How to Design and Fabricate Steel Structure Beams
How to Design and Fabricate Steel Structure Beams
Home » Steel Building » How to Design and Fabricate Steel Structure Beams
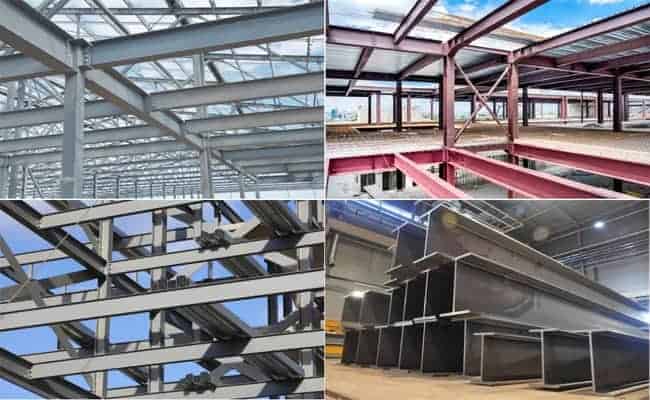
steel structure beams
Table of Contents
2.Design steps for steel structure beam:
2.1. Determine the structural scheme:
2.2. Determine the height of the beam:
2.3. Section selection of the beam:
2.4. Check the strength of the beam:
2.5. Check the overall stability of the beam:
2.6. Check the stiffness of the beam:
2.7. Check the local stability of the beam:
2.8. Structural design:
3.Steel structure beam fabrication
4.Shipping and Splicing of Steel Beams
5.Steel beam installation requirements
Classification of steel structure beams:
According to different manufacturing methods, beams can be divided into section steel beams and composite beams.
Section steel beams include hot-rolled and thin-walled cold-formed steel beams. Hot-rolled steel beams are often used for I-beams, channel steels, H-beams, etc. Thin-walled cold-formed steel beams are commonly used with C and Z-shaped steels, mainly for roof purlins and wall girt with small beam spans and loads. The processing of section steel beams is simple, but the steel specifications limit the cross-sectional size. Therefore, when the load and span are large, the composite beam should be used when the steel section cannot meet the strength, stiffness, and stability requirements.
Steel plates weld composite beams. Commonly used welded composite beams are H-shaped cross-sections and box-shaped cross-sections. H-section beams are the most widely used, and the manufacturing process is simple. On the other hand, the manufacturing process of box-section beams is more complicated, and the material loss is significant, but it has more excellent bending and torsional strength.
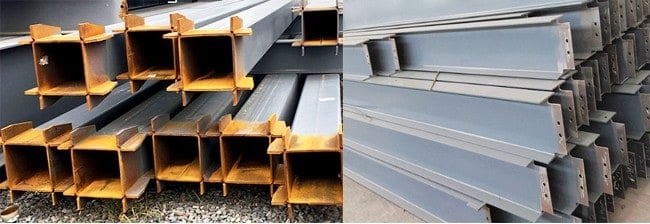
steel structure beams
Design steps for steel structure beam:
1. Determine the structural scheme:
2. Determine the height of the beam:
3. Section selection of the beam:
4. Check the strength of the beam:
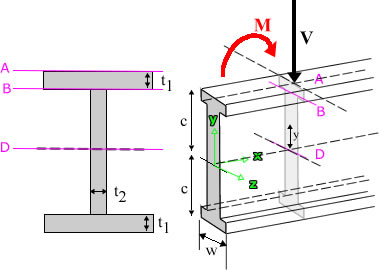
5. Check the overall stability of the beam:
Some beams are under load, although the maximum normal stress, shear stress, and converted stress of the section are lower than the strength design value of the steel. However, the deformation of the beam will suddenly deviate from the original bending deformation plane, and lateral bending and torsion will co-occur. This is called the global buckling of the beam. The severity of the overall instability of the beam must be given full attention. Sudden destabilization failure has the same consequences as brittle steel failure and has no warning in advance. When determining the structural scheme and selecting the beam’s cross-section, it is necessary to prevent the possible overall instability of the beam. It is not economical to wait until the checking calculation to find out that there is a problem, and it is too late to increase the cross-section of the beam.
6. Check the stiffness of the beam:
According to the process conditions or use requirements, the ratio of the deflection of the beam to its span should be limited. The code stipulates the maximum allowable ratio for beams of various purposes. The minimum height obtained from the stiffness condition has been considered when selecting the beam’s size. In general, the stiffness checking calculation can meet the requirements.
7. Check the local stability of the beam:
8. Structural design:
Steel structure beam fabrication
Assembly: The cut steel plate must first be fixed into the designed shape, such as an H or box shape. The body can use the steel structure assembly machine to fix the web and flange by electric welding.
Welding: After the steel beam is assembled, it needs to be welded, and the welding is usually submerged arc welding. Welding requires firm welds, no cracks, no defects, and meets the requirements of relevant standards and specifications. Distortion after welding needs to be corrected by flame or equipment.
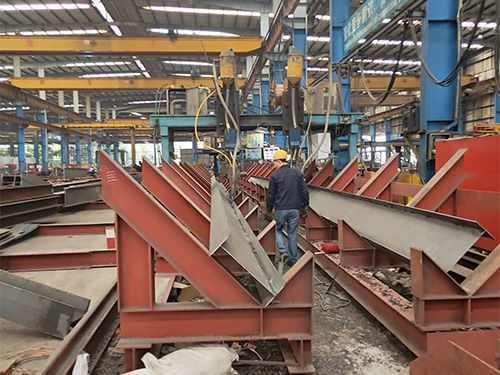
Processing: deep processing of welded steel beams. Includes perforations, breakouts, welded stiffeners, and end plates.
Surface treatment: surface treatment, including derusting, painting, hot-dip galvanizing, and other processes, to prevent steel from rusting and corrosion.
Shipping and Splicing of Steel Beams
Limited to transportation conditions, the beams are fabricated in sections at the factory, transported to the construction site, and then spliced into a whole, called on-site splicing. Due to insufficient steel dimensions, the splicing done at the manufacturing plant by lengthening or widening the individual members of the beam is called factory splicing. The joints should not weaken the strength of the shaft and ensure the continuity of deformation.
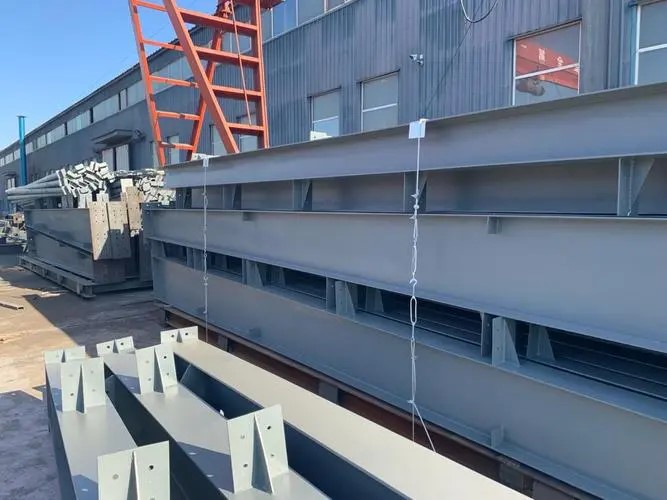
Steel beam installation requirements
To ensure safety and prevent the sharp edge of the steel girder from cutting the wire rope, the wire rope must be protected. The angle of the sling is not less than 450.
Before hoisting the steel beam, a safety rope should be installed on the steel beam. When boosting, hang two sliding ropes at both ends of the steel beam. Two people hold two sliding strings, respectively. Steel beams must be hoisted slowly. To ensure safety, personnel cannot stand directly under the beam. Place unique cloth bags for high-strength bolts at both ends of the steel beam. When the steel beam is hoisted above the in-place position, the steel beam is in place. The falling speed of the steel beam is controlled at 3m/min. Arrange two installers at each end to prepare for steel beam installation. When the steel girder was close to being in place, two installation workers held the upper flange of the steel girder with their hands, dragged it into place, and prepared to install high-strength bolts.
- Pre:None
- Next:Steel Structure Gymnasium The 2024/4/26