumed is associated with harmful pollutants emitted by the diesel engines.Particulate matter (PM) from diesel exhaust has been of increasing concern because of respiratoryissues linked to it. As of 2008, newly manufactured diesel reefer engines are becoming cleaner due to the U.S. Environmental Protection Agency’s (EPA) Tier 4 engine standards, required for all transport refrigeration units (TRUs), the diesel engines that run diesel reefers. PM standards for a 25–50 horse power engine, for example, were substantially reduced for Tier 4 engines, from 0.6 g/kWh to 0.03 g/kWh.
However, given the life cycle of an average TRU of 7-15 years, there are many Tier 2 TRUs still operating. For a facility operating 1,000 Tier 2 diesel reefers an average of 3,000hours each year, annual PM emissions from these reefers are estimated to be 24.4 tons and annualcarbon dioxide (CO2) emissions are estimated to be 29,330 tons per year.
This compares quite significantly to the average passenger vehicle, which emits about 5 tons CO2 per year.
Diesel reefers can also be associated with in efficiencies, as a diesel engine is required to be in a constant state of operation in order to keep the container cool. Reefers have two primary cycles of operation:
• Pull-down mode—rapidly getting the reefer down to the desired temperature for pre-loading or when it is first loaded
• Maintenance mode—continuous maintenance of desired temperature
Pull-down mode accounts for a very small percentage of a reefer’s operational cycle—as little as 5% according to some reports, yet requires the majority of the engine power. During pull-down,a diesel engine on a reefer will consume an estimated 1.4 gallons of diesel per hour. Maintenance mode accounts for the majority of a reefer’s operation. During this phase, a diesel reefer engine will consume an estimated 0.7–0.9 gallons of diesel per hour depending on the reefer model and use.
Electric/Hybrid Electric
Electrically powered reefers, or electric reefers, used extensively in the shipping industry, are powered by electrically driven components, which are in turn powered by electricity. When stationary at the dock, these units are plugged into grid power at an electrical terminal, and when in motion on a ship, they are powered by a ship’s electricity generators. When moving over the road, reefer containers require a mobile power source, or genset. An alternative to a full electric reefer is the hybrid electric reefer in which a small diesel engine serves as the source of power when electric power is not available.Electric reefers typically operate on 400 volt, 32 AMP, 3-phase, 60 Hz power with a maximum electrical load of 18 kVA. Step up power transformers can be used if either 308 VAC or 230/240VAC power sources are present. Depending on cargo and temperatures, a high capacity electricreefer uses, on average, 12–15 kWh of electricity in pull-down mode and 2.25 kWh during normaloperation, for an average of 2.8875 kWh per hour.
There can be several advantages to electric reefers compared to diesel, including:
• Reduced operational costs
• Lower emissions
• Reduced maintenance costs
Although the capital costs of electric compared to diesel reefers may be higher—as much as 10% higher when comparing the purchase prices of the two—this cost premium has been estimated to be recouped quickly with operating cost savings, depending on electricity and diesel pricing. At the 2009 national average commercial/institutional price of no. 2 ultra low sulfur diesel at $1.87 pergallon of diesel and the July 2010 national average commercial retail price of electricity at 10.70cents/kWh,annual fuel costs associated with reefer operations can be four times as high with dieselcompared to electricity (Table 1).
Table 1. Annual Fuel Costs: Electric verses Diesel Reefer
|
Diesel Reefer | Electric Reefer |
Average Fuel/Electricity Usage |
0.735 Gal./Hour |
2.8875 kWh/Hour |
Average Hours Operated/Year |
3,000 |
3,000 |
Price |
1.87/Gal. |
$0.107/kWh |
Cost to Operate Annually |
$4,123 |
$927 |
Assumption: 95% maintenance and 5% pull-down
In addition to fuel costs, there are land and lift costs associated with reefer operations at ports and inter-modal facilities. These costs, as they relate to electric reefers and the storage strategies that may be employed to keep cargo cold while reefers are awaiting transport at ports, will be discussedin the next section.
Electric Reefer Storage
Traditionally, electric reefers awaiting transport are parked lined up side-by-side at a port terminal,each plugged into their own electrical outlet. These containers typically have been wheeled into theterminal via truck chassis, or off-loaded from a ship by a crane and then wheeled to a parking spot by a yard truck where they are then plugged into grid power while they await further transport. A relatively new alternative to wheeled reefer operations has come into play at some ports—the refrigerated container rack system, known simply as reefer racks. This strategy allows for approximately two dozen electric reefers to be stacked—commonly four high by six or seven wide—in a rack, sharing electrical infrastructure and allowing for land space efficiencies. Both of these strategies will be discussed further below.
Wheeled Reefer Storage System
In a wheeled reefer export operation, refrigerated containers are delivered to the port or inter-modal facility by truck or train, are parked and plugged into an electrical outlet (Photo 2) at a parking sloton terminal for later pick up by a yard truck and ultimate loading onto a ship by a crane. A wheeled reefer import operation is similar, but actions are reversed. The wheeled operation requires relatively few movements of the container, from truck/rail to ship or vice versa, translating into lower operating expenses.
In this type of operation, the port owns the land that the parking slots occupy and is responsible for developing and maintaining the electrical infrastructure associated with these slots. Typically ports charge for electrical usage at each slot, in addition to “rent”, a fee for the use of these parking slots on a per day basis. While operationally efficient, the wheeled electric reefer strategy is land-intensive, requiring a 10x40 foot land footprint for each 40-foot container parked. In the port industry, where land is often expensive and in short supply, any means of reducing land requirements translates to lower operating expenses.
Rack Storage System
The reefer rack system (Photo 3), an alternative reefer storage system, may offer such a savings, depending on land costs and type of operation. In an electric reefer rack system, instead of being driven to a parking spot by a truck, the electric reefer to be exported is dropped off by the truck/train and thenplaced by a container handler (e.g., top pick or rubber tired gantry crane) into one of two dozen spaces in a custom-built rack that may hold 22–26 electric reefers. The reefer is then plugged in and awaits loading onto a ship. Later, it is removed from the rack by a container handler and transferred to yard truck and then to a crane which then loads it onto ship.The reefer rack, because it is custom built, can accommodate any sized refrigerated container. The rack’s electrical system is centralized at one end of each rack, simplifying access for maintenanceand hook up. Each of the rack parking slots has its own electrical hookup, which workers access via platforms and ladders. Although it requires additional handling compared to the wheeled system, the reefer rack has the advantage of being land efficient, taking up a footprint of 320 square feet for four 40 foot containers, compared to a 400 square foot per container footprint associated with a wheeled system. Whereland costs are high, this footprint savings can translate into cost reductions for reefer owners who pay rent on reefer parking spaces.
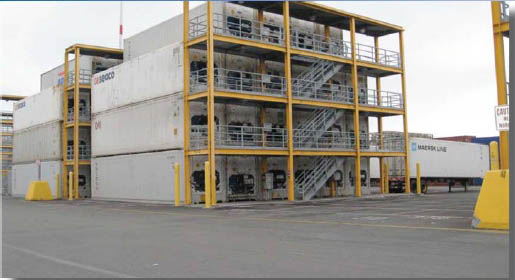
Photo 4:ZHM Steel Installation Report of Belgium Antwerp Reefer Rack Steel Structure Project(CE Certified,Eurocode), April,2024
- Pre:Refrigerated Container Racks R 2024/4/24
- Next:Steel Structure Introduction D 2024/4/23