Expansion Joint in a Steel Structure Building
Expansion Joints: Where, When and How
Table of Contents:
1. General Requirement
2.Expansion Joint Size
3.Structural Roof Systems
4.Overhead Crane Buildings
5.Large Clear Span Structures
6.Special Details
7.Construction Concerns
8. Example 1 400' long braced Frame
9. Example 2: Expansion Joint Size
10. Reference.
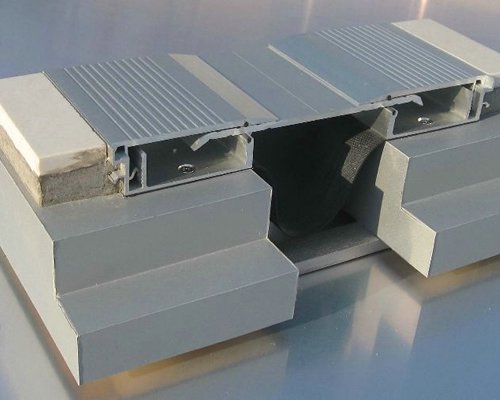
In the most basic sense, the need for an expansion joint in a structure depends on the consequence of not having an expansion joint. Will the lack of an expansion joint hamper or destroy the function of the facility, or cause damage to the structural or architectural components? The number and location of building expansion joints is a design issue not fully treated in technical literature. The LRFD Specification (AISC, 1999) lists
expansion and contraction as a serviceability issue and provides the statement in Section L2, “Adequate provision shall be made for expansion and contraction appropriate to the service conditions of the structure.”
ASCE 7-02 Minimum Design Loads for Buildings and Other Structures (ASCE, 2002) states, “Dimensional changes in a structure and its elements due to variations in temperature, relative humidity, or other effects shall not impair the serviceability of the structure.”
This paper will focus on the basic requirements used to determine whether an expansion joint is required at a given location, or locations within a structure. Requirements of expansion joints as they pertain to commercial, industrial, and long span structures are discussed. Area dividers as provided in roof membranes to control the effects of thermal loads for roofing are not discussed, as they are relief joints in the membrane and do not require a joint in the roof structure below.
General Requirements
Although buildings are often constructed using flexible materials, roof and structural expansion joints are required when plan dimensions are large. It is not possible to state exact requirements relative to distances between expansion joints because of the many variables involved, such as ambient temperatures during construction and the expected temperature range during the life of a building. The National Roofing Contractors Association (NRCA, 2001) gives the following recommendations for the location of roof expansion joints:
➜ Where steel framing, structural steel, or decking change direction.
➜ Where separate wings of L, U, and T shaped buildings or similar configurations exist.
➜ Where the type of decking changes; for example, where a precast concrete deck and a steel deck abut.
➜ Where additions are connected to existing buildings.
➜ At junctions where interior heating conditions change, such as a heated office abutting an unheated warehouse, canopies, etc.
➜ Where movement between walls and the roof deck may occur.
It should be noted that the NRCA standard details show that the roof structure under roof expansion joints is intended to be discontinuous.
The Building Research Advisory Board of the National Academy of Sciences (NAS, 1974) published Federal Construction Council Technical Report No. 65: Expansion Joints in Buildings (no longer in
print). When other conditions prevail, the following rules are applicable:
1. If the building will be heated only and will have hinged-column bases, use the allowable length as specified.
2. If the building will be air conditioned as well as heated, increase the allowable length by 15% (provided the environmental control system will run continuously).
3. If the building will be unheated, decrease the allowable length by 33%;
4. If the building will have fixed column bases, decrease the allowable length by 15%.
5. If the building will have substantially greater stiffness against lateral displacement at one end of the plan dimension, decrease the allowable length by 25%.
When more than one of these design conditions prevail in a building, the percentile factor to be applied should be the algebraic sum of the adjustment factors of all the various applicable conditions.
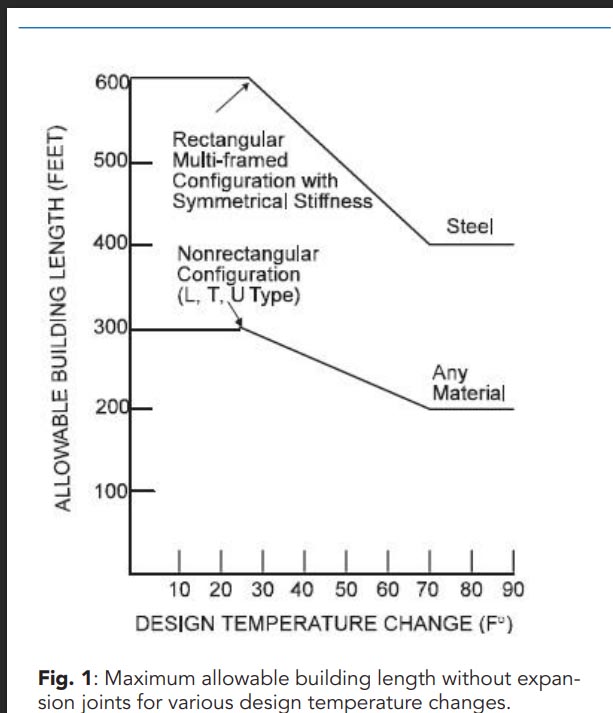
Fig. 1 Expansion Joint Spacing Graph [taken from F.C.C. Tech. Report No. 65, Expansion Joints in Buildings].: Maximum allowable building length without expansion joints for various design temperature changes
Rectangular multi-framed configuration with symmetrical stiffeness
Nonrectangular configuration L T U Type
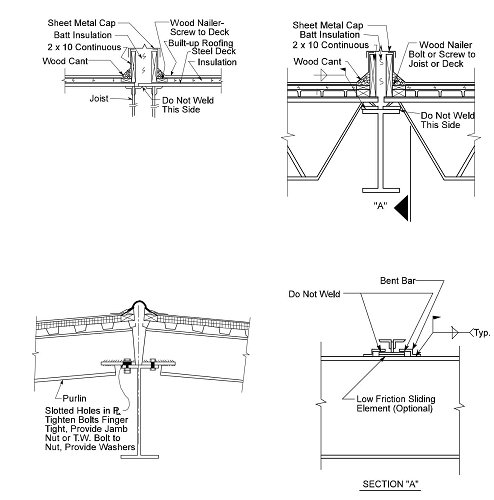
Fig. 2 Typical Expansion Joints.
Sheet Metal Cap, Batt Insulation, 2x10 Contineuous wood cant, Do not weld this side, wood nailer-screw to deck built-up roofing insulation
Sheet Metal Cap, batt insulation, 2x10 continuous, wood cant,
Purlin, Slotted holes in PL tighten bolts finger tight, provide jamb nut or T.W. Bolt to nut , provide washers,
Low friction sliding element(optional, Bent Bar Section A
The report also includes temperature data for numerous cities. (This data is reprinted in Appendix B of the complete paper. For the complete paper, please see www.modernsteel.com or the 2005 NASCC Proceedings at www.aisc.org.)
Tw is the temperature exceeded only 1% of the time during summer months; Tm, the mean temperature during the normal construction season; and Tc , the temperature exceeded 99% of the time during
winter months. The design temperature change is the larger of the two temperatures differences either (Tw-Tm) or (Tm-Tc).
Rather than consulting the above values, many engineers use a temperature change of 50 °F to 70 °F for enclosed heated/air-conditioned buildings.
In equation form, the NAS requirements given above can be shown in Eq. 1 as follows:
where:
Lmax= maximum length of a building with no expansion joints or between expansion joints
R1 = 0.15, if the building is heated and air-conditioned
R2 = 0.33, if the building is unheated
R3 = 0.25, if columns are fixed base
R4 = 0.25, if the building has substantially greater stiffness at one end Lallow = allowable length from Fig. 1
As a general rule, expansion joints should always be carried through the roofing membrane.
Regarding the type of structural expansion joint, most engineers agree that the best expansion joint (and generally the most expensive) is to use a line of double columns to provide a complete
separation in the building frame at the joints. When joints other than the double column type are employed, low friction sliding elements, such as Teflon pads, are used between the faying surfaces. It
should be remembered that slip connections are not totally frictionless. In addition, they may induce some level of restraint to movement due to binding or debris build-up.
Very often, buildings may be required to have fire walls in specific locations. Fire walls may be required to extend above the roof or they may be allowed to terminate at the underside of the roof.
Such fire walls become locations for expansion joints. In such cases, the detailing of joints can be difficult because the fire wall must be supported laterally.
The designer is also cautioned that when roof diaphragm forces are to be transferred into shear walls or vertical Xbracing systems, the transfer should be accomplished mid-way between expansion joints allowing edge members to expand and contract freely away from the fixed point of resistance.
Expansion Joint Size
The width of an expansion joint is determined from the basic thermal expression for the material used for the frames in the structure, ∆ = αL∆T. Where α =0.0000065 for steel structures, L is the length subject to the temperature change, and ∆T is the temperature change.
∆T is based on the design temperature change, (Tw-Tm) or (Tm-Tc ). The change during the construction cycle, (Tm-Tc), is usually the largest.
Structural Roof Systems
Metal roofs are of two types: Through Fastener Roofs (TFR) and Standing Seam Roofs (SSR). Standing seam roofs, for the purpose of this discussion, include only those of the floating type. Standing seam roofs without the floating feature should be treated as through fastener roofs.
Through fastener roofs rely on purlin roll to prevent slotting of the roof panels and to relieve thermal force build-up.Because of their greater lateral seat stiffness, steel joists should not be used with through fastener roofs, except in rare instances such as small roofs. A practical limit between expansion joints for TFR is in the range of 100’ to 200’, when these roofs are attached to light gage coldformed purlins.
Standing seam roofs are limited by the range of the sliding clips. Depending on the manufacturer, it is in the range of 150’ to 200’.
Standing seam roofs are more flexible in the direction perpendicular to the ribs, as compared to the direction of the ribs. Thus, expansion joints can be spaced at greater distances than those perpendicular to the ribs. The roof manufacturer’s recommendations should be consulted and followed relative to the distances between expansion joints.
Overhead Crane Buildings
Vertical bracing for wind, seismic, or crane longitudinal runway forces should be located at or near the center of the runway length. Expansion and contraction can then occur away from the brace location. This will help prevent the permanent elongation of the vertical bracing due to temperature changes. The disadvantage of the center placement of the bracing is that bumper forces have to be transferred a greater distance to get to the bracing as compared to braces that are located near the crane stops.
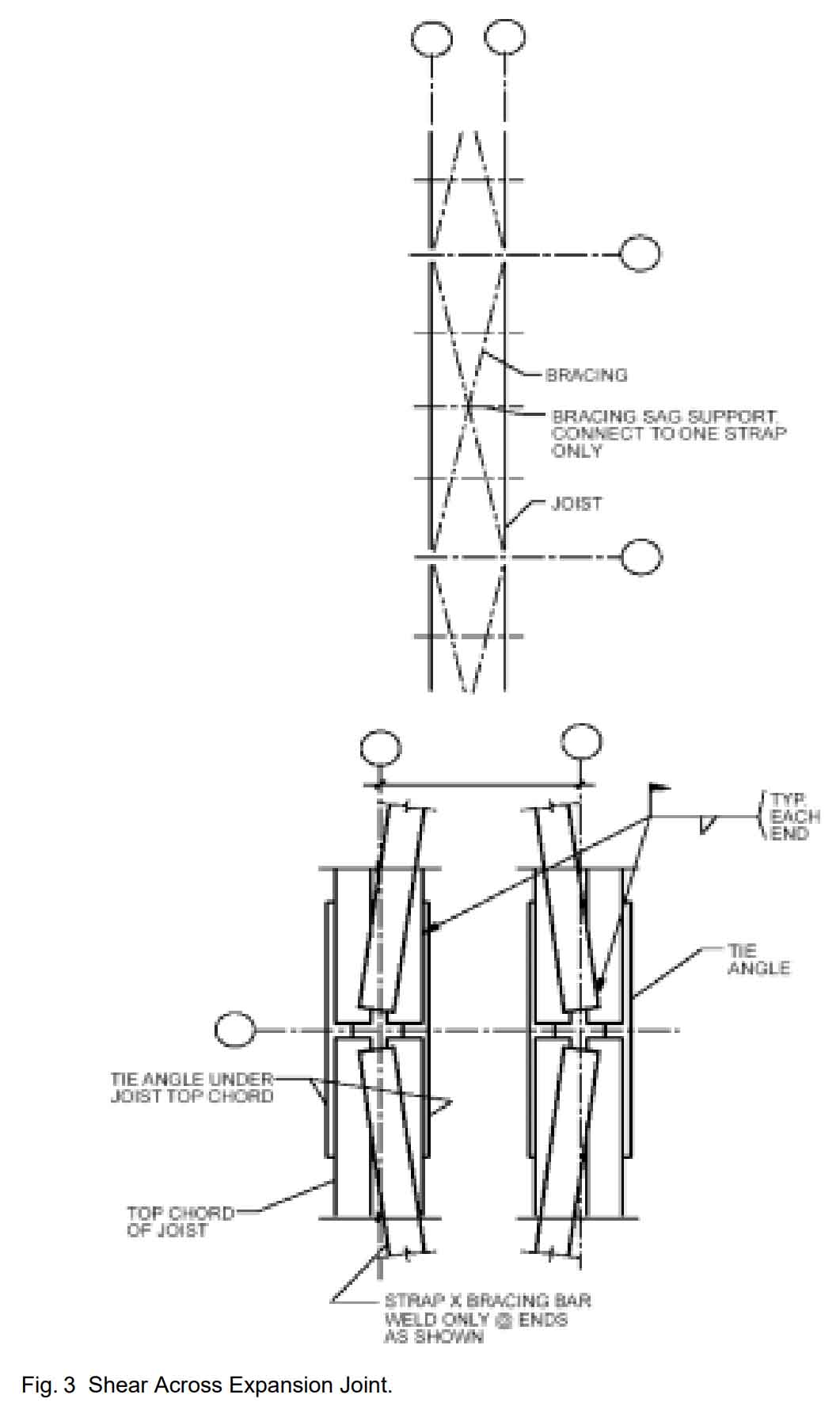
Only as a last resort should expansion joints be provided for runway beams. By providing oversize holes at the beam ends, expansion and contraction can be allowed in each beam segment so that an expansion joint is not necessary. If an expansion joint is provided in the runway system, careful consideration must be given as to how the lateral crane forces are transferred across the joint. Special details are required to prevent high shears in the crane rail and large forces in the rail clamps.
Crane rails: Expansion joints should never be provided in the crane rails. Such joints often lead to rail cracking. In lieu of such joints, the rail should be allowed to expand toward the stops. Adequate space must be allowed between the end of the rail and the face of the crane stops. In addition, a rail clamping system which allows longitudinal expansion and contraction of the rail must be provided, particularly in runway systems which exceed 400’ in length.
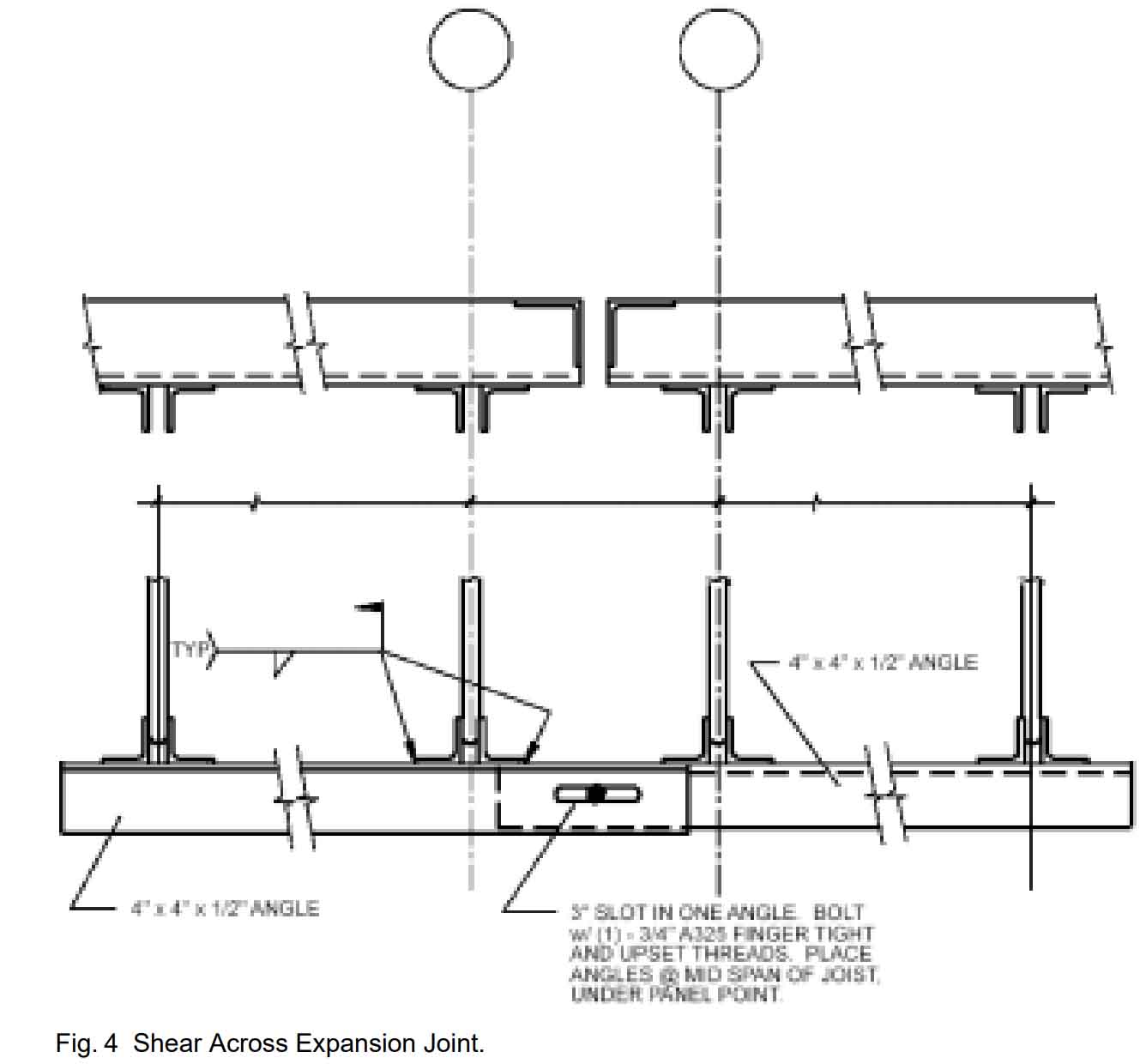
Long span structures and components often require special expansion joint hardware. The majority of bearings only have expansion and contraction capabilities of plus or minus 1”. Bearings that have smooth stainless steel surfaces can be specified for much grater expansion and contraction amounts. Slide bearings generally have a coefficient of frictions from 0.04 to 0.08. The bearings can accommodate pressures from 2,000 to 4,000 psi. Manufacturers of slide bearings can be found on the web. The manufacturer should be consulted for proper
ordering and installation procedures.
Special Details
On occasion, special expansion joint details are required to transfer shear across the expansion joint.
Construction Concerns
The author has experienced several issues relative to construction difficulties associated with expansion joints. The first is that temperature changes to which an unenclosed unheated structure is subjected to during construction may exceed the design temperature changes after completion of the structure. These increased temperature changes should be considered by the designer. The temperature to be considered during construction, of course, varies depending upon building location. Engineers often use a maximum value of 70 °F for calculation purposes. A more accurate value to use is the Tm-Tc value from the NAS Report.
Sometimes it is very difficult for the steel erector to adjust the expansion joint at the desired location, as normal erection tolerances may force the expansion joint to one end of its travel. This problem can be eliminated if the designer considers a detail at the far end of the member to which the expansion joint is located, as a means of adjustment. In this way, the construction tolerance can be compensated.
Example 1: 400’-Long Braced Frame
Determine whether a rectangular 400’by 180’, unheated building with pinned base columns requires an expansion joint.The building has X-bracing at one end only in the two side walls along the 400’direction. The building is located in Buffalo, NY. From the Appendix: For Buffalo, NY: Tw = 88, Tm = 59, Tc = 3
Design temperature change is the maximum of (Tw-Tm) or (Tm-Tc ). Substituting, the design temperature change is the maximum of (88-59=29) or (59-3=56).
∴Use 56 °F
From Equation (1):
With:
R1 = 0.15, the building is not heated and nor air-conditioned, N.A.
R2 = 0.33 the building is unheated
R3 = 0.25 the columns are fixed base, N.A.
R4 = 0.25 the building has substantially greater stiffness at one end
From Fig. 1, Lallow = 450’
Lmax = 450+(0.0-0.33-0.0-0.25)(450)=189’
Therefore, an expansion joint is required. Because the building has a braced frame, and the bracing is at only
one end of a typical frame, additional bracing will be required on both sides of the expansion joint.
Example 2: Expansion Joint Size
∆ = 0.0000065L∆T
= (2)(0.00065)(200)(56/100)
= 0.146’ = 1.75”
∴Use 2” total movement The above calculation assumes that the thermal movement for each segment
occurs away from the X-braced bays. ★
REFERENCES
American Institute of Steel Construction, 1999, Load and Resistance Factor Design Specification for Structural Steel Buildings, Chicago, IL.
American Society of Civil Engineers, 2003, Minimum Design Loads for Buildings and Other Structures, ASCE 7-02, ASCE Reston, VA.
Federal Construction Council, 1974, Technical Report No. 65, 1974, Expansion Joints in Buildings, National Research Council, Washington, D.C. (out of print).
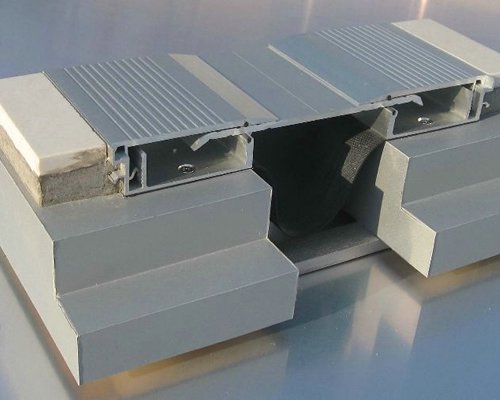
- Pre:None
- Next:Expansion Joint Considerations 2024/4/26