Steel building interiors-A guide to finishing metal building interiors
No Pics.
A guide to finishing metal building interiors
1.Add Insulation
2.Interior Framing
3.Wiring & Plumbing
4.Sheathing
5.Flooring
6.Final Inspection
But most buildings require some degree of finishing. Below we discuss:
- Insulation,
- Interior framing,
- Wiring and plumbing,
- Sheathing,
- Flooring, and
- The final inspection
A Critical Decision BEFORE Ordering Your Building
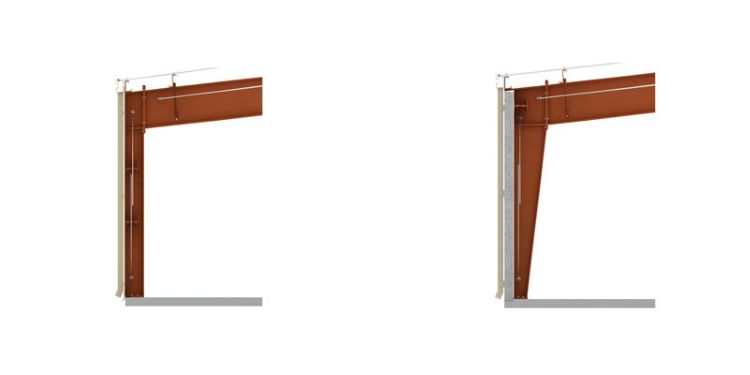
Straight Vs Tapered Steel Columns
Add Insulation
Additionally, insulation, combined with an effective vapor retarder, will help reduce condensation in your building, thus protecting your building materials from mold, rust, and decomposition.
Common insulating materials are fiberglass, foam board, and spray foam. Fiberglass is the most common and affordable option. For more details on the various options, see our page on metal building insulation.
In wood-framed construction, insulation is placed between the studs. In a metal frame building, the insulation will usually be installed outside the framing to provide continuous coverage to eliminate thermal bridging by highly conductive metal parts. You can also fill the wall and roof cavity for increased insulation.
What type of insulation is best for you will depend on the climate in your area, the purpose of the building, and what type of work, if any, will be done inside. For example, there is a fire risk if the building has exposed spray insulation and then welding is done close to that insulation.
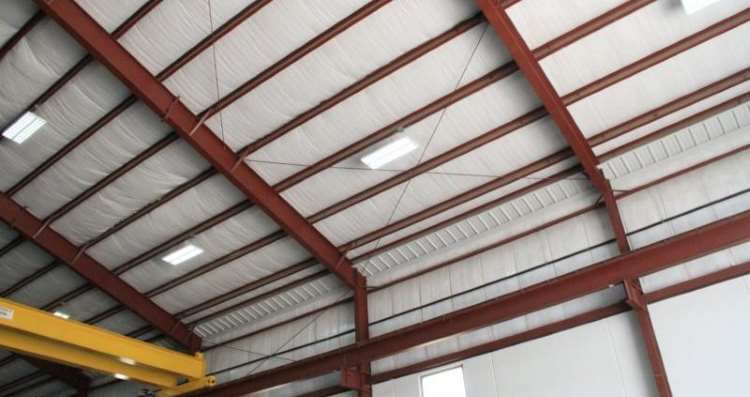
Installed insulation in a metal building
Get Four Building Quotes
Compare & save with competing quotes from local suppliers
Get Local Cost
Interior Wall Framing - Wood or Metal
Partitioning of Your Building
See our sample metal building floor plans page for ideas to design a simple layout. Alternatively, you can work with an architect or specialized contractor who will assist with your plans. Or design the layout yourself, as modern software makes it easy to configure the inside of your building to suit YOUR needs.
Make sure to tell your building supplier if you plan on hanging things from the ceiling or walls (fire sprinkler system, HVAC, etc.) as they may need to factor in extra dead load for the structure.
Steps in Constructing the Framing
1. Build the frame for walls. This is easier to do on the floor to ensure the frame will be vertical.
2. Add studs to the frame. These provide strength and stability and support the drywall and fixtures.
3. Add framing for doors and windows.
4. Raise and secure the frames. You will fasten the wall studs to the girts that run horizontally between the main columns, 400mm or 600mm on centers with 75mm self-drilling screws.
5. Add ceiling framing (beams and joists), if needed.
6. Add electrical, mechanical, and plumbing fixtures.
7. Install drywall or other wall finishing on the studs.
Again, be sure to inform your building supplier if you intend to add sheetrock to the walls, as they may need to factor this additional dead load into the building.
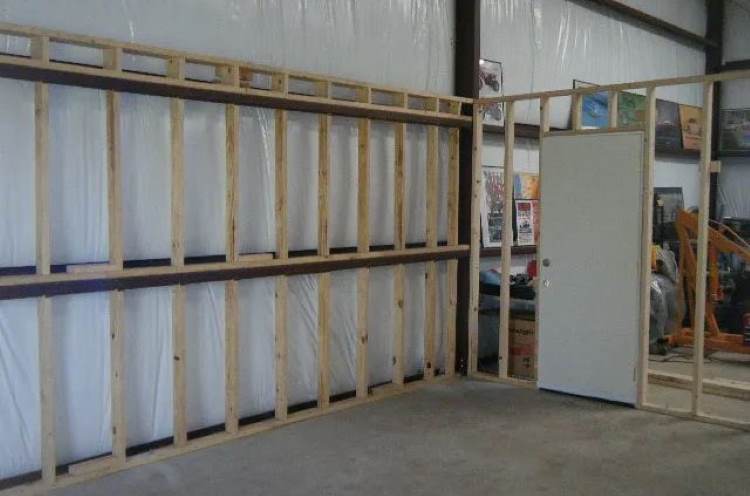
Interior framing a steel building with lumber studs
Interior framing with lumber studsSteel Studs Compared to Wood
- More durable and resistant to rot
- Stronger
- More dimensionally consistent and straight
- Better for moisture-prone areas such as bathrooms
- More difficult to cut
- In some areas, not as easy to find as wood studs (2x4s or 2x6s)
- Greater cost
- More difficult to attach electrical boxes and trim
- Drywall installation is more complicated
- Conduct more heat, unless a thermal gap is included in the construction
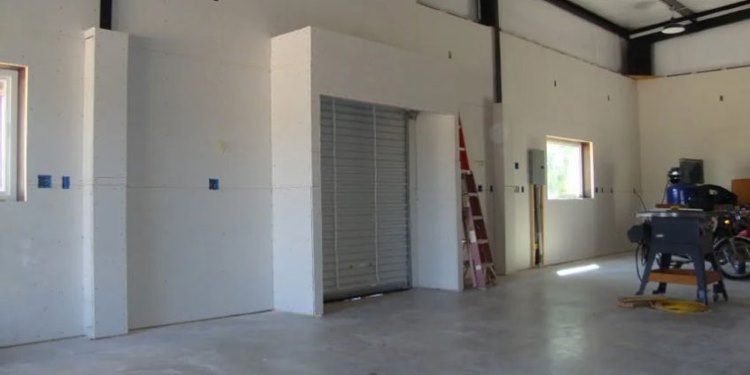
Wiring and Plumbing
Plan Ahead
You’ll need to decide on the conduit size, wiring gauge, outlets, and lighting. You’ll need to anticipate what equipment might be used simultaneously, so you don’t keep tripping breakers. You’ll also need a conduit bender.
Install Wiring
You can also pull it through. Using a little “parachute” string, you can get the string through with compressed air and then use the string to pull wiring. It’s easier than it might sound.
A Trick for Stranded Wiring
Cut around the insulation to strip, but don’t completely remove it. Slide almost to the end of the wire, so about an inch of copper is exposed. Twist the stranded wire opposite to the way it came. Wrap the wire clockwise around the screw and tighten. Then trim the end of the copper wire and insulation. Quick, easy, tidy.
Test Prior to Powering On
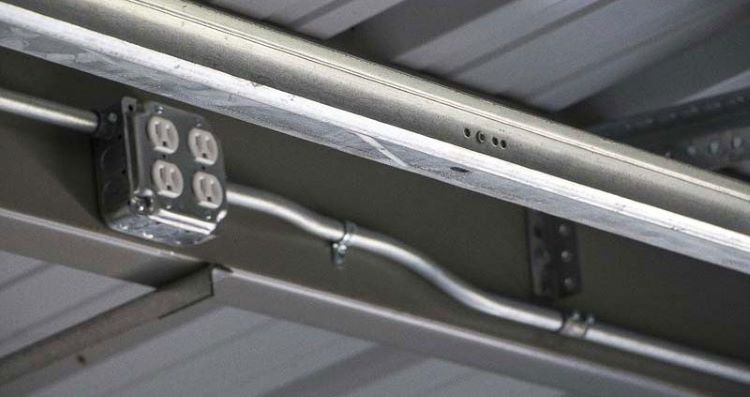
Get Four Building Quotes
Compare & save with competing quotes from local suppliers
Get Local Cost
Wall Sheathing
Apply Interior Finish – or leave Exposed Metal Walls?
However, there is a huge caveat here. Most metal buildings are not designed to be sturdy enough to support interior drywall or other brittle finishes without cracking. If you plan to have such interior wall and ceiling finishes, specify this BEFORE ordering the framing, as the manufacturer would have to provide a custom structure designed to much more stringent deflection criteria than a regular metal building. The sturdier building would cost more, of course. If you add drywall finishes to a building not designed for those, the building movements will eventually damage the interior finish.
Types of Interior Finishes
If you choose drywall, plywood, or related materials, ensure the bottom edges are kept clear of the floor. You won’t want any future spills to be wicked up into the walls and cause damage.
You might need an appropriate flame retardant primer and paint. This is another topic where you need to check on local code requirements.
The following are the most common finishes. Other types of finishes are possible if you have access to other kinds of materials. But these are the most used and the best for most purposes.
Drywall
- The attractive, smooth finished look, common in offices, commercial spaces, or homes
- Fire resistant
- Easy to damage in a working space (but easy to repair if damaged)
Plywood
- Easy to install
- Strong. Easy to mount tools or shelves.
- Warm look
- Can be painted
- Easy to repair if damaged
- More costly
OSB (oriented strand board)
Advantages:
- Cheaper than plywood
- Can mount tools and shelves
- Might not be as strong as plywood
- Cannot be painted
- More absorbent than plywood
Steel Liner Panels
- Easy to install
- Most durable
- Easy to clean
- Possible to repair or replace if damaged (a professional crew would likely be needed)
- While suitable for more industrial-type buildings, it provides a very attractive and finished look
- More costly
Ceiling Options
No ceiling: Leaving the steel framing exposed will give a more industrial look, with the high ceiling giving a more roomy feeling. The vapor retarder will act as a finish.
Drop ceiling: A drop ceiling will give a more comfortable feeling to buildings such as offices, retail spaces, community centers, and homes.
As stated at this section's beginning, DO NOT add the drop ceiling as an afterthought. It should be specified before the building is ordered.
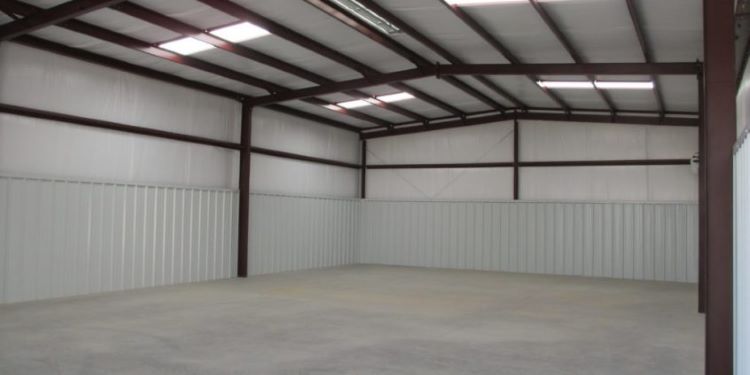
Flooring
The vast majority of steel-frame buildings have bare concrete floors. But you could have stained concrete, epoxy, vinyl flooring, and more. It all depends on what the building will be used for and how durable the floor needs to be.
This is one of the topics where we’d recommend a discussion with your building contractor and perhaps an architect or structural engineer.
Final Inspection and Walkthrough
But remember the pilot who got sucked most of the way out of the cockpit when the window blew out. Yes, it’s really true. Most people would think the cause impossible – that no sane person could be so stupid as to have used improper bolts while not following the procedure, but that is exactly what happened.
So we’d like to encourage you to think of inspection as a wise and potentially life and business-saving check on the work done.
Formal inspections should be carried out frequently throughout the construction process. At some critical stages, an inspection could occur as frequently as once daily. Again, this is a matter that your experienced building contractor will know about and take care of.
Small problems now could turn into much bigger problems later. And there could be huge liability issues. An inspection will give you peace of mind, knowing that all the materials are appropriate and the building has been assembled properly.
Would you like to see more information and images of ZHM’s Metal Steel Structure Buildings Interiors? Visit our Photo Gallery.
HOW CAN WE HELP YOU?
ZHM’s world-class team — together with our raw material suppliers and subcontractors — works to solve your most challenging design, engineering, farbrication or construction issues.
Contact ZHM by telephone at +86 135-8815-1981 (wechat and whatsapp) or send us your questions via email to info@zhmsteelworks.com